Key Takeaway
Standard pressure switch settings vary by system type, but common household water pump systems are usually set at 30–50 psi or 40–60 psi. That means the pump turns ON at 30 or 40 psi (cut-in) and OFF at 50 or 60 psi (cut-out). These settings give a good balance of water pressure and pump protection. In air compressors, common pressure settings range from 90–120 psi. Industrial systems may use higher or lower ranges depending on the application. The gap between cut-in and cut-out is usually 20 psi, which prevents the system from turning ON and OFF too often. You can adjust these settings using the screws on the pressure switch. However, it’s important to stay within the safe pressure range recommended by the pump or compressor manufacturer. Using the wrong settings can reduce system life or even cause damage. Always check your equipment manual or consult an expert before changing the default settings.
Common Factory Setpoints for Water and Air Systems
Pressure switches often come with factory-preset values based on typical use cases. For water pumps, common presets include 20–40 PSI, 30–50 PSI, or 40–60 PSI. Air compressors might use ranges like 90–120 PSI. These standard settings work well for most residential or commercial systems and are adjustable depending on system needs. Manufacturers design presets with safety, efficiency, and pump longevity in mind. However, improper changes can cause short cycling, pressure drops, or motor overload. Always refer to the switch’s datasheet before making adjustments. Understanding these factory defaults helps users calibrate systems safely, without compromising performance or damaging connected equipment.
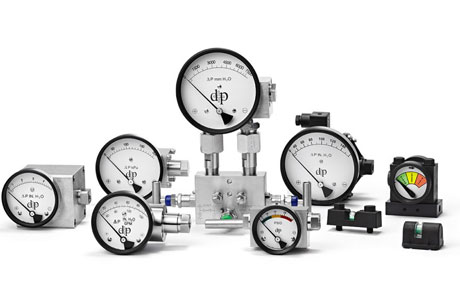
Understanding 20-40 vs. 30-50 vs. 40-60 PSI Ranges
Now here’s the fun part. Let’s compare the three most common pressure switch ranges.
20-40 PSI
Used in shallow well pumps and basic water delivery systems.
Lower energy consumption.
Less strain on plumbing, but may result in weak water flow.
30-50 PSI
The all-rounder. Most residential homes use this.
Provides a good balance of pressure and performance.
Suitable for average plumbing systems without upgrades.
40-60 PSI
High-performance option.
Best for homes with multiple bathrooms or large plumbing setups.
Also useful where strong pressure is needed (e.g., sprinklers, booster pumps).
You must also know about cut-in and cut-out:
Cut-in: The pressure at which the switch turns the pump ON.
Cut-out: The pressure at which the switch turns the pump OFF.
Example: In a 30-50 PSI switch, 30 PSI is cut-in, 50 PSI is cut-out.
Always measure real-world usage. For example, if users are complaining about low flow in the mornings, maybe you need to raise the cut-in slightly.
Industry Norms for Different Applications
Different industries have different needs. Let’s break it down:
Residential Buildings:
Typically use 30-50 PSI switches.
In some luxury homes with pressure boosters, 40-60 PSI may be installed.
Agricultural Farms:
Use 20-40 PSI switches for irrigation systems.
Drip irrigation doesn’t need high pressure, but overhead sprinkler systems do.
Industrial Facilities:
Air compressors usually need 90-120 PSI.
CNC machines or pneumatic systems may require tighter tolerances.
HVAC Systems:
Pressure switches play a role in chiller circuits and air handling systems.
Settings here are customized and usually depend on refrigerant type and system capacity.
Fire Fighting Systems:
These are critical. Often set to high-pressure levels.
Fail-safe design and accurate switching is non-negotiable.
As a rule, more pressure = more risk if not managed correctly.
So never assume one-size-fits-all. Ask: “What are we powering? What are the risks if pressure drops or spikes?”
That mindset will help you select the right settings.
Why Setpoints May Need Custom Adjustment
Just because the box says “factory set” doesn’t mean it’s perfect for you. Real-world conditions often demand tuning.
Here are common reasons:
Altitude: Higher altitudes lower atmospheric pressure, affecting system balance.
Pipe Size and Layout: Longer or narrower pipes cause pressure drops.
Water Tank Size: A larger pressure tank might benefit from higher cut-out.
User Demand: A family of 2 doesn’t need what a family of 8 does.
Another common case is replacing an old pump. You can’t always plug in the new switch and walk away. If the pump curve is different, the setpoints must be reviewed.
When adjusting:
Use a calibrated pressure gauge.
Start small (2-3 PSI changes).
Keep the differential (cut-out minus cut-in) reasonable: usually 20 PSI.
Custom adjustment isn’t just for performance—it extends system life too. Motors, pipes, and valves all thank you for it.
So don’t treat setpoints as “set-and-forget.” Think of them as tuning knobs. Fine-tune for the perfect performance.
Safety Considerations When Changing Settings
This is not just a technical point—it’s a responsibility.
When you change a pressure switch setting, you’re altering how the entire system behaves. That means risk, if done carelessly.
Start with Lockout/Tagout (LOTO). Never adjust live systems. Isolate power and drain pressure first.
Next, understand the equipment limits.
Every pump, tank, and pipe has a pressure rating.
Never exceed the maximum pressure marked on any component.
Use manufacturer documentation or nameplate data.
Use proper tools.
Adjust with insulated screwdrivers.
Avoid over-tightening springs inside the switch.
Document your changes.
Mark the new setpoints.
Notify the maintenance team.
Update the equipment manual.
Watch for side effects.
Higher pressure can strain joints and fittings.
It can also shorten pump cycles, leading to faster wear.
Always test the system after adjustment. Let it run a full cycle and check for leaks, overheating, or unusual vibrations.
If you’re unsure—stop. Call a senior technician or the manufacturer. Guesswork can be expensive and dangerous.
Remember, safety always beats speed.
Conclusion
Most pressure switches come pre-set from the factory with standard ranges like 30-50 PSI or 40-60 PSI. These settings are carefully chosen to suit typical applications like household water pumps, air compressors, or HVAC systems. The “cut-in” pressure is where the system starts, and the “cut-out” is where it stops. Standard settings help avoid overpressurization and maintain efficient cycling. However, not every system is the same. Custom adjustments may be needed for high-rise buildings, industrial tanks, or heavy machinery. Even then, it’s important to stay within safe operating limits. Never raise the pressure beyond what the pipes, valves, or tanks can handle. If your system seems to underperform at standard settings, check for blockages or wear before increasing pressure. Pressure that’s too high can cause leaks or equipment failure. Stick with known baselines unless you have a clear reason and proper tools to change them. Safety always comes first.