Key Takeaway
A pressure switch is used in many machines and systems where pressure needs to be controlled automatically. You can find it in water pump systems, where it turns the pump ON when pressure drops and OFF when pressure rises. It is also commonly used in air compressors to stop the motor when the tank is full of air. In HVAC systems, it helps monitor refrigerant or air pressure to keep heating and cooling safe. Pressure switches are also important in industrial machines, where they protect equipment from operating under dangerous pressure levels. In oil and gas, they are used for pipeline monitoring. Even automobiles use pressure switches to check things like brake pressure or engine oil levels. Because pressure switches work automatically, they help reduce manual monitoring and improve safety. Wherever there’s a need to start or stop something based on pressure — a pressure switch is likely there.
Role in Water Pumps and Booster Systems
Pressure switches are essential in water pump and booster systems. They monitor line pressure and automatically turn pumps ON when pressure drops below a certain point (cut-in), and OFF when it rises above another (cut-out). This prevents pumps from running unnecessarily and helps maintain consistent water flow in residential, commercial, and irrigation setups. Properly adjusted switches prevent short cycling, extend pump life, and save energy. In booster systems, pressure switches ensure backup pumps activate only when needed—maintaining flow during peak demand or system drops. Without pressure switches, these systems would require constant manual supervision. Their ability to automate pump control makes them vital for water system reliability and efficiency.
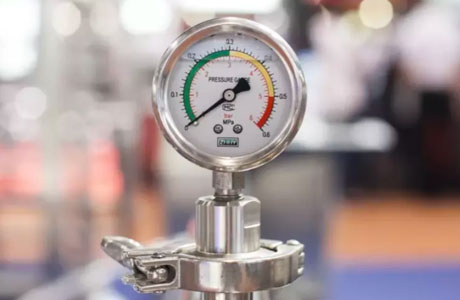
Application in HVAC and Refrigeration Units
Walk into any modern building, and the air you feel is likely being controlled by a pressure switch behind the scenes. HVAC (Heating, Ventilation, and Air Conditioning) systems rely on pressure switches to manage refrigerant flow and ensure system safety.
Let’s simplify:
These switches monitor refrigerant pressure. If it gets too high or too low, the switch will signal the system to shut down or adjust. This prevents compressor damage and keeps the environment comfortable.
In refrigeration units, they help regulate cooling cycles. For example, in cold storage or deep freezers, if pressure levels drop too low, it might mean a leak. The pressure switch alerts the control system or triggers a shutdown to avoid spoilage.
HVAC pressure switches also work as safety devices. They can sense blocked airflow, dirty filters, or frozen coils. In such cases, they prevent system overload by stopping the compressor until maintenance is done.
Bottom line? Without pressure switches, temperature control would be guesswork and system failures would be common.
Use in Compressors and Hydraulic Circuits
Compressors and hydraulic machines are like the muscles of the industrial world. And every muscle needs a brain. That’s where the pressure switch comes in.
In air compressors, pressure switches are essential for automatic start and stop control. For instance, once a compressor builds enough air pressure in the tank, the switch shuts it down. When pressure falls due to usage, the switch activates the compressor again.
In hydraulic circuits, pressure switches help maintain safe system pressures. They signal when pressure exceeds a certain point – triggering alarms or safety valves. This ensures that machines don’t over-pressurize and damage seals, pipes, or actuators.
Some systems also use pressure switches for sequencing. That means they only activate certain components when the required pressure is reached. This ensures smoother operation and better energy usage.
As a new engineer, remember this:
If a machine is failing to start, stalling under load, or making strange noises – always check the pressure switch. It might be trying to tell you something!
Integration in Oil and Gas Systems
The oil and gas industry is high-pressure – literally and figuratively. Here, pressure switches are more than tools – they’re lifelines.
In drilling operations, pressure switches monitor and control mud pumps. A sudden pressure drop might indicate a well kick or loss of circulation – dangerous events that demand instant action. The pressure switch alerts the control system or operator immediately.
In refineries and gas pipelines, pressure switches detect overpressure conditions. They work alongside safety valves to prevent explosions or environmental hazards.
These switches are often used in:
Pump protection
Compressor control
Wellhead automation
Pipeline safety systems
Because conditions in oil and gas are harsh, the switches used are rugged and explosion-proof. They need to perform reliably even in extreme temperatures, vibration, or corrosive environments.You might also find differential pressure switches used to monitor filter health. A clogged filter causes a pressure drop, which the switch detects and signals for maintenance.
Role in Machine Safety and Alarm Triggers
In factories, safety isn’t optional – it’s everything. That’s why pressure switches are often integrated into machine safety systems.
Take a hydraulic press, for example. If the pressure exceeds safe limits, the switch can shut down the system or trigger an alarm. This protects the machine, the product, and most importantly – the operator.
In automated systems, pressure switches are used to detect faults. Low air pressure? System won’t run. Sudden drop in hydraulic pressure? Emergency stop activated.
They can also monitor:
Clamping pressure in CNC machines
Lubrication systems
Coolant flow in machining centers
Brake air pressure in industrial cranes
Some pressure switches are wired directly to alarms, buzzers, or indicator lights. When something goes wrong, the operator gets an instant visual or sound cue.
As an engineer on the shop floor, learn to trust these devices. They speak the language of safety. And when they trip, don’t ignore them. Investigate.
A faulty pressure switch can be replaced. But ignoring its signal? That can cost production – or worse.
Conclusion
Pressure switches are more common than most people realize. In your home, they help regulate water pump operations to ensure steady water pressure. In commercial buildings, they are found in HVAC systems, controlling airflow and refrigerant pressure. In industrial plants, pressure switches are vital safety components for boilers, hydraulic systems, and air compressors. They are also used in automotive systems, oil and gas equipment, medical devices, and agriculture machinery. Their small size and straightforward operation make them easy to install, yet their impact is enormous. They keep machines running safely, prevent equipment failure, and ensure precise automation. Because they operate based on a simple principle—responding to pressure thresholds—they can be applied almost anywhere pressure control is needed. Whether you’re designing a factory, a farm irrigation system, or a household water pump, a pressure switch plays a role in maintaining operational stability. Their presence across sectors proves their versatility and importance.