Key Takeaway
There are mainly two types of pressure switches: mechanical and electronic. A mechanical pressure switch uses a spring and diaphragm. When pressure pushes against the diaphragm, the spring moves and triggers an electrical contact. These switches are simple, low-cost, and used in pumps, compressors, and HVAC systems. The cut-in and cut-out settings are adjusted using screws. An electronic pressure switch, on the other hand, uses a pressure sensor and internal circuit to monitor pressure. It provides more accuracy and often includes a digital display. Electronic types can also be programmed for multiple switching points or delays. These are used in modern industrial automation systems where precise pressure control is needed. In short, mechanical switches are best for simple ON/OFF control, while electronic switches are ideal for advanced applications with detailed control and data monitoring. Your choice depends on your system needs, budget, and how much precision is required.
Mechanical Pressure Switch and Its Operation
A mechanical pressure switch operates using a diaphragm, piston, or bellows that flexes when pressure builds. This movement pushes against a spring, causing electrical contacts to open or close. It’s a simple, reliable mechanism ideal for ON/OFF control in pumps, compressors, and tanks. Mechanical switches are favored in rugged, vibration-prone environments because of their durability and low cost. They don’t need external power to operate and can be used in standalone systems. Adjustment is typically done via a screw to change the spring tension and setpoint. These switches are widely used in industrial, agricultural, and HVAC applications where basic automation is required without the need for digital feedback.
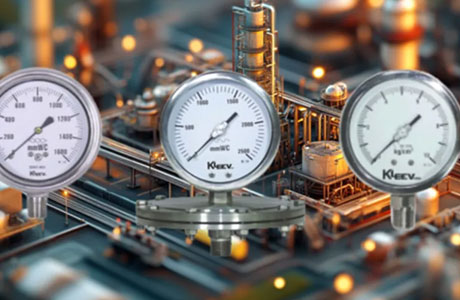
Electronic Pressure Switch with Digital Features
Now let’s step into the future — electronic pressure switches. These are smarter, more accurate, and more flexible than their mechanical cousins. Instead of a physical mechanism, they use a pressure sensor — usually piezoresistive, capacitive, or strain gauge — to detect pressure.
The signal from this sensor is processed electronically and can be configured using a digital display or interface. You can program setpoints, delays, and even hysteresis settings. No need for a screwdriver — just use the keypad or software.
Some advanced models even have IO-Link or other industrial communication protocols. That means they can talk to PLCs, send diagnostic data, and support predictive maintenance.
They shine in applications where precision and flexibility are critical. For example, in bottling plants, electronic switches ensure consistent pressure at each stage. In automotive test benches, they provide fast response and digital outputs to the control system.
You’ll also find these in clean rooms, pharmaceutical manufacturing, and high-speed machinery — places where accuracy matters and system integration is key.
But they do rely on electronics. So, they’re more sensitive to voltage surges, moisture ingress, and EMI. And yes, they’re pricier than mechanical switches. But the value they deliver in high-end applications often justifies the cost.
If you’re working in a data-driven, tightly controlled environment, electronic pressure switches are the way to go.
Comparison of Response Times and Accuracy
When you compare mechanical and electronic pressure switches, two major factors stand out: response time and accuracy.
Mechanical switches usually have a slower response time. That’s because the system has to wait for physical components to move and make or break a contact. We’re talking milliseconds to a few seconds depending on the spring tension, damping, and design.
Electronic switches, on the other hand, are lightning-fast. They sense pressure changes in real-time and send signals almost instantly. In high-speed applications like automated assembly lines, that difference can make or break your process.
Accuracy is another key point. Mechanical switches usually have a tolerance range of around ±3% to ±5%. That might be fine for general-purpose use, but not in precision systems.
Electronic switches typically have accuracy ranges of ±0.5% or better. Plus, you can fine-tune them digitally, reducing error caused by manual adjustment.
But here’s a reality check — ultra-high accuracy doesn’t matter in every application. If you’re monitoring air pressure in a tire inflation system, you might not need sub-millibar precision. But in a chemical dosing system? You absolutely do.
So always ask yourself: what does the system really need?
Speed and precision are valuable — but only if your application demands them.
Application Scenarios for Each Type
Mechanical pressure switches still dominate in basic systems. Think about well pumps, air compressors, or agricultural sprayers. In these setups, the pressure range is broad, the operating environment is tough, and high precision isn’t mandatory.
For example, a 3-phase air compressor uses a mechanical switch to start and stop based on pressure levels in the tank. No PLC. No sensor output. Just simple mechanical logic. And it works beautifully for years.
You’ll also find mechanical switches in industrial boilers, cooling systems, and even older hydraulic systems.
But as soon as the environment becomes digital — where feedback loops, data logging, or system diagnostics matter — electronic switches take the lead.
In modern factories, electronic switches allow operators to see the exact pressure on a screen. They can log data over time. Maintenance teams can get alerts if a switch is nearing failure.
Even in food processing lines, where hygiene is critical and fast washdowns are common, electronic models rated with IP67/IP69K make more sense.
So the decision is not just about budget. It’s about context. Choose mechanical when simplicity and ruggedness are key. Choose electronic when accuracy, diagnostics, and integration matter.
Pros and Cons from a Maintenance Viewpoint
Let’s talk maintenance — something every engineer must think about.
Mechanical pressure switches are easy to service. You can clean or replace diaphragms, springs, or seals with standard tools. Spare parts are cheap and widely available. And technicians don’t need programming skills to calibrate or replace them.
But they can drift over time. Springs lose tension. Seals degrade. And if you’re not checking regularly, that drift can cause delays or shutdowns.
Electronic switches require less mechanical maintenance since there are fewer moving parts. But they come with their own issues.
Moisture ingress, EMI (electromagnetic interference), or voltage spikes can damage internal electronics. Firmware bugs or configuration errors can also cause malfunctions. So, you’ll need a technician with some electronics know-how.
On the plus side, many electronic switches offer self-diagnostics. They can alert you when there’s an internal fault, reducing the time spent on troubleshooting.
And if your plant uses predictive maintenance or condition monitoring, electronic switches integrate easily with those systems.
Conclusion
Pressure switches come in two primary types: mechanical and electronic. Mechanical pressure switches use springs and diaphragms to open or close contacts when a set pressure is reached. They’re simple, reliable, and ideal for rugged applications. Electronic pressure switches, however, offer advanced features like digital displays, programmable setpoints, and output signal options (PNP, NPN, analog). While mechanical switches are often preferred for basic ON/OFF tasks, electronic ones are better suited for PLC-controlled systems and applications needing remote monitoring. Despite their differences, both types aim to do one thing—control pressure accurately and safely. The choice depends on your application’s complexity, environment, and budget. In many systems, both types may even work side-by-side. Whether you need simplicity or smart control, pressure switches—mechanical or electronic—are essential components for pressure-based automation. Always choose the right type based on your control requirements, response time, and integration needs.