Key Takeaway
A diaphragm pressure gauge measures pressure by using the deflection of a flexible diaphragm. The diaphragm separates the pressure medium from the movement mechanism and is ideal for low-pressure or corrosive media. When pressure is applied, the diaphragm flexes, and the movement is transmitted to a pointer for display. These gauges are highly accurate, suitable for sanitary or chemical applications, and can be constructed with materials like stainless steel, PTFE, or Hastelloy for compatibility with aggressive fluids. Diaphragm gauges are commonly used in food processing, chemical plants, and pharmaceutical industries where hygiene and corrosion resistance are crucial.
Structure and Principle of Operation
Every pressure gauge follows the same basic principle: convert pressure into displacement, and display it. The structure includes:
Pressure port
Elastic sensing element
Mechanical or magnetic transmission system
Dial and pointer
Protective casing
When pressure enters the sensing element, it causes movement — either expansion (diaphragm), deflection (Bourdon tube), or compression (capsule). That movement is amplified through a mechanism and converted into dial rotation.
Understanding this structure helps in identifying failure points: stuck needles, cracked tubes, loose gears, or condensation inside the dial window. A properly structured gauge should last years — if maintained and not overpressured.
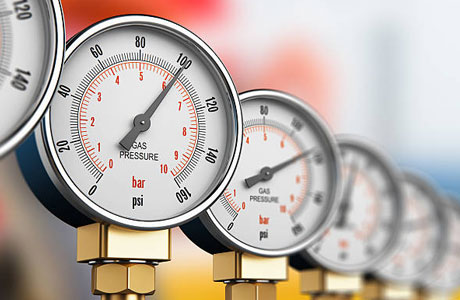
Benefits of Using Diaphragms Over Bourdon Tubes
While Bourdon tubes are great for general-purpose pressure sensing, diaphragm gauges offer key benefits in specific applications:
Better for low-pressure measurement (below 600 mbar)
Ideal for corrosive, slurry, or viscous media
Easier to isolate from the process fluid using seals
More compact in sanitary or hygienic applications
Diaphragms also provide better response in pulsating pressure conditions. They’re often used in biotech, water treatment, and food processing plants. While slightly more expensive, their longer life and process compatibility make them a preferred choice in tough environments.
Best Uses in Corrosive or Hygienic Environments
Corrosive fluids and sterile environments demand special gauge materials and designs.
Corrosive applications (acids, brine, chlorine):
Use Monel, Hastelloy, or PTFE-lined diaphragms
Avoid brass or mild steel internals
Hygienic applications (pharma, dairy, beverages):
Use 316 SS diaphragm gauges
Ensure 3A/ASME-BPE compliant fittings
Opt for flush-mounted designs for easy CIP/SIP cleaning
Gauges in these environments must resist both the media and cleaning chemicals. Always validate the material compatibility before installation to avoid failure or contamination.
Pressure Ranges and Sensitivity
Pressure ranges vary:
Vacuum: Down to -1 bar or 0 Torr
Low pressure: 0–100 mbar (e.g., cleanrooms)
Medium: 0–10 bar (e.g., pneumatics, HVAC)
High: 0–600 bar (e.g., hydraulics)
Ultra-high: >1,000 bar (e.g., injection molding)
Sensitivity is the gauge’s ability to detect small changes in pressure. For example, a low-range diaphragm gauge is more sensitive than a high-range Bourdon gauge.
Matching range and sensitivity ensures fast response and better control — especially in fast-changing processes.
Comparison with Other Mechanical Gauges
Pressure gauges are just one type of mechanical measurement device. Let’s compare them with other similar tools:
Manometers: Use liquid columns to measure pressure. They’re accurate for very low-pressure readings but impractical in dynamic or industrial settings due to size and fragility.
Pressure Switches: Trigger a system response (e.g., pump on/off) rather than provide continuous readings. They’re used for control, not monitoring.
Transducers: Convert pressure into an electrical signal — useful for automation but more expensive and fragile compared to mechanical gauges.
Compound Gauges: These measure both vacuum and positive pressure — versatile for systems with dynamic pressure ranges.
Advantages of mechanical gauges:
No power required
Simple and rugged
Easy to read
Low cost
Disadvantages:
Lower accuracy than digital
Susceptible to vibration and zero drift
No data logging
For traditional applications, mechanical gauges remain the standard. But when precision or automation is required, digital or electronic alternatives win out.
Conclusion
Diaphragm pressure gauges are ideal for low-pressure applications, corrosive media, and sanitary environments like food processing and pharmaceuticals. They use a flexible membrane to separate the measured media from the internal mechanism, ensuring no contamination and corrosion. This makes them suitable for applications involving viscous, crystallizing, or aggressive fluids. Their sensitivity allows for precise measurements in delicate systems. Diaphragm gauges also accommodate pulsation dampeners and are available in flush-mount versions for hygienic design. Because of their protective barriers and varied material options (like PTFE or stainless steel), they offer both accuracy and durability in demanding environments. When you need clean, sensitive, and chemically compatible pressure sensing, diaphragm gauges deliver.