Key Takeaway
Zero error occurs when a pressure gauge does not read zero when it should—i.e., when no pressure is applied. This typically happens in mechanical gauges due to fatigue, shock, temperature changes, or aging of internal components. A positive zero error shows a higher reading than actual, while a negative zero error shows a lower value. It can lead to inaccurate readings and may compromise system safety or performance. To correct zero error, the gauge must be recalibrated or reset. In sensitive applications, regular inspection and calibration schedules are critical to ensure zero error is minimized and the gauge remains accurate.
Definition and Common Causes of Zero Error
Zero error happens when a gauge does not return to zero when the system is depressurized. It’s dangerous because it builds a false confidence in your readings. For example, a zero error of +5 PSI means your actual reading is always off by 5 PSI.
Common causes include mechanical shock, aging of the Bourdon tube, internal residue, or poor manufacturing. Even overpressure events can cause permanent deformation of internal components.
To check zero error, disconnect the gauge and observe the needle position. If it doesn’t rest exactly at zero, recalibration or replacement is needed. This simple step prevents major process inaccuracies.
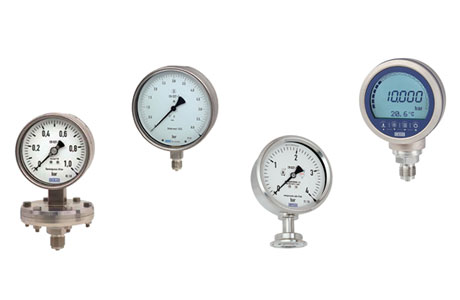
How to Identify Zero Error in Analog Gauges
Zero error is when an analog pressure gauge doesn’t return to zero when there’s no pressure in the system. It’s one of the simplest but most important errors to detect.
To check:
Isolate or remove the gauge from the system.
Ensure it’s fully vented to the atmosphere.
Check if the pointer rests at zero. If not, the gauge has a zero error.
A small deviation (1–2% FS) might be acceptable in low-critical systems. But in high-precision or safety-sensitive environments, it’s a problem.
Common causes include mechanical stress, overpressure, or long-term wear in the Bourdon tube. Always check the zero before and after use, especially on portable test gauges. If error persists, recalibrate or replace the unit.
Adjusting the Needle to True Zero
If a gauge shows zero error, you can sometimes manually reset the pointer. Here’s how:
Remove the gauge face or unscrew the bezel.
Carefully rotate the pointer using a reset screw or by hand (if accessible).
Align it exactly with the zero mark.
Reassemble and recheck after venting pressure.
Only attempt this if the gauge mechanism is undamaged. If the internal tube is bent or worn out, manual zeroing won’t fix the root issue.
Use this method for minor offsets, especially in portable or test gauges. For critical systems, rely on proper calibration tools or replace the gauge entirely.
Effects of Zero Error on Process Control
Zero error skews every reading a pressure gauge provides. Even a small offset (e.g., 0.3 bar) causes:
Misjudged operating pressures
Incorrect controller responses
False alarms or missed fault detection
For example, if a pump is expected to start at 4 bar but the gauge reads 3.7 at zero, the controller may trigger too late. This affects flow rate, quality, and safety.
In automated systems, zero error throws off PID control loops — leading to overshoot or unstable operation.
Always verify zero during startup checks and after maintenance. A gauge with visible zero error should be recalibrated or replaced immediately.
Preventing Zero Error Through Regular Maintenance
Zero error occurs when a pressure gauge shows a reading even when no pressure is applied. This can mislead operators and lead to faulty decisions. The best defense against zero error is routine maintenance and calibration.
Regularly inspect the gauge for visible signs of damage, corrosion, or wear. Over time, mechanical components like the Bourdon tube may deform, especially under continuous stress or vibration. This deformation shifts the needle’s resting position, creating a false zero.
To prevent this, schedule periodic zero checks. Isolate the gauge, relieve system pressure, and see if the needle returns to zero. If not, calibration or replacement is required. For liquid-filled gauges, also check for air bubbles or fluid loss, as this can affect the damping mechanism and accuracy.
Store spare gauges in a clean, vibration-free environment and rotate them periodically into use. For critical applications, consider using digital gauges with auto-zeroing features. In high-vibration zones, use gauges with dampeners or silicone-filled cases to reduce wear.
Consistent care not only extends gauge life but also maintains the accuracy and safety of your entire system — preventing small measurement errors from turning into costly operational problems.
Conclusion
Zero error occurs when the pressure gauge needle does not return to zero when there’s no pressure in the system. This small issue can significantly distort readings and lead to poor decisions. A zero error of just 2 PSI could cause operators to believe a tank is properly pressurized when it’s actually underfilled—or overpressurized. Regular checks, especially before high-stakes operations, are essential. Many gauges include a zero adjustment screw or require manual recalibration. Zero error can be caused by mechanical wear, pressure shocks, or improper storage. Ignoring it leads to cumulative inaccuracies across your system. Spotting and correcting zero error early maintains trust in your instrumentation and ensures operational safety.