Key Takeaway
An S7-1500 CPU can support up to 32 local modules (signal modules, communication modules, technology modules) directly attached to the CPU rack.
In larger systems, you can extend using ET 200SP or ET 200MP distributed I/O stations via Profinet or Profibus.
Different CPUs (like 1511, 1515, 1517, 1518) allow different maximum module counts based on available internal resources (memory, bus communication speed).
Additionally, communication processors (CPs) and redundant setups may slightly alter the expansion capabilities.
Always consult the Siemens hardware manual or TIA Portal configurator for exact module limits per CPU type and firmware version.
Modular expansion enables large, scalable automation systems while maintaining fast cyclic data exchange and real-time process control.
Rack Size and Module Limitations per CPU Type
The first thing to know is: not all S7-1500 CPUs are created equal. Each CPU type in the series—like the 1511, 1513, 1515, 1516, or 1518—comes with its own limits in terms of rack size and number of modules supported.
Here’s the hook: More powerful CPUs support more modules and larger setups. For example, a CPU 1511 might support only 8-16 modules on its central rack, while a CPU 1518 can handle 32+ modules or even more with extension racks.
Another point to remember is that the standard backplane (rack) supports 11 module slots. You can expand that further using extension racks, but the total module count will still be limited by the CPU’s capability and the address space available.
Always check the latest Siemens manual or TIA Portal for the CPU model you’re using. Module limits vary not just by hardware, but also by firmware version.
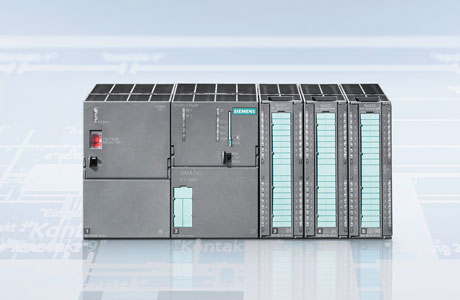
Digital and Analog IO Expansion Limits
In most automation setups, you’ll need a mix of digital input/output (DI/DO) and analog input/output (AI/AO) modules. But how far can you go?
Here’s where it gets exciting: depending on the CPU, you can connect hundreds of I/O channels. For example, CPU 1516 can support over 1000 I/O points, combining digital and analog.
However, the limitation isn’t just about physical slots. Each module consumes a certain number of process image bytes and address space. If your modules are too data-heavy, you might hit the logical limits before you run out of physical space.
Pro tip: If your system needs lots of I/O but your rack is filling up, consider remote IO like ET200MP using PROFINET. It expands your system without cluttering your main cabinet.
Communication and Function Module Considerations
S7-1500 PLCs are powerhouses when it comes to communication. But don’t forget: each additional communication or function module also occupies a slot, and they use up backplane bandwidth.
If you’re adding modules like PROFINET, PROFIBUS, or serial communication modules, plan wisely. These modules don’t use process image space like IO modules, but they still have load limits. Siemens refers to this as communication load in percent.
Also, if you use technology modules like high-speed counters, motion control modules, or weighing modules, you’ll need to consider both the number of slots and power draw.
Always calculate the load factor and check module compatibility, especially if you’re mixing standard and safety modules.
Power Supply and Current Consumption Planning
Here’s something many newcomers overlook: you can’t just keep adding modules without thinking about power consumption.
Each module draws power from the rack’s power bus, and the total current draw must not exceed the power supply’s rating. Siemens recommends checking load current per rack segment and using additional power modules or separate power supplies when necessary.
For instance, a large setup with multiple analog modules (which consume more current) might overload the central power bus. That’s why Siemens provides current consumption values for every module—use them.
This isn’t just a planning detail. If you ignore power limits, your system may fail intermittently, behave unpredictably, or even shut down under load.
Real-World Configuration Examples
Let’s bring this into perspective. Here are two real-world examples:
Example 1: Compact Automation Line
CPU: 1512SP
Modules: 4 DI, 4 DO, 2 AI, 1 communication module (PROFINET), 1 function module (Pulse Output)
Total: 12 modules – Fits perfectly in one rack. No issues with power or address space.
Example 2: Large Factory Process Control
CPU: 1518
Central Rack: 11 modules
2 Extension Racks: 10 modules each
Mix of DI, DO, AI, AO, Communication (PROFIBUS + OPC UA), Safety I/Os
Total: ~30 modules, with calculated power and communication load well under CPU limits
These cases show that smart planning makes anything possible, even with module limits.
Conclusion
The Siemens S7-1500 platform is built for flexibility. Whether you’re building a small machine or a massive plant automation system, understanding your module limits, rack configurations, power budgets, and I/O address constraints is key to long-term stability.
Always design with a balance of physical layout, power management, and CPU load in mind. Use TIA Portal to simulate your setup before building it physically. And never forget—more modules mean more responsibility.
Knowing these limits doesn’t restrict you. It actually empowers you to scale with confidence. Plan wisely, configure smartly, and your S7-1500 will handle complex automation like a pro.