Key Takeaway
The formula for gauge pressure is:
Pg = Pabs – Patm
Where:
Pg = Gauge Pressure
Pabs = Absolute Pressure
Patm = Atmospheric Pressure (typically ~101.3 kPa at sea level)
This formula means that gauge pressure measures how much pressure exceeds the ambient atmospheric pressure. If absolute pressure is lower than atmospheric pressure, the gauge pressure becomes negative (indicating a vacuum). Most mechanical gauges like tire or industrial pressure gauges show gauge pressure, not absolute. For example, if your absolute pressure is 250 kPa and the atmospheric pressure is 100 kPa, your gauge pressure would be 150 kPa. It’s a critical concept in industrial measurements and system design.
Standard Formula: Pg = Pabs - Patm
Every new engineer stepping into the world of industrial instrumentation must understand that most pressure measuring instruments actually measure gauge pressure, not absolute pressure. This means the pressure reading you see on a dial or digital screen is already adjusted for atmospheric pressure — it shows how much above (or below) the ambient air pressure your system is operating.
Imagine working on a pipeline system or a compressed air unit. If the gauge reads zero, it doesn’t mean there’s no pressure at all — it means the pressure inside the system equals the surrounding atmospheric pressure. That’s a key insight.
And here’s another thing. This formula is essential when switching between different types of sensors or designing control systems. If you confuse absolute with gauge pressure, you might end up miscalculating and potentially damaging sensitive equipment.
So, always remember: the Pg = Pabs – Patm formula is the foundation of accurate pressure monitoring in any plant or factory setup.
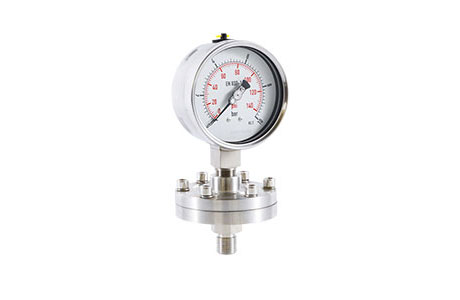
Understanding Atmospheric Pressure (Patm)
Atmospheric pressure is the air pressure around us — the force exerted by the weight of the air above us. It’s not fixed. It changes with altitude, temperature, and weather conditions.
At sea level, standard atmospheric pressure is about 101.325 kPa. But if you’re working in a hilly region or inside a vacuum-sealed environment, this value can be quite different. That’s why it’s important to always confirm the local atmospheric pressure when performing any pressure-based calculations.
For industrial engineers, knowing this variable is non-negotiable. Let’s say you’re calibrating an absolute pressure sensor — you’ll need to subtract Patm from that reading to get gauge pressure. If you assume a wrong Patm, your gauge pressure reading will be inaccurate. And that can lead to underperformance or overpressure warnings in machinery.
Also, when atmospheric pressure drops, even a sealed tank may show increased gauge pressure, simply because the external pressure has reduced — not because the internal pressure has changed. This misunderstanding can cause unnecessary alarms or shutoffs.
That’s why we always teach our junior engineers: treat Patm as a living number. Always check the real-time atmospheric conditions before relying on pressure values in sensitive operations.
Real-World Example of Gauge Pressure Calculation
Let me give you a live floor example. Picture this — you’re on a shift in a process plant. One of the vessels shows an absolute pressure of 250 kPa. The control room reads atmospheric pressure as 100 kPa. So, what’s the gauge pressure?
Apply the formula: Pg = Pabs – Patm
Pg = 250 – 100 = 150 kPa
So the system is running 150 kPa above the ambient pressure. Simple. But what if someone misread the sensor and thought 250 kPa was gauge pressure? Then they would assume the internal pressure is much higher than it really is — and that could trigger false alarms or unnecessary interventions.
Here’s another case. You’re installing a new pressure gauge on a steam line. The specs mention absolute pressure range. But your existing system is based on gauge pressure. If you don’t convert values correctly, the new gauge might always read higher than expected. You’ll end up chasing problems that don’t exist.
That’s why we stress so much on field-level accuracy. Calculations may be basic, but misreading or misapplying them can cost time, money, and safety.
Always double-check which type of pressure your device is measuring. And always ask this: Is the value I see on the display gauge pressure or absolute pressure?
When to Use This Formula in Industry
Knowing when to apply Pg = Pabs – Patm can save your job — and your machines.
This formula is most relevant when you’re switching between different types of instruments. For instance, if your data logger reads absolute pressure but your SCADA system expects gauge pressure input, you’ll need to apply this formula before feeding values into the system.
It also plays a big role during system design or audits. If you’re planning a pressurized tank system, safety valves are usually set based on gauge pressure. So, while the tank might hold a higher absolute pressure, safety thresholds are designed against the pressure above atmospheric level — gauge pressure.
In the chemical and oil & gas industries, where vacuum systems or pressurized chambers are involved, this formula becomes even more critical. A vacuum system might show negative gauge pressure, but the absolute pressure is still a positive number. Without proper interpretation, someone might assume the system is in full vacuum when it’s not.
In short, apply this formula:
During instrument calibration
When logging or transferring pressure data
While designing pressure-sensitive equipment
During troubleshooting abnormal readings
This isn’t theory. This is everyday engineering.
Tools for Accurate Gauge Pressure Measurement
To measure gauge pressure accurately, industries use mechanical Bourdon tube gauges, digital pressure transmitters, and manometers. Each has its place.
Bourdon tube gauges are most common. They’re easy to use and cheap. But they need regular calibration. Over time, vibration and environmental conditions affect their accuracy.
Digital transmitters are more advanced. They can offer both gauge and absolute readings. You can even configure them for differential pressure. These are used in critical systems like pharmaceutical manufacturing or chemical dosing.
Manometers are simple but effective. They work on fluid displacement and are often used in HVAC systems or calibration labs. Not ideal for rugged industrial environments but great for accuracy.
One tool that is gaining popularity is the pressure data logger. These can record pressure values over time and help identify anomalies or peak pressures during specific operations.
Always remember: regular calibration and environmental compensation (like temperature or altitude) are just as important as the reading itself. The best engineers are those who don’t blindly trust the gauge but ask, “Is this value truly accurate for this application?”
To wrap up, gauge pressure might seem like a basic topic, but it’s deeply rooted in every industrial operation. Mastering it early will make you a more reliable and trusted engineer on the field.
Conclusion
The formula for gauge pressure is simple: Pg = Pabs – Patm. But overlooking this basic equation leads to wrong readings, especially in high-accuracy systems. Miscalculating gauge pressure can trigger incorrect alarms or mislead automation systems, risking equipment failure. It’s important to measure and adjust for atmospheric pressure when needed—especially in labs, aerospace, or high-altitude applications. Proper calibration tools, accurate reference pressure, and understanding when to use absolute, gauge, or differential pressure are essential. This math isn’t just theory—it’s applied safety. Operators and technicians who understand the formula can validate sensors, detect drift, and ensure the right data flows through control systems.