Key Takeaway
To calculate gauge pressure, use the formula:
Gauge Pressure = Absolute Pressure – Atmospheric Pressure
If the absolute pressure (measured from a perfect vacuum) is 250 kPa, and the local atmospheric pressure is 101.3 kPa, the gauge pressure is:
250 – 101.3 = 148.7 kPa (gauge)
Gauge pressure represents how much pressure is above the surrounding atmospheric pressure. It’s commonly used in mechanical gauges like tire or water pressure meters. Note: If the result is negative, it indicates a vacuum condition. Always ensure the atmospheric pressure value is accurate for your location, as it varies with altitude and weather. Gauge pressure is vital in industrial settings where overpressure can lead to system failure or safety hazards.
Understanding the Basic Formula: Pg = Pabs - Patm
Gauge pressure (Pg) is the pressure measured relative to atmospheric pressure (Patm). In simple words, it tells you how much pressure is present in a system above or below the surrounding air pressure. The basic formula used across industries is:
Pg = Pabs – Patm
Here:
Pg is the gauge pressure.
Pabs is the absolute pressure (total pressure exerted, including atmospheric).
Patm is the current atmospheric pressure, which is generally around 1.013 bar or 101.325 kPa at sea level.In most industrial applications, instruments like pumps, compressors, and pressure vessels are rated based on gauge pressure—not absolute. This allows engineers to understand the pressure stress the equipment is actually facing beyond the surrounding air pressure.
For example, if your absolute pressure reads 5 bar and the atmospheric pressure is 1 bar, your gauge pressure is 4 bar. Simple, right?
This formula is not just academic—it’s used in day-to-day troubleshooting, process control, and safety analysis. Without knowing it, many young engineers misinterpret readings, which can lead to incorrect assumptions about system performance.
Always remember: Gauge pressure is what your pressure gauge typically shows. It zeros at atmospheric pressure, not vacuum. And that difference is what you need to manage, monitor, and master in real-world environments.
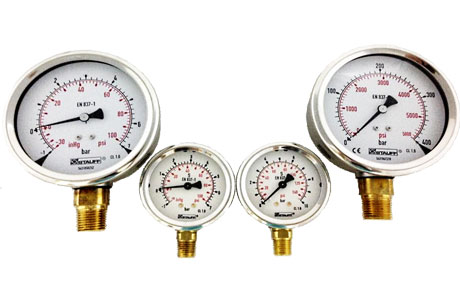
Tools and Instruments for Measurement
In the field, gauge pressure is not calculated manually in most cases. Instead, we rely on pressure gauges or digital sensors that automatically give you the Pg value directly. But here’s the catch—you need the right tool for the right job.
There are three common types of instruments used:
Analog Bourdon Tube Pressure Gauges
Digital Pressure Gauges
Pressure Transmitters and Sensors
The analog type is still widely used in many plants because of its durability, cost-effectiveness, and simplicity. These are typically dial-type indicators and are easy to install on pipelines, tanks, and pumps.
Digital gauges, on the other hand, offer precise readings, often with multiple unit options (bar, psi, kPa), and are ideal for high-accuracy or critical processes. Most of them come with built-in temperature compensation, which is a huge advantage.
Then we have smart sensors or transmitters, often used in PLC/SCADA-based setups, that not only measure pressure but also communicate the values to control systems in real-time. These are vital in automated industries where human error must be minimized.
No matter which tool you use, make sure it is:
Calibrated regularly
Installed properly at the right process point
Rated for your application’s pressure range
Without proper tools, even the best calculations become useless. Trust your instruments—but verify them periodically.
Real-Life Example Calculation
Let’s simplify things with a real-life example.
Imagine you’re working on a compressor system in a factory. The sensor shows an absolute pressure (Pabs) of 6.5 bar. You know the current atmospheric pressure (Patm) in your location is approximately 1 bar.
Using the formula:
Pg = Pabs – Patm
Pg = 6.5 bar – 1 bar = 5.5 bar
That 5.5 bar is what the equipment is experiencing beyond ambient pressure. This is the pressure that determines whether the system is operating safely and efficiently.
Now flip the situation.
If you connect a vacuum pump and get a pressure of 0.3 bar absolute, what’s the gauge pressure?
Pg = 0.3 – 1 = -0.7 bar
That’s a negative gauge pressure, which indicates vacuum. In such scenarios, negative values are expected and normal.
Why is this important?
Because understanding whether your system is under positive pressure or vacuum conditions directly impacts the design of your equipment—especially the material, seals, and pressure ratings.
This kind of clarity can help you avoid overdesigning systems or, worse, underestimating risks. Use this simple calculation daily, and you’ll start seeing pressure data as actionable insight, not just numbers.
Common Pitfalls in Manual Gauge Pressure Calculation
Now here’s the part most engineers ignore—and pay the price later.
Even though the formula is straightforward, manual calculations can go wrong when:
You use outdated atmospheric pressure values.
You misread the pressure gauge scale (e.g., bar vs. psi).
You forget to convert units correctly.
You assume standard sea-level pressure everywhere.
Let’s break that down.
A common mistake is assuming atmospheric pressure is always 1 bar. But that’s true only at sea level and under normal weather. If you’re working at a higher altitude or in a weather system with low pressure, your Patm might drop to 0.9 bar or lower.
That 0.1 difference can skew your calculations, especially in precision processes like pharma, gas systems, or aerospace.
Another common error? Not identifying whether your sensor gives absolute or gauge readings. Some transmitters provide absolute pressure, and if you mistakenly treat that as gauge Pressure—you’ll miscalculate the real force acting on your system.
Always label and verify your sensors. Don’t just look at the number. Understand what it represents.
And finally, don’t ignore unit conversions. Engineers working in international environments must switch between bar, psi, and kPa regularly. One wrong unit? Entire process setup can fail.
Your job isn’t just to know the formula. It’s to know where errors creep in and how to prevent them.
Impact of Temperature and Elevation
Let me tell you something every field engineer must never forget—pressure never acts alone.
Temperature and elevation silently affect your readings more than you think.
Let’s start with elevation. At higher altitudes, atmospheric pressure drops. For example, while sea level pressure is around 1.013 bar, in a city like Shimla or Denver, it might be 0.8 bar. So the same absolute pressure sensor will show a different gauge pressure in different cities—even if the system stays the same!
This difference can impact everything from pump efficiency to flow control.
Now let’s look at temperature. Gases expand when heated and contract when cooled. This affects both the system pressure and the accuracy of the gauge. In some industries—like food processing or steam systems—temperature fluctuations are rapid and frequent. If your gauge is not temperature compensated, you might see false pressure spikes or dips.
Some modern pressure sensors now include built-in temperature sensors, which correct the reading on the fly. If you’re working in high-precision zones, insist on these.
Bottom line?
Never isolate pressure from its environment. Always account for where and how you’re measuring. That’s how experienced engineers ensure reliability, not just accuracy.
Conclusion
Calculating gauge pressure accurately is essential for safe and efficient operations. The formula is straightforward—Gauge Pressure = Absolute Pressure – Atmospheric Pressure—but must be applied correctly. Without understanding this, technicians may misread conditions, leading to system overpressure, underperformance, or even mechanical failure. In areas of varying altitude or barometric conditions, atmospheric pressure shifts must be considered. Always ensure your pressure gauge is calibrated correctly and zeroed before use. Accurate readings also depend on proper installation and environmental compensation. When the basics are overlooked, even the best instruments can mislead. Knowing the theory behind the reading builds confidence, reduces error, and supports better decisions in process control and maintenance.