Key Takeaway
The three main types of pressure instruments are:
Pressure Gauges – These mechanically or digitally display the measured pressure, usually in real time.
Pressure Transducers (Sensors) – These convert pressure into an electrical signal, commonly used for monitoring and control in automation systems.
Pressure Switches – These detect whether pressure is above or below a certain threshold and activate/deactivate circuits accordingly.
Each serves a unique function. Gauges provide visual readings; transducers send data to controllers, and switches initiate actions (like shutting off a pump). Depending on your industry—HVAC, oil & gas, manufacturing, or pharmaceuticals—these instruments help monitor, control, and ensure the safety and efficiency of pressurized systems.
Pressure Gauges: Direct Reading Instruments
Alright, let me break it down for you. As a newly joined engineer stepping into the world of industrial instrumentation, the first thing you need to understand is the role of pressure gauges. These are direct-reading instruments. That means what you see is what you get. No conversions, no signal processing. Just a simple mechanical pointer indicating the pressure inside a system.
Pressure gauges typically use a Bourdon tube mechanism. When pressure increases, the tube flexes, and that movement drives a pointer on the dial. They’re widely used in industries because they’re reliable, require no power, and are easy to read. From compressors and boilers to hydraulic presses, pressure gauges are everywhere.
But here’s a key point: they are local indicators. If you want to know the pressure, you have to be physically present near the gauge. That’s both a strength and a limitation. In smaller plants or for quick spot-checks, they’re perfect. But if you’re building a smart system or monitoring from a control room, this won’t cut it.
Despite their simplicity, don’t underestimate their value. They’ve saved countless systems from overload and operators from danger. They’re the eyes of basic pressure monitoring. So, before jumping into complex electronics, master these fundamentals.
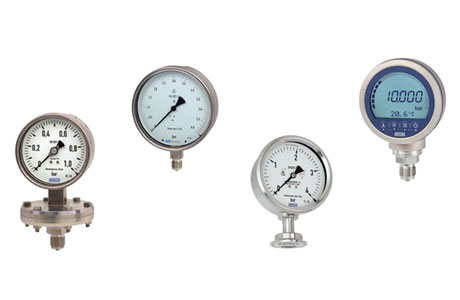
Pressure Sensors: Electronic Signal Output
Now, let’s move a level up. Once industries needed to automate and monitor systems from a distance, pressure sensors came into the picture. These clever devices convert pressure into an electrical signal. Usually, a voltage or a current signal that goes straight to a display or PLC (Programmable Logic Controller).
The key component inside most pressure sensors is a strain gauge or piezoelectric material. When pressure is applied, the resistance changes, generating a proportional electrical output. That’s the data your system reads. This makes pressure sensors perfect for real-time monitoring, alerts, and automated actions.
They’re commonly used in robotics, factory automation, and automotive applications. If you want to integrate pressure data into your control system, sensors are your go-to.
Here’s a quick tip: sensors require power. They’re active devices. They’re also sensitive to electromagnetic interference and temperature changes. So, proper shielding and installation matter a lot.
Pressure sensors give you flexibility and smart feedback. You can log data, set thresholds, and automate responses. This is the kind of smart instrumentation that drives Industry 4.0.
Pressure Transmitters: Remote Monitoring Applications
Now we’re getting into the heavyweights. Pressure transmitters are like the elder cousins of sensors. They don’t just send raw electrical signals; they convert pressure into standardized outputs like 4-20 mA or HART protocols, which can travel long distances without signal loss.
Transmitters are used in process industries where monitoring and controlling pressure remotely is critical. Think of oil refineries, chemical plants, and large-scale manufacturing lines. You can place a transmitter 200 meters away from the control room, and still get accurate readings.
Most transmitters are built tough. They can handle high temperatures, corrosive media, and explosive environments. You’ll often find smart transmitters that offer digital diagnostics, remote calibration, and zero drift features.
Compared to gauges or sensors, they’re expensive. But their accuracy, reliability, and ability to integrate into SCADA systems make them indispensable in modern plants.
Here’s something to keep in mind: Not every application needs a transmitter. Use them where the scale, criticality, or environmental conditions demand it. Otherwise, you’re just overspending.
Comparison Between Gauges, Sensors, and Transmitters
Let’s line them up and compare. This is important when you’re deciding what to use for a specific application.
Pressure Gauges are mechanical and analog. They’re great for local, visual monitoring. No wiring, no signal conditioning, but also no remote access or automation.
Pressure Sensors are compact and digital. They convert pressure to an electrical signal for integration with PLCs or HMIs. Ideal for machine feedback and automation systems.
Pressure Transmitters are robust and highly accurate. They provide long-distance signal transmission and are made for large, hazardous, or high-performance environments.
Think of it like this:
Use a gauge when someone is on-site checking manually.
Use a sensor when data needs to feed into local systems or machinery.
Use a transmitter when the data has to travel far or be used for critical system control.
Each has its place. The key is understanding the process needs, budget, and environment.
Where Each Instrument Type Is Used
Let’s look at some real-world examples so you can relate better.
In a boiler room, you’ll typically see pressure gauges right on the pipeline. The operator walks by and checks if everything’s normal.
In a CNC machine, a pressure sensor ensures air pressure is within limits. If it drops, the machine pauses and sends an alert.
In a chemical plant, a pressure transmitter monitors pressure in a storage tank 100 meters away. The signal feeds into a DCS system that logs and controls it 24/7.
Conclusion
Pressure instruments fall into three broad categories: gauges, sensors, and transmitters. Gauges provide on-site visual readings, ideal for local monitoring. Sensors convert pressure into electrical signals, best for automated control systems. Transmitters go a step further—sending pressure data remotely for continuous tracking. Each has its own role in process monitoring. Using a gauge where a transmitter is needed leads to data blind spots. Likewise, using a transmitter in a basic system adds unnecessary complexity and cost. Evaluate your application’s needs—whether manual observation or integration with PLCs/SCADA—and choose accordingly. The right instrument ensures precision, efficiency, and long-term system performance without overcomplication.