Key Takeaway
Testing a pressure switch means checking whether it turns ON and OFF at the right pressure. Start by turning off the system power and connecting a pressure gauge nearby. Slowly increase or decrease the system pressure and listen for a click sound from the switch. The click means it’s switching contacts. If there’s no click, or if it clicks too early or too late, it may be out of adjustment or faulty. For electrical switches, use a multimeter to see if the switch is opening and closing the circuit correctly. Set the meter to continuity or voltage mode, then watch for the signal to change as pressure moves across the cut-in or cut-out point. Make sure the pressure switch is clean and not blocked by dirt or rust. A properly working switch helps protect pumps, compressors, and machines. If it doesn’t respond as expected, it may need recalibration or replacement.
Using a Pressure Source for Manual Testing
Manual testing of a pressure switch involves applying a controlled pressure source—like a hand pump or compressor—and observing the switch’s response. Connect a pressure gauge and multimeter to monitor both pressure and electrical continuity. Gradually increase the pressure to see at what point the switch closes (or opens), then compare that to the expected setpoint. This method helps verify whether the switch activates correctly and consistently. It’s especially useful during installation, maintenance, or troubleshooting. Always test both rising and falling pressure to ensure proper cut-in and cut-out operation. Manual testing helps catch faulty switches, calibration drift, or worn diaphragms—avoiding potential failures in real-world conditions. Always isolate the system before testing for safety.
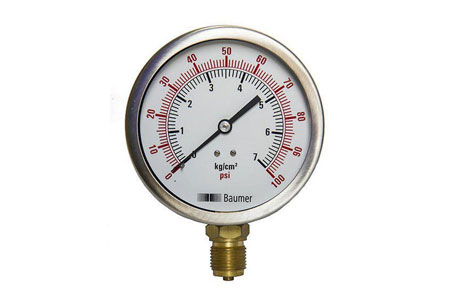
Verifying Switch Contacts and Voltage Response
Now comes the electrical side — where even experienced folks can make mistakes. One of the most underrated skills in an engineer’s toolkit is reading a multimeter correctly. So let’s make sure you’re doing it the right way.
First, disconnect the switch from the system’s load side. With the pressure source still connected, take your multimeter and set it to the continuity or voltage mode. Connect it across the switch terminals.
For a Normally Closed (NC) contact, you should see continuity when there’s no pressure. As pressure rises beyond the setpoint, continuity should break. For a Normally Open (NO) contact, the reverse happens — open at rest, closed after setpoint.
If the contact status doesn’t change even when pressure crosses the setpoint, something’s wrong. Could be contact welding, corrosion, or mechanical wear inside the switch.
To verify voltage, connect the multimeter between the input terminal and ground. Apply pressure. Once the setpoint is crossed, the output terminal should show voltage — if wired correctly.
Test Procedures for NC and NO Terminals
Every pressure switch is built with either NC (Normally Closed) or NO (Normally Open) terminals — and some have both. But testing them isn’t just about checking continuity. It’s about knowing why and when each type is used.
Let’s say you’re working with an air compressor. It uses an NC contact to stop the motor when the pressure hits 8 bar. That NC contact should remain closed (complete circuit) until pressure exceeds the setpoint. Once it does, the switch breaks the connection — motor stops. Your test must prove that sequence.
To test:
Attach your pressure source.
Connect a multimeter on continuity mode to the NC terminal.
Slowly increase pressure and observe.
The multimeter beep should stop precisely when the setpoint is reached.
Now for NO:
Same process — but this time, you should hear no beep until the pressure crosses the setpoint. After that point, the contact closes and the circuit completes.
If you’re not hearing the beep or voltage doesn’t flow as expected, don’t rush to replace the switch. Check for loose screws, dust, and debris — sometimes the smallest thing blocks movement.
In industrial environments, a faulty contact can mean a machine failure or even a safety hazard. Don’t underestimate this test — even if it looks basic.
Signs of Delay, Sticking, or No Response
This is the silent killer. Your switch might pass all tests in ideal conditions — but during real use, it sticks, delays, or doesn’t respond at all. That’s why reliability testing matters more than pass/fail outcomes.
Here’s what to look for:
Delay: When pressure hits the setpoint, but the switch responds 2–3 seconds later. Not good for fast-reacting systems.
Sticking: The switch doesn’t return to its original state after pressure drops. You may hear one click, but not the second.
No Response: Pressure crosses well beyond the rated setpoint — and the switch remains dead. No mechanical click. No electrical output.
What causes these? Dirt inside the diaphragm, weak springs, or worn internal seals. If a switch hasn’t been activated in months, it might get “lazy.” Yes, just like us. It needs exercise.
Tools Required for Accurate Testing
Let’s get practical. You can’t just rely on your ears and instincts. You need tools — and the right ones make all the difference. Here’s what every engineer must have when testing a pressure switch:
Digital Pressure Gauge: Your most critical tool. Analog gauges are okay, but digital ones give you real-time, precise pressure readings.
Hand Pump with Pressure Regulator: For manual pressure application. This helps simulate rising pressure gradually.
Multimeter: Preferably with continuity buzzer and voltage range. It helps verify contact behavior.
Test Leads & Clips: To make safe, hands-free connections while applying pressure.
Notebook or Digital Log Sheet: Trust me, documenting your readings helps you catch patterns, especially with intermittent faults.
Safety Gear: Gloves, goggles, and sometimes ear protection if you’re testing near operating machinery.
Conclusion
Testing a pressure switch is not guesswork—it’s about using the right tools to ensure precise and safe system behavior. Begin by isolating the switch from power and pressure. Then use a calibrated pressure source (like a hand pump or compressor) to apply gradual pressure. Connect a multimeter to the switch terminals to observe when the contacts open or close. This helps you verify if the switch activates at the correct setpoint. If the switch reacts too early, too late, or not at all, it may need adjustment or replacement. Test both normally open (NO) and normally closed (NC) terminals to ensure full functionality. Avoid relying only on system behavior (like pump noise or cycles); those can be misleading. Trust your test data, not assumptions. Thorough testing also helps identify hidden issues such as contact sticking or pressure drift. Accurate testing ensures your switch performs exactly when needed—no surprises.