Key Takeaway
Pressure gauge error is calculated by comparing the measured pressure value to the true or standard pressure value. The formula is:
Error (%) = [(Measured Value – True Value) / Full Scale] × 100
For example, if a gauge reads 105 psi, the true value is 100 psi, and the full-scale range is 200 psi, then:
Error = (105 – 100) / 200 × 100 = 2.5%
This helps determine how accurate the gauge is. Regular calibration ensures the gauge remains within acceptable error limits (typically ±1% to ±2%). Gauges with high error should be adjusted or replaced, especially in applications where precision is critical for safety or performance.
Error Formula: (True Value - Measured Value) / True Value × 100
This formula is your foundation for evaluating gauge accuracy:
Error % = (True Value – Measured Value) / True Value × 100
If your system pressure is 100 PSI but the gauge reads 92 PSI, your error is 8%. This impacts system efficiency, quality control, and even safety — especially in regulated environments like pharmaceuticals or chemical processing.
Compare against a master gauge or calibrated device to identify the true value. If the error crosses acceptable thresholds (often ±1% to ±2.5% depending on the application), you should calibrate or replace the instrument.
Engineers should regularly record and review these errors to avoid systemic drift over time.
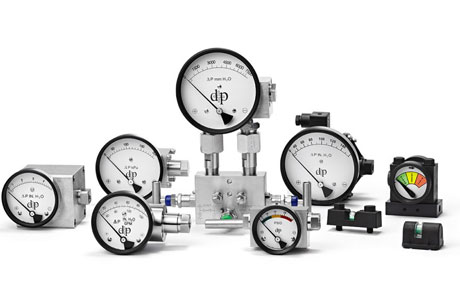
Using Calibration Standards and Master Gauges
Calibration ensures your pressure gauge provides accurate readings. And to calibrate a gauge, you need a reference standard — something more accurate than the gauge being tested.
Two common tools:
Master Gauge: A certified gauge with high accuracy (Class 0.25 or better)
Dead Weight Tester: Applies known pressure using calibrated weights — considered the gold standard
The procedure involves applying known pressures and comparing the gauge reading. Deviations are recorded and used to adjust the gauge if possible.
Calibration must follow traceable standards (like NABL or NIST) and should be done regularly — usually every 6–12 months depending on usage. Always label your gauges with the calibration date and due date.
Allowable Tolerances in Different Industries
Different industries define acceptable pressure gauge errors based on process criticality:
Pharma/Labs: ±0.25% to ±1.0% of full scale (Class 0.25–1.0)
Oil & Gas: ±1.0% to ±1.6% depending on pipeline or pump location
HVAC/Water: ±2.5% tolerance is usually sufficient
Manufacturing: ±1.6% to ±2.5% depending on system type
Tolerances ensure product quality, energy efficiency, and regulatory compliance. Don’t just install a gauge — ensure it meets the tolerance class required for your process. Too loose, and you’ll get false alarms. Too tight, and you’ll pay for unnecessary precision.
Importance of Environmental Conditions
Temperature, humidity, vibration, and even altitude affect pressure gauge performance.
High temperature softens elastic elements, reducing accuracy
Humidity can fog dials or corrode internals
Altitude alters atmospheric pressure, impacting gauge vs absolute readings
Vibration causes mechanical wear and pointer oscillation
To protect your gauges:
Use liquid-filled models in vibrating zones
Install snubbers or isolators
Mount remotely with capillary tubing in hot or corrosive areas
Choose IP-rated enclosures for outdoor use
Ignoring environmental impact leads to early failure, false readings, and expensive process errors.
Recording and Reporting Measurement Errors
Even with the best tools, measurement errors can happen — but failing to record or report them is a serious oversight. Accurate pressure readings are critical for process control, equipment safety, and compliance. Any deviation from expected values should be documented promptly and clearly.
Start by identifying whether the error is due to user handling, equipment malfunction, or environmental factors. Misreading the scale, parallax errors, or misinterpreting units are common operator issues. Meanwhile, zero drift, stuck needles, or cracked dials often signal instrument problems.
Every pressure error should be logged with the date, time, system condition, and the suspected cause. Include any corrective action taken — whether the gauge was recalibrated, replaced, or found to be functioning correctly after a system adjustment.
Use standardized error sheets or digital logs to keep records traceable and audit-friendly. In regulated industries like pharmaceuticals, energy, or food processing, this is especially important for inspections and compliance.
Additionally, train all personnel to recognize errors and report them without hesitation. A small anomaly, when flagged early, can prevent major accidents. Building a culture of measurement integrity helps improve overall reliability and operational excellence.
Conclusion
Pressure gauges come with accuracy ratings—typically 1%, 1.6%, or 2.5% of full scale. Choosing the correct accuracy class is essential for maintaining system control. In critical applications like pharmaceuticals or aviation, even a slight deviation can be unacceptable. In contrast, less demanding systems like irrigation or HVAC may tolerate lower accuracy. Poor accuracy leads to process inefficiencies, safety risks, and false diagnostics. Regular calibration ensures the gauge remains within acceptable limits. Operators must also understand the difference between accuracy, precision, and resolution. Don’t rely on assumptions—use the manufacturer’s specifications to verify suitability. Remember: the more sensitive the process, the tighter the accuracy you need. It’s not a luxury—it’s a requirement.