Key Takeaway
Pressure gauges come in various types based on their measurement principles and applications:
Bourdon Tube Gauge – Most common, used for medium to high pressure
Diaphragm Gauge – Ideal for low pressure and corrosive media
Bellows Gauge – Suited for differential and low pressures
Capsule Gauge – Used for low-pressure gas measurement
Magnehelic Gauge – For low-pressure differential air systems
Digital Gauge – Offers electronic reading and high accuracy
Vacuum Gauge – Measures pressures below atmospheric
Differential Gauge – Measures the difference between two pressures
Each type is chosen based on the medium, pressure range, accuracy needs, and application environment.
Absolute, Gauge, and Differential Pressure Gauges
There are three types of pressure gauges, and each serves a different role:
Gauge Pressure: Most common. Measures pressure relative to atmospheric pressure.
Absolute Pressure: Includes atmospheric pressure. Used in scientific or vacuum processes.
Differential Pressure: Measures the pressure difference between two points.
You’ll see differential gauges used across filters, pumps, and flow systems. Absolute gauges appear in labs or vacuum chambers. Gauge pressure covers everything else — boilers, compressors, hydraulics.
Never mix these up. A misconfigured sensor could throw off control systems or trigger false alarms. Know which type is needed for your application before selecting or installing a gauge.
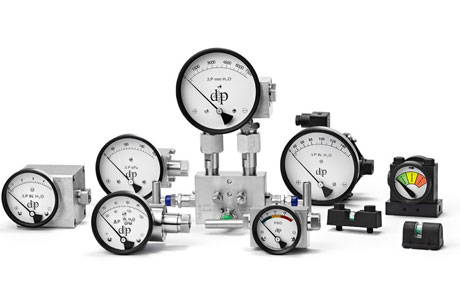
Vacuum Gauges for Negative Pressure
Vacuum gauges are used to measure pressure below atmospheric level — often referred to as negative pressure or vacuum. They’re crucial in applications like:
Vacuum packaging
Semiconductor manufacturing
Freeze drying
HVAC leak testing
Types include:
Compound Gauges: Measure both pressure and vacuum (dual scale)
Bourdon Tube Gauges: For low vacuum
Capacitive or Pirani Sensors: For deep vacuum in labs
Vacuum measurement is often in units like mmHg, Torr, or mbar. Always choose a gauge based on vacuum depth and required precision. For high vacuum, mechanical gauges aren’t enough — use electronic sensors.
Sealed and Compound Gauges
Sealed gauges are calibrated to read pressure relative to a sealed reference (usually 1 atm). They’re used where atmospheric pressure changes affect readings, like high-altitude systems.
Compound gauges measure both vacuum and pressure. Their dials show positive values (e.g., 0–6 bar) and negative (e.g., -1 to 0 bar) on a single scale.
Applications:
Sealed: Refrigeration, sealed tanks, or weather-sensitive systems
Compound: HVAC vacuum charging, pump suction monitoring
Selecting the right gauge type ensures accurate readings across fluctuating pressure ranges and environmental conditions.
Smart and Wireless Gauges
Smart gauges use Bluetooth, Wi-Fi, or cellular connectivity to send pressure readings wirelessly. They’re ideal for:
Remote or hazardous environments
Large installations with no manual access
Real-time diagnostics and alerts
Benefits:
Instant data access from anywhere
Integration with cloud dashboards
Predictive maintenance through data trends
They’re often battery-powered and built with digital sensors and microcontrollers. While more expensive than traditional gauges, smart gauges reduce labor costs, increase safety, and deliver continuous insights.
Use Cases for Each Type
Different gauge types excel in different applications:
Bourdon Tube Gauges: Used in water supply systems, hydraulics, and industrial air compressors due to robustness and affordability.
Diaphragm Gauges: Ideal for corrosive media, slurry, and sanitary processes. Used in chemical plants and food/pharma industries.
Digital Gauges: Found in labs, test benches, and smart factories. They offer precise readings, alarms, and data logging.
Capsule Gauges: Suited for very low-pressure gas applications like HVAC systems or medical ventilators.
Differential Gauges: Essential for filter monitoring, flow measurement, and pump protection across various sectors.
For example:
A Bourdon tube gauge in a steam boiler ensures safe operation under high pressure.
A digital pressure gauge in a biopharmaceutical plant logs exact values every second.
A diaphragm gauge in a fertilizer plant resists harsh chemicals that would destroy standard gauges.
Choosing the correct type ensures performance, reliability, and safety. The wrong choice may lead to failure, frequent maintenance, or even accidents.
Conclusion
There isn’t one universal type of pressure gauge for all systems. The right classification depends on what you’re measuring (gas or liquid), the environment (harsh, cleanroom, outdoor), and pressure range (vacuum, low, high). Absolute pressure gauges are used in sealed environments, differential gauges for pressure drop across filters, and compound gauges for systems needing both vacuum and positive pressure readings. Smart gauges include wireless or digital capabilities. Environmental factors like humidity, vibration, or chemical exposure also influence gauge selection. By understanding different classifications, you ensure you’re not under- or over-specifying. The right choice improves longevity, enhances accuracy, and ensures safety across your specific application.