Key Takeaway
Calibrating a pressure gauge involves comparing its readings to a standard reference pressure source and making adjustments as needed. First, isolate the gauge and connect it to a calibration device like a deadweight tester or pressure calibrator. Apply known pressure values in steps, and record the gauge’s reading at each level. If the readings deviate beyond acceptable limits, adjust the pointer or calibration screw (if available). After adjustments, recheck the entire range. Document the calibration results and tag the gauge with the calibration date. Calibration ensures accuracy and compliance, especially in critical applications like pharmaceutical manufacturing or gas pipelines.
Tools Required for Calibration (Dead Weight Tester, Master Gauge)
To calibrate a pressure gauge, you need reference tools more accurate than the gauge itself. The two most commonly used are:
Dead Weight Tester: This applies known pressure using calibrated weights and a piston. It’s the gold standard for accuracy.
Master Gauge: A certified high-accuracy gauge used for comparison.
During calibration, apply pressure incrementally and compare the reading. Any deviation outside allowed error must be adjusted or noted. Use T-connectors to measure both test and reference instruments in the same setup.
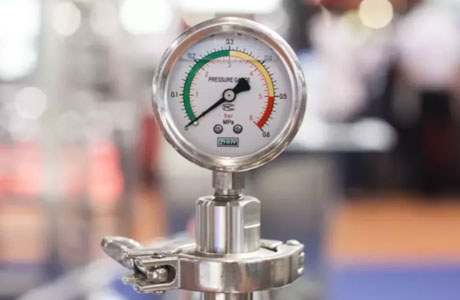
Calibration Procedure Step-by-Step
Calibrating a pressure gauge ensures it displays true values. Here’s a simplified step-by-step:
Prepare a master gauge or dead weight tester as your reference.
Isolate the gauge from the system.
Zero the test system to confirm no trapped pressure.
Apply known pressure in stages (e.g., 0%, 25%, 50%, 75%, 100%).
Record the readings and deviations at each stage.
If deviations are outside limits, use the adjustment screw or note correction factors.
Re-test in descending order to detect hysteresis.
Label the gauge with calibration date, due date, and technician info.
Calibration is not optional in regulated industries — it’s proof of accuracy and reliability.
Tolerance Limits and Pass/Fail Criteria
Each application has a tolerance range — a window where pressure is acceptable. Anything outside is a fail.
Examples:
Pharma: ±0.5% FS tolerance
HVAC: ±5% FS may be acceptable
Hydraulic systems: ±2% FS for safety
Use pressure gauges with accuracy that supports your tolerance band. Don’t use Class 2.5 gauges where ±1% accuracy is needed.
In inspections, compare readings to certified test gauges. If deviation exceeds allowed limits, the gauge fails and must be adjusted or replaced.
Recording Calibration Data
Calibration ensures traceable, accurate pressure readings. Documentation should include:
Calibration date
Gauge serial number
Reference standard used
Readings at various pressure points
Tolerance and pass/fail status
Technician signature
For regulated industries (pharma, aerospace, medical), storing this data is mandatory for audits and traceability. Use calibration stickers on the gauge body, and maintain digital or paper logs for QA/QC records.
Regularly scheduled calibration backed by recorded data builds confidence in your instrumentation system.
When and How Often to Calibrate
Calibration frequency depends on how critical the system is, how often it’s used, and how extreme the conditions are.
Calibrate more often when:
The system is safety-critical (boilers, medical, etc.)
Pressure fluctuates frequently
The environment is corrosive or vibrational
You notice zero drift or erratic readings
Typical calibration intervals:
High-precision or safety systems: every 3–6 months
General-purpose industrial: once a year
Low-use backup systems: every 2 years
The calibration process includes:
Isolate the gauge from the system.
Connect it to a calibrated pressure source.
Compare actual pressure vs displayed pressure.
Adjust or record deviation.
Label the gauge with calibration date and next due date.
Many companies set up internal calibration labs or outsource to accredited third parties (ISO/IEC 17025 certified).
Consistent calibration ensures that pressure data remains trustworthy — the cornerstone of reliable decision-making.
Conclusion
Calibration ensures your pressure gauges remain accurate, consistent, and compliant with regulatory standards. Over time, mechanical fatigue, temperature changes, and frequent use can cause gauges to drift. Without calibration, even high-quality gauges become unreliable. Calibrating against a known standard (master gauge or dead weight tester) validates your readings and catches errors early. For industries like pharma, aerospace, and oil & gas, traceable calibration is a legal requirement. It also builds internal trust—operators and engineers can confidently rely on data. A well-maintained calibration log extends instrument life, improves safety, and optimizes performance. Don’t just install and forget—schedule regular calibrations to keep your gauges trustworthy and accurate.