Key Takeaway
The fundamental law governing pressure gauges is Hooke’s Law, which states that the deformation of an elastic material is proportional to the force applied, within its elastic limit. In pressure gauges, this principle is used in Bourdon tubes, diaphragms, and bellows. As fluid pressure applies force to the elastic element, it deforms, and the movement is converted into a readable dial indication. Other laws involved include Pascal’s Law, which states that pressure applied to a confined fluid is transmitted undiminished in all directions. These principles ensure that pressure readings are consistent and accurate across various mechanical and electronic gauge types.
Boyle’s and Hooke’s Law in Gauge Design
Pressure gauge design is rooted in physics — particularly Boyle’s Law and Hooke’s Law.
Boyle’s Law explains gas behavior: if temperature stays constant, pressure × volume = constant. This helps engineers understand how gas compression impacts system pressure — essential when designing gauges for pneumatic systems.
Hooke’s Law, as we covered earlier, governs how elastic elements in the gauge respond to pressure. It ensures that when a Bourdon tube bends, the deflection corresponds proportionally to the applied pressure — until the elastic limit is reached.
In essence, Boyle helps predict system behavior, while Hooke governs how the gauge responds. These laws are the foundation for pressure sensing accuracy.
Gauge manufacturers calculate tube thickness, curvature, and material properties based on these principles. If you’re ever troubleshooting a faulty gauge, go back to these basics — is the pressure real, or is the gauge mechanically unresponsive?
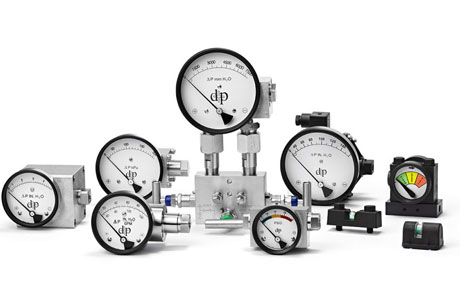
Relationship Between Force, Area, and Pressure
The core formula of pressure is:
Pressure = Force / Area
or
P = F / A
This means if you apply a force over a smaller area, pressure increases. That’s why hydraulic systems can lift heavy loads — they convert low pressure into high force using large pistons.
Understanding this relationship helps engineers design actuator systems, calculate burst pressures, and select appropriate seals and flanges. For example, if pressure is too high for a small gasket, it may blow out or deform.
Instruments like pressure sensors and transmitters rely on this concept too — they detect how much a surface deforms under applied force.
Thermodynamic Effects on Pressure Measurement
Temperature has a direct effect on pressure — especially in closed systems. According to Gay-Lussac’s Law:
Pressure ∝ Temperature
As temperature increases, so does the pressure of gases in sealed containers. If the gauge isn’t temperature-compensated, this can lead to false high readings.
Materials like Bourdon tubes also expand with temperature, which affects elasticity and deflection.
Digital sensors can compensate electronically, but mechanical gauges must be placed away from heat sources or use bimetallic compensation.
Always consider thermodynamic effects when measuring pressure in boilers, compressors, or outdoor systems exposed to sun and ambient changes.
Fluid Mechanics Behind Pressure Readings
Pressure is defined as force per unit area (P = F/A). In fluid systems:
Liquids transmit pressure equally in all directions (Pascal’s Principle)
Gases compress and expand with temperature and volume changes (Boyle’s & Charles’ Laws)
Understanding these basics explains:
Why pressure increases with depth
How flow restrictions cause pressure drop
Why turbulence or sharp bends create localized pressure peaks
This helps design more efficient systems and interpret pressure data accurately. A pressure reading is not just a number — it’s the result of how fluid behaves in motion or at rest.
Gauge Law vs General Pressure Laws
“Gauge pressure” is measured relative to atmospheric pressure — and that’s where Gauge Law comes in. It’s not a scientific law in itself but rather a convention used in engineering and industry.
In contrast, general pressure laws — such as Boyle’s Law (P1V1 = P2V2) or Pascal’s Law (pressure applied to a fluid is transmitted equally in all directions) — are foundational scientific principles.
Gauge Law simply states:
Gauge Pressure = Absolute Pressure – Atmospheric Pressure
For example, if your tire pressure reads 35 psi (gauge), it’s actually 35 psi above atmospheric pressure (~14.7 psi at sea level). The absolute pressure is 35 + 14.7 = 49.7 psi.
In contrast, vacuum gauges measure pressures below atmospheric, often expressed as negative gauge pressures.
Engineers must distinguish between gauge and absolute pressure, especially in calculations involving gas laws, flow rates, or altitude compensation. A mistake here can lead to incorrect readings, wrong equipment sizing, or system failure.
So while Gauge Law isn’t a physics rule, it’s a critical conversion in everyday industrial use — bridging practical readings with scientific theory.
Conclusion
Behind every pressure reading lies a combination of physics principles—Hooke’s Law for elastic deformation, Boyle’s Law for gas compression, and Pascal’s Law for fluid pressure transmission. These laws help engineers design gauges that are not only functional but reliable. Ignoring these fundamentals can lead to instruments that fail under pressure, behave unpredictably, or deliver inaccurate results. For example, not accounting for compressibility in gases or ignoring thermal expansion can compromise the integrity of your readings. Understanding these laws allows you to interpret readings better, design safer systems, and select suitable instruments for specific processes. In engineering, success often hinges on respecting the laws that govern physical behavior—and gauges are no exception.