Key Takeaway
Pressure gauges play a critical role in industrial operations. In the oil and gas industry, they monitor pipeline and wellhead pressure to avoid blowouts. In chemical processing, they ensure reactors and storage tanks maintain safe pressure levels. In power generation, they help regulate steam and boiler pressure. In pharmaceuticals and food production, sanitary gauges maintain process hygiene. They’re also used in pneumatics, hydraulics, firefighting systems, aerospace, and marine industries. Pressure gauges ensure safety, prevent costly downtime, and optimize energy consumption. Their precision and reliability are vital for process control, equipment protection, and regulatory compliance in high-stakes industrial environments.
Manufacturing and Production Line Monitoring
In production lines — whether bottling, forging, or painting — consistent pressure is critical for quality. Even slight pressure drops in pneumatic systems can cause actuator delays, product defects, or rejection of entire batches.
Pressure gauges are installed across compressors, dryers, spray nozzles, and hydraulic presses to maintain optimal conditions. Sudden changes in pressure readings often indicate leaks, valve faults, or clogged filters.
Modern setups use both analog and digital sensors with PLC integration to trigger alarms. A simple gauge may prevent downtime worth lakhs. Train your team to read them regularly — it’s part of lean manufacturing.
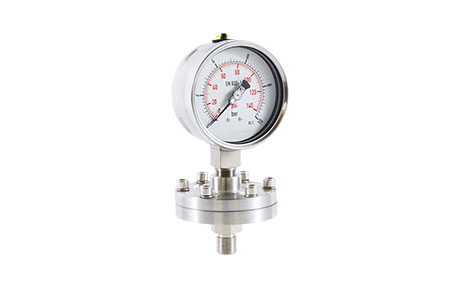
Power Plants and Utility Systems
Power plants rely heavily on accurate pressure measurement for safe and efficient operations. Whether it’s steam, cooling water, or lubrication oil — pressure monitoring is central.
In thermal power plants:
Boiler pressure must be kept within limits to prevent explosions
Turbine oil pressure ensures bearing protection
Feedwater pressure affects efficiency and flow balance
In gas or nuclear facilities, pressure sensors are integrated into safety interlocks and control systems. Any deviation from setpoints can trip alarms, reduce load, or initiate shutdowns.
Utility systems like water supply, HVAC, and compressed air also use pressure gauges to maintain system balance and avoid waste or risk.
Water Treatment and Filtration Plants
In water and effluent systems, pressure gauges are used:
Before and after filters to detect clogging
On booster pumps to verify suction/discharge pressure
On chemical dosing lines to prevent over/under-pressure
Digital differential gauges are popular for filter status. Mechanical gauges monitor pump performance in real-time. Use glycerin-filled gauges in outdoor or vibration-prone installations.
Reliable pressure monitoring reduces downtime, ensures safe chemical handling, and keeps water quality within required standards.
Pharmaceuticals and Biotech Equipment
These industries require pressure measurement for:
Bioreactor control
Sterile air systems
CIP/SIP process validation
Filtration monitoring
Requirements:
316L stainless steel body and internals
Sanitary diaphragm seals
3A or EHEDG certification
Traceable calibration with documentation
Digital transmitters are often used with PLCs for precise control. Cleanability, autoclavability, and resistance to CIP chemicals are non-negotiable features. Any contamination or inaccuracy compromises product safety and compliance.
Transport and Heavy Machinery
Transport and heavy machinery — including railways, trucks, cranes, and construction equipment — depend on pressure systems for braking, hydraulics, steering, and suspension. Gauges play a vital role in preventing mechanical failure and ensuring safety on the move.
Air brake systems in trucks and trains rely on pressure gauges to monitor reservoir pressure. If air pressure drops below a certain threshold, brakes could fail or engage improperly. Inaccurate readings here could cause accidents.
Hydraulic gauges in excavators, bulldozers, and cranes ensure lifting arms and control systems operate within safe pressure limits. Overpressure can burst hoses or damage cylinders, while underpressure may result in weak or erratic movements.
Vibration, dust, and extreme temperature variations are constant in transport and construction sites. Hence, gauges must be shock-resistant, dustproof, and often liquid-filled to dampen vibrations.
In modern vehicles and machinery, digital gauges are increasingly replacing analog ones — offering better visibility, integration with onboard diagnostics, and wireless monitoring.
Well-maintained pressure gauges in transport are not just about machine efficiency — they’re about protecting lives and avoiding downtime in high-risk environments.
Conclusion
Industrial applications depend on accurate pressure monitoring to maintain safety, productivity, and compliance. Pressure gauges serve as the backbone of this monitoring across sectors—ensuring machines run within operational limits and alerting operators to abnormalities. In power plants, they prevent turbine damage. In chemical processing, they avoid dangerous overpressure. In manufacturing, they optimize line performance. The gauge may look simple, but it connects directly to the success or failure of entire systems. Without them, there’s no visibility into what’s happening inside pipes, tanks, or machinery. A reliable gauge provides instant feedback and supports broader control strategies. When everything is on the line, trust the tool that gives you visibility: the pressure gauge.