Key Takeaway
The four main types of pressure gauges are Bourdon tube, diaphragm, capsule, and bellows gauges. Each operates on a different mechanical principle to measure pressure. The Bourdon tube gauge is the most widely used and works by flexing a curved tube when pressure is applied. Diaphragm gauges use a flexible membrane that moves in response to pressure changes, ideal for low-pressure applications. Capsule gauges, which are formed by two diaphragms welded at the edges, are also used for low pressures, especially in gaseous media. Bellows gauges expand or contract accordion-like metal tubes to measure pressure and are commonly used in HVAC and refrigeration. Selecting the right gauge type depends on the required sensitivity, pressure range, and media compatibility.
Overview of Pressure Gauge Classification
Alright, listen up. If you’re just stepping into the world of industrial instrumentation, the first thing you need to wrap your head around is how pressure gauges are classified. Think of pressure gauges like the eyes of any system dealing with air, steam, oil, or gas. They help operators see what’s happening inside the lines without opening them up.
Pressure gauges are broadly classified based on how they operate. The major categories include: mechanical pressure gauges (like Bourdon tube, diaphragm, capsule, and bellows types) and electrical/electronic pressure gauges that use sensors and signals. Mechanical types are super common in industries due to their durability, simplicity, and no-dependency on power.
Now, here’s a golden rule: the right gauge depends on what fluid you’re measuring, the range of pressure, and the type of environment. From boilers to compressors to chemical reactors, every application might need a different type.
Let’s explore the most common ones, starting with the OG of pressure measurement – the Bourdon tube gauge.
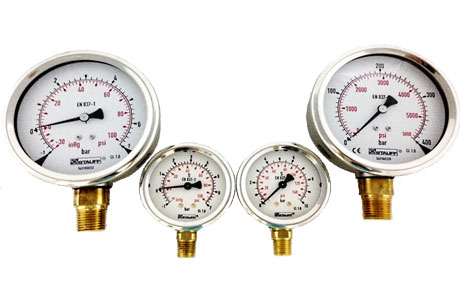
Bourdon Tube Pressure Gauge Explained
The Bourdon tube gauge is the most widely used pressure gauge in the world. Why? It’s simple, reliable, and works without electricity. It has been around since the 19th century, and it’s still rocking.
Here’s how it works: it has a curved, hollow metal tube inside. When pressure is applied, the tube tries to straighten out. That tiny movement is converted to a dial movement using gears and springs. You see the result on the dial – easy and fast.
You’ll find Bourdon gauges everywhere – on air compressors, steam lines, refrigeration units, and even on hydraulic presses. They can measure both low and extremely high pressures, ranging from vacuum to over 1000 bar.
They come in two basic types: C-type (most common, crescent shaped) and helical/coiled types (for higher pressures). The materials can vary from brass to stainless steel, depending on the media. If you’re working with clean, dry gases or liquids, this is your go-to.
Still, remember: they don’t like pulsation or vibration much. That’s where other types step in.
Diaphragm Pressure Gauge Basics
If your application involves corrosive fluids or you’re dealing with low-pressure ranges, diaphragm gauges are your best bet.
This type uses a thin, flexible membrane (the diaphragm) to sense pressure. The pressure difference on either side of the diaphragm causes it to flex. This movement is translated into a readable dial value.
Where do you see diaphragm gauges? In pharmaceutical plants, food processing, water treatment, and chemical industries. They’re great for measuring low pressures, starting from just a few millibar, and are perfect when the medium is thick, dirty, or sticky.
An added bonus? You can use chemical seals to isolate the diaphragm from the process fluid, making them extra durable. Plus, since the diaphragm can be made from Teflon, Hastelloy, or other exotic materials, they can resist aggressive chemicals.
Diaphragm gauges shine where Bourdon tubes may struggle – in terms of sensitivity and media compatibility.
Capsule and Bellows Gauges
Here’s where things get interesting – especially if you’re dealing with very low pressures, like in HVAC systems, medical equipment, or lab-scale setups.
Capsule gauges are designed specifically for low-pressure gas applications. They use two diaphragms welded together to form a capsule. When gas pressure increases, the capsule expands, and that movement is transferred to a pointer. Ideal for measuring pressure from 0-600 mbar.
Bellows gauges, on the other hand, use a concertina-like component (think of an accordion). When pressure changes, the bellows expands or contracts. Bellows types can measure slightly higher pressures than capsules and are often used in both vacuum and low-pressure monitoring.
These gauges offer excellent sensitivity and can detect even the smallest changes in pressure. However, they are not suited for harsh industrial environments where pressure spikes or vibrations are common.
So, if you’re in a clean lab, R&D setup, or working with delicate instruments, these are your go-to sensors.
Which Type Fits Your Industry?
Now you might be wondering – with all these types, how do you choose the right one?
Here’s a cheat sheet from the field:
Manufacturing Plants / Factories: Bourdon Tube Gauges – rugged, no-nonsense, can handle tough environments.
Chemical / Petrochemical / Pharmaceutical: Diaphragm Gauges – perfect for aggressive or sanitary media.
HVAC / Labs / R&D: Capsule or Bellows – ideal for low-pressure, precise monitoring.
Food / Beverage: Diaphragm with hygienic seal – easy to clean, bacteria-resistant.
Hydraulic and Pneumatic Systems: Bourdon again wins for robustness and simplicity.
And don’t forget: ambient conditions matter too. If you’re working in a high-vibration area or a place with high temperature fluctuations, go for liquid-filled gauges or add snubbers.
Conclusion
Choosing the correct pressure gauge depends on several factors: the medium being measured (liquid or gas), pressure range, environment (corrosive or clean), and required accuracy. Bourdon tube gauges are ideal for general industrial use, while diaphragm gauges suit corrosive or hygienic processes. Capsule or bellows gauges handle low pressures, and digital options offer precise monitoring with outputs for automation. Before selecting, assess the application’s conditions, mounting needs, and whether local or remote reading is needed. By matching the gauge type with your operating environment, you avoid breakdowns, ensure safe operation, and get reliable data. Always consult manufacturer datasheets and avoid over-specifying features that increase cost without benefit. Smart selection leads to long-term success.