Key Takeaway
While pressure gauges are useful, they do have limitations. Mechanical gauges can lose accuracy over time due to fatigue, vibration, or temperature changes. Exposure to corrosive or viscous media can damage internal components. They must be selected carefully for the intended pressure range—exceeding it can lead to failure or incorrect readings. Analog gauges may be hard to read in low-light or remote locations. Digital gauges need power and may be affected by electromagnetic interference. Additionally, gauges require periodic calibration to maintain accuracy. Poor installation or lack of maintenance can also result in zero error or total malfunction.
Susceptibility to Mechanical Wear and Tear
Like any mechanical device, pressure gauges degrade over time. Friction in gears, vibration from pumps, and temperature cycling slowly affect accuracy.
Common symptoms include:
Pointer sticking
Lagging needle
Zero shift
Erratic readings
To minimize wear, use liquid-filled gauges, especially in vibrating environments. They dampen internal motion and reduce fatigue. Also, mount gauges properly — never hang them unsupported on long impulse lines.
Include pressure gauge inspections in your preventive maintenance checklist. If ignored, mechanical wear leads to costly process errors or undetected safety risks.
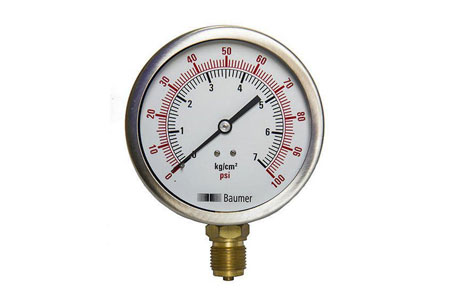
Limited Accuracy at Extreme Conditions
At extreme temperatures or pressures, mechanical pressure gauges often lose accuracy. Why?
High temperatures cause expansion of internal components, altering spring tension and deformation behavior
Extreme cold can make materials brittle or cause fluid fill to thicken
Very high pressure induces non-linear deflection or even plastic deformation in Bourdon tubes
Standard accuracy classes (1.0, 1.6, etc.) may not hold true outside 20–25°C. Use temperature-compensated gauges or electronic transmitters with RTD correction when working in harsh environments.
Also, avoid long-term use near the full-scale range — it stresses components and degrades accuracy faster.
Not Ideal for Remote Monitoring (Analog)
Analog gauges have one drawback: they can’t transmit data. This limits their use in:
Remote or hazardous zones
Unmanned facilities
Predictive maintenance systems
They require manual reading and recording. This leads to human error, delays in detecting faults, and lack of data for analysis.
For these cases, digital gauges or pressure transmitters are ideal. They offer real-time visibility, remote alerts, and integration with IoT platforms.
Use analog gauges for local monitoring, but don’t rely on them alone where remote insight is critical.
Possible Human Error in Reading Scales
Analog gauges are prone to human error due to:
Parallax effect: Reading the pointer from an angle
Misinterpreting dual scales: (e.g., bar vs PSI)
Overlooking color zones
Reading during rapid pointer movement
These errors can result in:
Incorrect process adjustments
Missed alarms
Faulty diagnostics
To reduce mistakes:
Train operators to read gauges at eye level
Use digital displays where possible
Choose larger dials or backlit designs for poor lighting
In critical applications, don’t rely solely on manual reading — pair with alarms or digital logging for verification.
Challenges in Corrosive or High-Vibration Areas
Corrosive media and high vibration present serious challenges for pressure gauge performance and lifespan.
In corrosive environments — such as chemical plants, refineries, or marine applications — standard brass or mild steel gauges quickly degrade. The sensing element and internals may get eaten away, leading to false readings or total failure. The solution? Use 316 stainless steel or Teflon-lined diaphragm seals for chemical resistance.
In high-vibration zones — like engines, compressors, or factory floors — needle flutter and fatigue damage are common. Gauges may misread, reset to zero incorrectly, or break from wear. Solutions include:
Liquid-filled gauges (typically glycerin or silicone) that dampen internal movement
Snubbers or pulsation dampeners on the inlet
Remote mounting with capillaries to isolate the gauge from vibration
Also consider reinforced mounting brackets and flexible connectors. Frequent recalibration and visual inspection are a must.
If not addressed, these harsh conditions will dramatically shorten the gauge’s useful life — sometimes within weeks. Select the right material and mounting configuration upfront to prevent downtime and safety risks.
Conclusion
No tool is perfect, and pressure gauges have their limitations. Mechanical wear, vibration, extreme temperatures, corrosive environments, and human error in reading analog dials can all compromise performance. That’s why it’s important to recognize their boundaries and implement preventive measures like isolation valves, snubbers, or remote sensors when needed. Understanding limitations also helps with realistic expectations—analog gauges won’t provide cloud-based insights, and digital ones may fail without power. Select based on application needs, not just convenience. Proper housing, mounting, and calibration are just as important as the gauge itself. When you respect what a gauge can and can’t do, you deploy it smarter, extend its life, and get better results.