Key Takeaway
To read a mechanical pressure gauge:
Identify the units (psi, bar, kPa, etc.) on the dial.
Look at the needle position and align it with the nearest marking.
Estimate the value between marks if needed (e.g., if the needle is halfway between 40 and 50 psi, it’s 45 psi).
Check if the gauge is zeroed when not connected to pressure—if not, there may be a zero error.
In digital gauges, the pressure is displayed directly. Always ensure the gauge is properly installed and facing front for accurate readings. Also, verify that the range of the gauge suits the pressure you are measuring, to avoid overrange damage.
Analog Dial Reading Techniques
Reading analog gauges correctly is a basic yet often mishandled task. One of the most common mistakes is parallax error — when you read the gauge at an angle, not straight on. Always align your eye with the needle to get an accurate value.
Make sure the units are correct — PSI, bar, or kg/cm². Look for dual-scale gauges in international facilities. Check if the needle movement is smooth; a stuck or bouncing needle could mean internal damage. And don’t forget the glass — if it’s dirty or foggy, you’re working blind.
In short: clean view, proper eye alignment, unit awareness, and needle behavior are your checklist for every reading.
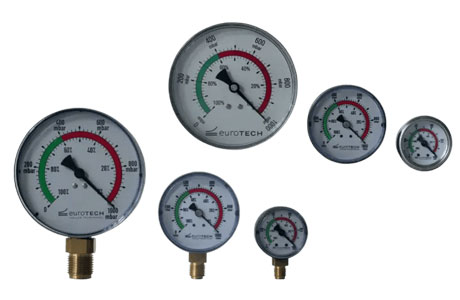
How to Read a Digital Pressure Display
Digital pressure displays offer precise readings, often down to one or two decimal places. Unlike analog gauges, they eliminate parallax error and are easier to read in low-light or fast-paced environments.
To read one correctly:
First, confirm the unit of measurement — PSI, bar, Pa, or MPa.
Then check if the display is absolute or gauge pressure.
Look for alarm indicators or error codes that may appear alongside the number.
Many digital displays have zeroing functions, peak hold, and backlighting. They’re also more responsive than mechanical systems, showing rapid pressure changes in real time.
However, they rely on sensors, batteries, or wired power. So always ensure the device is calibrated and functioning properly before trusting the numbers. In high-risk environments, it’s common to use both a digital and analog gauge together as redundancy.
Recognizing Zero Offset and Misalignments
Zero offset happens when the gauge pointer doesn’t rest at zero even when no pressure is applied. It’s often caused by:
Mechanical stress
Overpressure
Thermal expansion
Vibration or mishandling
To check, disconnect the gauge, vent pressure, and observe the needle. If it sits off zero, that’s your offset.Misalignment, like bent needles or skewed dials, also distorts readings. This can occur after physical impact or manufacturing defects.
Regularly inspect and recalibrate gauges to avoid propagating errors. Even a small zero shift leads to incorrect readings, especially in low-pressure applications. Fixing these errors early improves trust and precision in your system.
Understanding Color Bands and Red Zones
Analog pressure gauges often feature color-coded segments to visually indicate safe, caution, or danger zones. These are especially helpful in environments where operators must react quickly.
Green Zone: Normal operating range
Yellow Zone: Caution – near upper/lower limits
Red Zone: Danger – overpressure or vacuum
These zones can be painted on the dial or marked with adhesive stickers. In high-risk environments like steam boilers or hydraulic presses, red zones help prevent accidents by alerting technicians instantly.
Operators must be trained to recognize and respond to color indicators. Ignoring a red zone reading could result in system rupture, energy loss, or injury.
Safety Precautions While Reading
When working with pressure gauges, safety should always come first. Even though they seem simple, gauges operate under pressure and can pose risks if mishandled. Always begin by checking if the gauge is rated for the system pressure. Never exceed the gauge’s maximum pressure limit — doing so can cause failure or bursting, especially in older or poorly maintained units.
Ensure the gauge is installed in a location where it’s easy to read without straining or exposing the operator to hazardous environments. Avoid placing it near hot surfaces, moving parts, or areas with strong vibration unless it is specially rated for such conditions.
Before reading, confirm that the system is stable and not in a state of transition like startup or shutdown, which may cause fluctuations. Use personal protective equipment (PPE) where required — especially in chemical, steam, or high-pressure systems. For glass gauges, use safety glasses as a precaution against potential shattering.
Lastly, never attempt to tap or strike a gauge to “unstick” a needle — it can misalign or damage the internal mechanism. If the reading seems wrong, replace or calibrate the gauge instead of guessing. These simple habits go a long way in preventing accidents and maintaining equipment accuracy.
Conclusion
Reading a pressure gauge may seem simple, but small errors can lead to major problems. Parallax errors, wrong unit interpretation, or misreading needle positions can result in incorrect assumptions about system status. Always ensure your eye is level with the dial, check the unit (PSI, bar, etc.), and make sure the needle isn’t stuck or offset. Digital gauges may seem foolproof, but they can also malfunction if batteries are low or sensors drift. Operators should be trained to spot anomalies like fluctuating readings or zero errors. Correct reading is the first line of defense in preventing equipment damage, leaks, or dangerous overpressure situations. A few seconds of attention could save thousands in repairs—or lives.