Key Takeaway
There are four main types of mechanical pressure gauges: Bourdon tube, diaphragm, capsule, and bellows gauges. Each type is used depending on the application’s pressure range and media characteristics. However, considering electronic pressure measurement, there are also digital, piezoresistive, capacitive, strain-gauge, and piezoelectric pressure gauges. If we include specialty types, the total variety can exceed ten types, such as differential, vacuum, compound, and high-pressure gauges. The choice depends on factors like pressure range, required accuracy, operating environment, and whether the pressure is absolute, gauge, or differential. So, in industrial settings, pressure gauges can be broadly classified into mechanical, electrical, and digital categories with numerous subtypes.
Overview of Pressure Gauge Categories
Alright, let’s get into this. If you’re just stepping into the industrial world, one of the first instruments you’ll deal with is a pressure gauge. These little devices might look simple, but they play a massive role in keeping systems running safely and efficiently.
Pressure gauges come in many types, and each is built for a specific environment and purpose. At the most basic level, a pressure gauge helps you monitor the pressure of a gas or liquid in a system. If you’re working with air compressors, water lines, oil systems, or even chemical pipelines, you’ll see these gauges installed everywhere.
Now, pressure gauges can be broadly classified into two main categories: analog and digital. But even beyond that, we can divide them further based on application—industrial, lab-grade, and even food-grade. And under these, you’ll find specialized types like vacuum gauges, compound gauges, and differential gauges.
Each category has its role. Knowing which type to use (and where) is the kind of knowledge that will make you stand out in any plant or factory floor. So, let’s break them down clearly and simply.
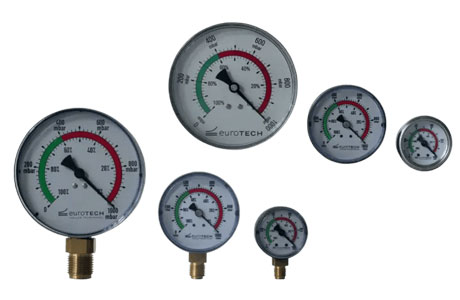
Analog vs Digital Pressure Gauges
Analog pressure gauges are the traditional dial-type ones. You’ve seen them. A needle rotates across a calibrated scale—very visual, very mechanical. No batteries, no fuss. These are preferred in rugged industrial settings where reliability matters more than digital precision.
Digital pressure gauges, on the other hand, come with an LCD or LED display. They often have added features like data logging, alarms, and high accuracy readings. They’re commonly used in lab environments or modern process setups that require tight monitoring and remote tracking.
So when should you choose analog over digital—or vice versa?
If you’re in a high-vibration environment or an area prone to electrical noise, analog is your friend. They’re simple, tough, and cost-effective. But if you’re doing detailed pressure diagnostics or integrating with a SCADA system, digital gauges make much more sense.
Both types have their space. The trick is in knowing which one fits your job best.
Industrial vs Laboratory Pressure Gauges
Industrial pressure gauges are made for harsh, often dirty, noisy, and high-vibration environments. Think of oil refineries, cement plants, heavy manufacturing, or power stations. The gauges here are built with rugged cases, shatterproof glass, and sometimes liquid-filled designs to dampen vibrations.
Lab pressure gauges, however, are used in controlled environments. Precision is key here. These gauges are designed to deliver highly accurate readings, sometimes even up to a fraction of a psi or bar. You’ll find them in R&D labs, pharmaceutical setups, or quality control departments.
Also, in labs, digital gauges are more common. These provide better resolution and can connect to data systems. But on the industrial side, analog still dominates because they don’t need power, can handle tough handling, and are easier to read at a glance.
So again, your environment will dictate the type of pressure gauge you need. Choose accordingly.
Sub-types: Differential, Vacuum, Compound, etc.
Differential pressure gauges measure the difference between two pressure points. You’ll need these when monitoring filters, pumps, or flow rates across systems. For example, in an air handling unit, you might use a differential gauge to check if a filter is clogged.
Vacuum gauges are designed to measure pressures below atmospheric pressure. These are essential in processes involving suction or vacuum systems like packaging machines, HVAC vacuuming, or distillation units.
Compound gauges are versatile—they can measure both positive and negative pressures (vacuum and pressure). These are great when your system goes below and above atmospheric pressure during different cycles.
There are also other types like absolute pressure gauges (measure pressure relative to a perfect vacuum) and sealed gauges (used in closed systems with sealed reference points).
Each of these has a very specific use case. So as an engineer, your job is to understand what the system demands and match it with the right sub-type
Specialized Gauges: Sanitary, Hydraulic, Refrigerant
Sanitary pressure gauges are used in food, beverage, and pharmaceutical applications. These gauges are designed to be cleaned easily and resist contamination. You’ll find tri-clamp fittings and smooth surfaces—basically, they follow strict hygiene norms.
Hydraulic pressure gauges are used in systems with high pressure and pulsation—like construction machinery, presses, and injection molding machines. These gauges are often liquid-filled to absorb shock and protect the internal mechanism.
Refrigerant pressure gauges are used in HVAC and refrigeration systems. They’re color-coded and calibrated for refrigerants like R-22 or R-410A, allowing technicians to monitor low and high pressure sides during charging or maintenance.
The point is, every industry has its own specific needs. And there’s usually a gauge type built exactly for that purpose. Knowing these specialized gauges will help you work more efficiently, avoid costly mismatches, and improve system performance.
Conclusion
Pressure gauges come in a wide range of types and specifications. From standard Bourdon tube gauges to specialized Magnehelic or digital types, each has unique benefits. Understanding this range allows you to make informed decisions based on your system’s requirements. For instance, differential pressure gauges are best for filter monitoring, while vacuum gauges are ideal for suction systems. Knowing the full range also helps avoid over-specification—saving cost—and ensures safety by preventing gauge overload or incorrect use. Categorizing gauges by function, accuracy, build, and media compatibility is essential. Whether for high pressure, low pressure, or differential reading, every situation has a best-fit gauge. Know your options to select confidently.