Key Takeaway
SIMATIC is Siemens’ brand name meaning “Siemens Automatic Industrial Control.”
Launched in the 1950s, SIMATIC covers a wide range of automation products including PLCs, HMIs, SCADA systems, distributed I/Os, software tools, and industrial PCs. It emphasizes seamless integration across manufacturing control, monitoring, and data processing. The SIMATIC range offers solutions from small machines (LOGO!, S7-1200) to complex plants (S7-400, PCS 7). Products under the SIMATIC brand are engineered for reliability, scalability, cyber-security, and digitalization readiness, supporting concepts like Industry 4.0. Today, SIMATIC represents Siemens’ commitment to providing fully integrated automation systems that simplify engineering, enhance production efficiency, and improve system connectivity in industrial environments worldwide.
Breakdown of “SIMATIC” as Siemens Automation Technology
SIMATIC stands for SIemens and MATIC, derived from “automatic.” In simpler terms, it refers to the automation technology developed by Siemens to control and monitor industrial processes. This brand has become a trusted symbol in factories and plants all over the world.
From PLCs (Programmable Logic Controllers) to HMI (Human Machine Interface) panels, the SIMATIC brand encompasses a complete ecosystem for automation. It’s built to handle everything from basic control tasks to complex production lines with multiple integrated systems.
Each SIMATIC component is designed to communicate efficiently with others—this ensures seamless operation, reduces downtime, and enhances productivity. So whether you are working with a small control panel or a sophisticated SCADA system, SIMATIC products ensure reliability and performance.
In essence, SIMATIC is not just a product—it’s a framework for intelligent automation.
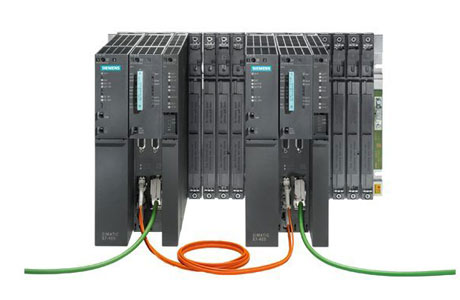
Legacy and Evolution of the SIMATIC Brand
The SIMATIC journey began in the 1950s, with Siemens launching its first control system. Since then, the brand has evolved in parallel with the rise of digital automation. Early SIMATIC systems relied heavily on relays and hardwiring. Fast forward to today, and you’ll find high-performance CPUs, touch interfaces, and cloud integration under the same brand.
One of the key milestones was the introduction of the SIMATIC S5 and later the S7 series. These PLCs changed the way factories controlled and monitored operations. Today, SIMATIC S7-1200 and S7-1500 controllers are known worldwide for their reliability and advanced features like integrated diagnostics, high-speed communication, and cybersecurity.
SIMATIC has always stayed ahead by adapting to technological shifts. When the industry moved towards digitalization, Siemens enhanced SIMATIC with TIA Portal (Totally Integrated Automation), enabling centralized configuration and programming. This adaptability is what makes SIMATIC future-ready.
Role of SIMATIC in PLCs, HMIs, SCADA
SIMATIC is the umbrella brand for Siemens’ automation hardware and software. It plays a major role in three key areas:
PLCs (Programmable Logic Controllers) – These are the brain of industrial machines. SIMATIC PLCs like the S7-1200 and S7-1500 offer fast processing, modularity, and integration with sensors and actuators.
HMIs (Human Machine Interfaces) – SIMATIC HMI panels allow operators to interact with machines through touchscreens, buttons, and displays. These interfaces are critical for status monitoring, fault alerts, and user commands.
SCADA (Supervisory Control and Data Acquisition) – For plant-wide control and data collection, SIMATIC SCADA systems like WinCC offer centralized dashboards, analytics, and historical data logging.
Together, these systems form a complete automation loop—from sensing and controlling to visualization and optimization. It’s why SIMATIC is seen as an all-in-one automation brand.
Global Recognition and Certifications
When a system carries the SIMATIC name, it automatically gains trust. Siemens is known for rigorous quality standards, and SIMATIC products are certified by international bodies like CE, UL, and IEC.
In many countries, SIMATIC has become a default standard in industrial automation projects. Engineers and technicians across the globe are trained on SIMATIC systems because of their prevalence and performance.
In addition to technical reliability, Siemens ensures that all SIMATIC products are designed with safety and sustainability in mind. Features like fail-safe PLCs, redundant systems, and energy-efficient modules underline this commitment.
This global reputation isn’t just based on branding—it’s earned through decades of consistent innovation and dependability.
SIMATIC’s Role in the Digital Enterprise Vision
As industries embrace digital transformation, SIMATIC plays a central role in Siemens’ Digital Enterprise strategy. It connects operational technology (OT) with information technology (IT) to create smart factories.
Using SIMATIC, manufacturers can integrate real-time data from the factory floor into enterprise systems. This helps in predictive maintenance, process optimization, and flexible manufacturing.
Tools like SIMATIC MindSphere and Industrial Edge are enabling data analytics and machine learning at the edge, making automation smarter and more responsive.
In short, SIMATIC isn’t just about automating—it’s about innovating. It helps businesses not just keep up, but lead in the Industry 4.0 era.
Conclusion
SIMATIC symbolizes Siemens’ vision of intelligent, integrated, and future-ready automation. It’s a name that has shaped industrial history and continues to drive digital progress.
For any new engineer stepping into this field, understanding SIMATIC is crucial—it’s the foundation of countless systems around the world. From PLCs and HMIs to cloud-connected SCADA solutions, SIMATIC delivers trusted automation.
More than just a product line, SIMATIC is a legacy that empowers industries to perform smarter, faster, and better. It’s where automation meets intelligence—and where your journey as an engineer truly begins.