Key Takeaway
The operating range of a pressure switch is the pressure window in which it can safely and accurately work. For example, a switch might have a range of 30 to 150 psi, meaning it can be adjusted to turn ON or OFF anywhere between those limits. Each pressure switch has a minimum and maximum rating, usually printed on its label or datasheet. Operating outside this range may lead to inaccurate switching or damage. When setting the cut-in and cut-out points, make sure they fall within the operating range. Also, consider the differential range — the gap between ON and OFF points — which may also be limited. For example, some switches may require at least a 15 psi difference. Always follow the manufacturer’s specs. Choosing the right operating range ensures safe function and long life for both the switch and the connected equipment, whether in pumps, compressors, or HVAC systems.
Minimum and Maximum Pressure Limits
Every pressure switch has a minimum operating pressure (cut-in), a maximum pressure (cut-out), and two critical limits: proof pressure and burst pressure. Proof pressure is the temporary maximum a switch can handle without damage. Burst pressure is the point of failure. Always choose a switch with an operating range slightly above your system’s normal peak. Exceeding these values can deform the diaphragm, damage internal components, or result in complete failure. It’s also important to consider environmental conditions like temperature and fluid compatibility, which can shift effective limits. Staying within manufacturer-specified limits ensures long-term reliability, system safety, and uninterrupted operation.
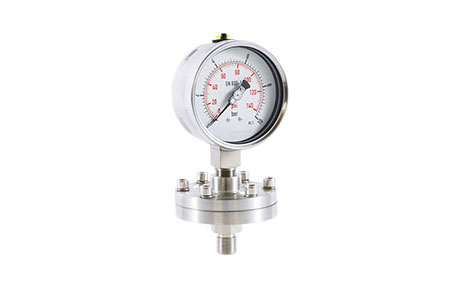
Working Range vs. Proof and Burst Pressure
Here’s where most junior engineers get it wrong. You look at a switch and see 0-10 bar written on it. You assume it can handle 10 bar all day, every day. That’s not how it works.
There are three pressure numbers you must know:
Operating Range (e.g., 2 to 8 bar)
Proof Pressure (e.g., 12 bar)
Burst Pressure (e.g., 25 bar)
The operating range is where the switch is designed to perform reliably. Proof pressure is the maximum pressure the switch can survive temporarily without permanent damage. Burst pressure is the point at which the switch will literally break apart.
Do not confuse these. Just because a switch won’t explode until 25 bar doesn’t mean you can use it at 20 bar.
Example: Let’s say your pump system has occasional pressure spikes up to 11 bar. If your switch has a proof pressure of 10 bar, those spikes will slowly kill it.
Environmental Effects on Range Accuracy
Now let’s talk reality. Industrial sites aren’t labs. Heat, vibration, dust, humidity, and even installation angle can all affect pressure switch performance.
Temperature is the biggest villain here. Extreme cold or heat can shift the setpoints of your switch. For example, a switch set to trip at 5 bar may actually trip at 4.5 bar if exposed to freezing temperatures.
Vibration can cause contact wear or relay chattering. Over time, this throws off your accuracy or causes electrical arcing inside the switch.
Dust and moisture affect sealing and diaphragm movement. Especially in food, pharma, or chemical plants, ingress protection (IP rating) matters a lot.
Mounting the switch incorrectly can also change how it responds. If it was designed to be mounted vertically, placing it sideways might stress the internal spring or diaphragm.
Matching Range to Application Load
Selecting the correct operating range is about knowing your application load profile. Does your system experience slow ramp-up pressure? Or are there sudden spikes?
Let’s say you have a booster pump that starts at 2.5 bar and shuts at 5 bar. A switch with a range of 1.5–6 bar and a deadband of 1 bar would be ideal. If the switch only starts at 3 bar, you’ll have late starts or no starts at all.
Similarly, in compressor control, pressure rise happens quickly. You need a switch that can not only detect the spike but handle it repeatedly.
Don’t Overspec. Choosing a switch with a 0–100 bar range for a 4 bar application gives you poor accuracy. Instead, pick the closest suitable range.
Also consider system media. Are you switching water, air, steam, or oil? Viscous or corrosive fluids require diaphragm materials and enclosures that suit the medium. This indirectly affects the switch range too.
And of course, check the electrical load. A pressure switch may be great at handling 5 bar pressure, but what if your load circuit needs 15A switching capacity and the switch is rated only for 5A?
Quick advice: Never select a switch just based on pressure. Always evaluate pressure, media, electrical load, and environment together.
This will help you match not just the switch range, but the total capability to the application.
Manufacturer Specifications and Tolerances
Each manufacturer provides detailed specifications, and trust me — they matter.
Every switch has factory-calibrated setpoints, tolerances, and performance curves. You’ll find terms like:
Repeatability: How close the switch trips at the same point every time.
Hysteresis: The difference between the trip and reset point.
Tolerance: The allowed variation from the target point (like ±0.5 bar).
Let’s say a switch is set to trip at 6 bar with a tolerance of ±0.2 bar. That means it could trip anywhere between 5.8 and 6.2 bar. That variance could be fine for irrigation pumps but disastrous for an autoclave system.
Also, some switches are field-adjustable, others are factory-sealed. Don’t try to tweak sealed switches unless you’re trained or authorized.
Best practice: Download the manufacturer’s product sheet, installation guide, and if available, test report. Cross-check everything before purchase.
And never mix brands casually. A 6 bar switch from Brand A may behave differently than a 6 bar switch from Brand B due to internal spring and diaphragm designs.
Engineers on the shop floor swear by certain brands because of years of trouble-free service. That’s the value of first-hand experience.
Finally, always validate your pressure switch settings post-installation using a calibrated gauge or digital meter. Never rely on the printed label alone.
Conclusion
Every pressure switch has a defined operating range—minimum and maximum pressure it can handle safely. Exceeding these limits may not trigger failure immediately, but it weakens internal components like springs and diaphragms. Over time, this causes malfunction or dangerous behavior. Beyond the working range, there’s a proof pressure (temporary overload capacity) and burst pressure (catastrophic failure point). Always select a switch with a range suited to your system, leaving a safety margin. Environmental conditions like heat, altitude, or vibration can also affect range performance. Don’t just focus on functionality—consider safety, reliability, and longevity. A well-matched pressure switch ensures peak performance while reducing downtime, damage, and unexpected replacement costs.