Key Takeaway
The accuracy of a pressure gauge is usually expressed as a percentage of the full-scale range. Typical accuracy classes include:
±0.1% to ±0.25% for precision digital gauges
±0.5% to ±1% for industrial-grade mechanical gauges
±2% to ±5% for general-purpose or utility gauges
Higher accuracy is required in applications like calibration labs, while lower accuracy may be acceptable for simple pressure checks. It’s important to select a gauge whose accuracy class meets your application’s requirements. A misjudged accuracy class can lead to process inefficiency, safety risks, or product quality issues.
Understanding Accuracy Classes (e.g., 1.0, 1.6, 2.5)
Accuracy class tells you how precise a pressure gauge is. The number represents the maximum error as a percentage of the full-scale value.
For example:
Class 1.0 = ±1% of full scale
Class 1.6 = ±1.6% (common in general-purpose gauges)
Class 2.5 = ±2.5% (used where precision isn’t critical)
So if you have a Class 1.6 gauge with a 100 bar range, it can show ±1.6 bar error. For high-precision systems, use Class 1.0 or better.
Never assume a gauge is accurate — check its class and ensure it fits your process tolerance.
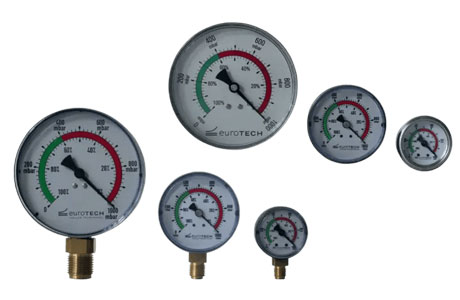
Accuracy vs Precision: What’s the Difference?
Accuracy is how close your measurement is to the true value. Precision is how consistently your gauge gives the same reading under the same conditions.
Example:
A gauge that always shows 98 PSI when the actual pressure is 100 PSI is precise but not accurate.
A gauge that sometimes shows 98, 102, and 95 PSI is neither accurate nor precise.
A well-calibrated gauge that always reads 100 PSI under 100 PSI is both.
In industrial applications, you need both. Precision ensures repeatability, and accuracy ensures correctness. Always check both when selecting and calibrating instruments.
Mechanical vs Digital Gauge Accuracy
Accuracy differs greatly between mechanical and digital pressure gauges.
Mechanical gauges (Class 1.0 to 2.5) typically offer ±1% to ±2.5% full-scale accuracy. They are affected by wear, parallax error, and environmental conditions.
Digital gauges can reach ±0.1% or better. They’re less prone to drift, easier to calibrate, and offer consistent readings regardless of operator angle.
For critical operations (pharma, aerospace, calibration labs), digital is preferred. For general monitoring or harsh environments, mechanical gauges may be more practical — especially if redundancy is built in.
Match accuracy to your process needs, not just cost or preference.
Impact of Range and Scale on Accuracy
The pressure range and scale layout directly affect gauge accuracy. A wide-range gauge may offer less resolution at lower pressures, while a narrow-range gauge provides better readability but risks overpressure damage.
Example:
A 0–100 bar gauge may only mark 5 bar divisions.
A 0–10 bar gauge will mark 0.2–0.5 bar divisions.
Best practices:
Choose a range where your normal pressure sits in the middle 30–70% of the scale.
Never operate near the full scale regularly.
Use dampers or snubbers if preesure surges are expected.
The right scale ensures better decision-making and prevents misreading in fast-paced environments.
Industry Requirements for Pressure Accuracy
Different industries demand different levels of pressure accuracy. These standards ensure safety, product quality, and compliance.
Pharmaceuticals & Biotech
Require ±0.25% or better accuracy
Must meet FDA, GMP, or ISO 14644
Food & Beverage
Sanitary gauges, CIP-compatible
Accuracy typically ±0.5%–1%
Oil & Gas
ATEX/IECEx-rated, NACE compliance
Accuracy needs vary from ±0.5% to ±1%
Aerospace
Ultra-high precision (±0.1%)
Fully traceable calibration
HVAC & Water Systems
Moderate accuracy (±1%–2%) acceptable
Reliability more important than precision
Selecting a gauge without meeting industry standards can lead to rejection during audits or worse — safety incidents.
Always match gauge specs with the compliance framework your industry follows.
Conclusion
Not every application requires a 0.1% accuracy gauge. For general HVAC or water systems, a 2.5% accuracy may be sufficient. But for pharmaceutical, lab, or high-pressure equipment, tighter tolerances are essential. Choosing a gauge with the correct accuracy class (like 1.0%, 1.6%, or 0.5%) ensures your readings are both reliable and cost-effective. Over-specifying increases cost unnecessarily, while under-specifying introduces risk. Match your gauge accuracy with operational range—targeting 30–70% of the full-scale range for the best precision. Accurate gauges minimize process waste, improve safety, and support compliance. Understanding application demands helps you avoid extremes—delivering exactly the accuracy required for your system without compromise.