Key Takeaway
The frequency of pressure gauge recalibration depends on the application, usage conditions, and industry standards. In critical or high-precision environments (like pharmaceuticals, aviation, or chemical plants), gauges may be calibrated every 3–6 months. In general industrial settings, an annual calibration is common. Factors like vibration, extreme temperatures, or frequent pressure cycling may warrant more frequent checks. If a gauge is exposed to harsh environments or shows signs of inaccuracy (zero error, sticking needle), recalibration should be done immediately. Following a documented calibration schedule ensures reliable readings, process safety, and compliance with ISO or regulatory quality standards.
Recommended Recalibration Intervals by Industry
How often should you recalibrate a pressure gauge? The answer depends on:
Industry standards
Criticality of the application
Operating conditions
Typical intervals:
Every 6 months – for pharmaceutical, aerospace, or lab environments
Annually – for general manufacturing
Quarterly – for high-vibration or corrosive systems
Some industries follow ISO/IEC 17025 or API standards. Also, maintain a calibration logbook or software — track the history, service date, and next due date.
If a gauge is critical to quality or safety, treat recalibration as a must — not an optional task.
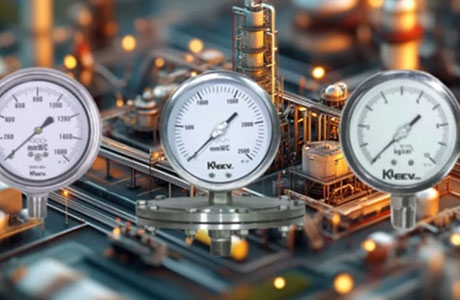
Factors That Influence Calibration Frequency
How often should you calibrate a pressure gauge? It depends on several factors:
Application criticality: Safety-related systems need more frequent checks
Operating conditions: High vibration, temperature, or pressure cycling accelerates drift
Regulatory requirements: Pharma, aerospace, and energy sectors may demand quarterly or monthly calibration
Manufacturer recommendation: Often annually, unless used heavily
Other factors include gauge type (digital vs mechanical), age, and historical stability. A good rule of thumb: calibrate at least once a year, and increase frequency if the gauge shows signs of drift, damage, or frequent zero error.
Signs That a Gauge Needs Immediate Recalibration
You should recalibrate a gauge if:
The pointer doesn’t rest at zero
Readings change sluggishly
The needle jumps or oscillates
You suspect a pressure spike event
There’s visible fog, rust, or damage
In regulated industries, recalibration is based on schedule — not just symptoms. However, these signs demand immediate attention even between cycles.
Tag faulty gauges, isolate them from the system, and send for certified recalibration or replace them. A faulty gauge leads to false decisions — and costly outcomes.
Best Practices for Scheduling Calibration
Calibration frequency depends on:
Process criticality
Manufacturer recommendations
History of drift or failure
Regulatory standards
General guidelines:
Every 6–12 months for standard industrial gauges
Every 3–6 months for high-accuracy or critical process gauges
After any suspected overpressure event
Best practices:
Use calibrated master gauges or dead-weight testers
Keep calibration certificates traceable
Log changes and compare with past trends
Replace rather than recalibrate if the gauge is damaged or too far out of spec
Consistent scheduling improves accuracy, compliance, and safety.
Role of Environment and Usage Cycles
The environment and usage frequency heavily influence a gauge’s lifespan and performance.
In clean, climate-controlled settings, a gauge might last 5–10 years with minimal calibration. But in hot, humid, dusty, or vibrating environments, even a rugged gauge can fail in under a year.
Environmental factors to monitor:
Temperature extremes
Moisture/humidity
Corrosive chemicals
Saltwater or marine conditions
Vibration and shock
Usage cycles — how often the system pressurizes and depressurizes — also matter. Frequent cycles wear out Bourdon tubes or diaphragms faster.
Best practices:
Choose the right gauge rating for the environment.
Use liquid-filled or remote-mount gauges where needed.
Set up inspection and replacement schedules based on actual usage.
Don’t just buy and forget. Understand where and how the gauge operates, and maintain accordingly.
Conclusion
Over time, all mechanical and digital pressure gauges are subject to drift due to vibration, environmental conditions, mechanical fatigue, or overpressure events. Regular recalibration—typically every 6 to 12 months—helps detect these issues early and keeps readings within tolerance. In industries like food processing, pharmaceuticals, and energy, recalibration is a regulatory and safety requirement. Scheduled recalibration reduces emergency downtime, ensures product quality, and maintains customer trust. Skipping it may lead to process deviation, rejected output, or equipment damage. With preventive recalibration, small issues don’t escalate into major failures. Whether done in-house or outsourced, building recalibration into your maintenance routine ensures long-term reliability and consistent measurement performance.