Key Takeaway
Pressure gauges are used to measure the pressure of gases or liquids in pipelines, tanks, compressors, HVAC systems, and many other applications. They provide real-time readings that help operators monitor performance, maintain safety, and optimize system efficiency. For instance, in industrial automation, gauges ensure processes stay within safe operating pressure ranges. In pneumatic or hydraulic systems, they prevent overloading by displaying system pressure. In residential settings, they’re found in water heaters or pressure cookers. Pressure gauges are critical in detecting leaks, blockages, and pump failures. Depending on the system, they may use mechanical mechanisms or electronic sensors to measure and display the pressure.
Monitoring Mechanical Systems in Real-Time
A compressor fails in the middle of a production shift. Everything stops. Workers stand idle. Clients get delayed deliveries. Losses pile up. All of this — because no one noticed the system was under pressure. That’s why real-time monitoring is not a luxury. It’s a necessity.
In modern industries, we no longer “wait and check.” We watch systems live — as they run, pulse, and breathe. With sensors and smart control panels, we track pressure, temperature, vibration, flow rates, and more. If anything goes outside safe limits, alerts fire instantly. No guessing. No delays. You see what’s happening and take action before things go wrong.
This real-time data isn’t just for alerts. It helps us find patterns. If a motor gets slightly hotter every Friday afternoon, maybe it’s working harder due to a shift in load. You wouldn’t notice this on paper, but real-time systems catch it. That’s how we prevent damage before it starts.
Whether you’re monitoring a hydraulic press or a chilled water pump, live feedback ensures smoother operation and quick response. It keeps your equipment healthy and your production on track.
So if someone asks why we need monitoring tools, tell them this — it’s the eyes and ears of your machines.
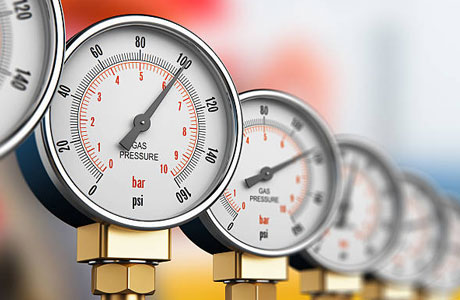
Ensuring Safety in Boilers, Compressors, and Pumps
Let’s get serious for a second. Boilers, compressors, and pumps are not just workhorses. They can be dangerous if ignored.
Take boilers for example. If pressure goes beyond safe levels and no one notices, it can literally explode. And that’s not just downtime. That’s a disaster. Compressors? Same thing. Overheating or excess pressure can lead to failure or even fire. Pumps? They might seem harmless, but a worn-out seal or a dry run can leak chemicals or stop an entire cooling system.
Now how do you prevent that?
You guessed it — real-time monitoring. It’s like having a safety officer on duty, 24/7. Pressure sensors, temperature indicators, and vibration monitors are placed strategically. If pressure rises beyond the safe mark, the system shuts down or sends a warning. If vibration goes off balance, we know something’s wrong inside. Maybe a bearing is damaged. Maybe alignment is off. You won’t see it with your eyes, but sensors do.
The good part? These systems are not hard to install. And they talk to you through dashboards, alarms, or even mobile alerts. You can take action from anywhere.
The lesson here is simple — when you monitor boilers, compressors, and pumps actively, you’re not just improving efficiency. You’re saving lives, saving time, and saving your job.
Applications in HVAC, Oil, Pharma, and Food Sectors
Every sector has different priorities. But one thing is common — no one likes sudden shutdowns or unsafe conditions.
In HVAC systems, real-time monitoring ensures proper airflow, temperature, and energy efficiency. If pressure drops in a duct or a fan slows down, the system tells you. No room gets too hot or too cold. Comfort stays consistent. Downtime stays away.
In the oil and gas industry, the risks are higher. A leak, pressure rise, or heat spike could cause a fire. That’s why pressure gauges and flow meters are critical. And they’re monitored constantly — not checked manually. Real-time alerts help prevent serious incidents.
Pharma is different. It’s all about purity and compliance. If a sterile mixer goes off temperature by even 2 degrees, the batch can go to waste. And that’s not just loss — it’s non-compliance. Pharma companies use real-time sensors to meet FDA or WHO standards. Everything is documented and tracked live.
Food processing? Temperature and pressure must be controlled to ensure hygiene. If milk pasteurization drops in temperature, bacteria may survive. That’s a direct risk to public health. So real-time control is non-negotiable here too.
Different industries. Same need. The keyword is trust. And trust only comes when you can see that everything’s okay — in real-time.
Preventing System Overloads and Failures
Let’s be clear — mechanical failures don’t happen suddenly. They build up slowly.
It might start with a tiny increase in pressure. A small temperature fluctuation. Slight extra vibration. On its own, it might seem harmless. But over time, it leads to a breakdown.
That’s where real-time monitoring becomes your superpower.
Imagine a situation where a cooling system in a factory is slowly losing efficiency. Without real-time pressure and flow sensors, the team might never know until the motor burns out. But with sensors, you’ll get early signs. Maybe the flow rate is dropping. Maybe power consumption is going up. That means you can intervene — before the failure happens.
The same applies to compressors that are being overworked, or pumps that are struggling due to airlocks. All these issues can be caught early through continuous tracking.
This kind of proactive approach isn’t just about fixing problems. It’s about saving cost. Maintenance teams can schedule minor repairs instead of dealing with full-blown damage. There’s less downtime, fewer emergency calls, and happier management.
Think of it this way — real-time monitoring is like checking your health daily instead of waiting for a heart attack. Don’t wait for the bang. Prevent the breakdown.
Role in Routine Maintenance and Inspection
Now let’s talk about the part most engineers overlook — routine maintenance.
In the past, inspections were done manually. Every month or quarter, someone would go around with a checklist, take readings, and note down values. It worked. But it was slow, often inaccurate, and always reactive.
With real-time monitoring, the game changes.
You don’t need to guess when to service a pump. You’ll know. You don’t have to wonder if a valve is behaving oddly. The data shows you trends. You can see if a motor is vibrating more than usual. Or if a filter is clogging up because airflow has reduced.
This leads to something magical — predictive maintenance. Instead of fixing after failure or checking every 30 days blindly, you maintain only when needed. Based on actual machine behavior. It’s smarter, faster, and more cost-effective.
And let’s not forget audits. If you’re in a regulated industry like food or pharma, you’ll love this. Real-time records prove that your equipment stayed within safe limits — no paper logs, no confusion. Everything is saved, time-stamped, and accurate.
As a new engineer, your goal is not to just fix things. It’s to prevent them from going wrong. And real-time monitoring is your best friend here.
Conclusion
Pressure gauges serve as frontline indicators for system health. They show real-time pressure changes that may signal blockages, leaks, or abnormal operation. When used properly, they prevent catastrophic failure by providing early warnings. For example, in a steam boiler, a sudden drop or spike in pressure could indicate scale buildup or valve failure. Regularly checking pressure readings helps you take corrective action before problems worsen. Gauges also confirm that pumps, compressors, and regulators are operating within safe limits. As a low-cost tool, they offer high value in preventive maintenance programs. Consistent monitoring keeps systems efficient, safe, and long-lasting.