Key Takeaway
To connect a Siemens S7-300 PLC:
Connect a PG/PC to the CPU using MPI cable, Profibus cable, or Industrial Ethernet (if CP installed).
In SIMATIC Manager (Step 7 Classic) or TIA Portal, scan for accessible devices.
Set communication parameters (MPI address, Profibus network settings, or IP address).
Download the hardware configuration and program.
Ensure correct project settings, matching CPU type, firmware version, and network topology.
Also, verify the PG/PC interface settings on your laptop match the physical communication method being used (MPI adapter, Ethernet card, etc.).
Interface Options: MPI, PROFIBUS, Ethernet
The Siemens S7-300 offers three primary interface options for communication: MPI (Multi-Point Interface), PROFIBUS, and Ethernet. These protocols are designed to connect the PLC to various network devices, ensuring that data exchange between systems is reliable and efficient.
MPI: This is a traditional Siemens protocol used to connect PLCs and other devices within the same network. It operates at a speed of up to 187.5 kbit/s, making it suitable for smaller networks or simpler applications.
PROFIBUS: This is an industrial communication standard that offers higher speed and is ideal for larger systems with more devices. PROFIBUS DP (Decentralized Peripherals) allows for fast data transfer between the PLC and peripheral devices, such as sensors and actuators.
Ethernet: The fastest and most flexible option, Ethernet is commonly used for connecting to PCs, HMIs, or other networked devices. It offers higher bandwidth and is suitable for more complex, large-scale automation systems.
Understanding these options is the first step in choosing the right communication protocol for your specific application. Depending on your system requirements and the number of devices involved, selecting the correct interface will ensure efficient communication within your network.
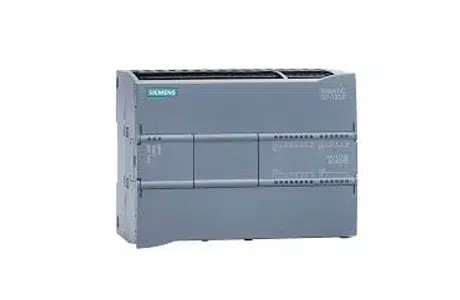
Physical Connection Steps and Wiring Setup
Once you’ve selected your communication protocol, the next step is the physical connection. For Siemens S7-300, this involves wiring the PLC to the network using the appropriate cables and connectors.
For MPI: You will use a standard MPI cable to connect the S7-300 PLC to the programming device or other devices. The connection requires a special MPI connector on both ends, ensuring a stable connection for data transmission.
For PROFIBUS: PROFIBUS requires a twisted-pair cable or fiber optic cables for communication. The cables need to be terminated properly at both ends to prevent signal reflection, which can cause communication errors. Make sure to follow the manufacturer’s instructions for wiring and termination.
For Ethernet: Ethernet cables (Cat 5 or higher) are used for this connection. The S7-300 can be connected directly to a switch or router via an Ethernet port, and this method requires minimal configuration. Simply ensure the cables are securely plugged into the PLC and networking equipment.
Make sure that all connections are securely fastened and that the cables are correctly routed to avoid interference. The quality of the physical connection plays a crucial role in the stability of the communication.
Communication Configuration in STEP 7
STEP 7 is Siemens’ configuration and programming software used to set up the PLC’s communication parameters. After wiring the PLC, you need to configure it to communicate with other devices in your network.
Open STEP 7: Once you’ve installed STEP 7 on your computer, open the software and connect it to your Siemens S7-300 PLC.
Configure Communication Parameters: Navigate to the “Network” section within STEP 7 and choose the appropriate interface (MPI, PROFIBUS, or Ethernet). For Ethernet connections, you will be required to enter the IP address and subnet mask.
Add Devices: In the software, you will add all devices that will communicate with the PLC, such as HMIs, sensors, or other PLCs. Each device must be configured with its respective address and communication settings.
The communication configuration in STEP 7 is where most of the setup work happens. It’s important to follow each step precisely, as misconfigurations can lead to connection issues or unstable communications. Double-check all settings before proceeding.
IP Address Assignment and Network Discovery
For Ethernet-based connections, assigning the correct IP address to your S7-300 PLC is essential for proper network discovery. This step ensures that the PLC can be found on the network and can communicate with other devices.
Assign the IP Address: In STEP 7, navigate to the Ethernet settings for your PLC. Assign a unique IP address that fits within your network’s IP range. Make sure to also assign the correct subnet mask and gateway, especially if you are connecting across different subnets.
Test the Connection: Once the IP address is set, you can test the connection by pinging the PLC from a computer or other networked device. This step helps verify that the PLC is correctly configured and accessible.
Network Discovery: Use STEP 7’s network discovery feature to scan for all connected devices. This ensures that your PLC is properly visible on the network, and no devices are left out of the communication loop.
A successful IP configuration guarantees that your PLC is part of the network, enabling it to exchange data with other devices effectively. If you encounter issues during this phase, verify that your network settings are correct and that there are no conflicts with other devices.
Troubleshooting Connection Issues
Even with a proper setup, issues may arise during the connection process. Here are some common troubleshooting steps to resolve potential problems:
Check Cables and Connections: If the PLC is not communicating, the first step is to check all physical connections. Make sure that cables are properly plugged in, and that there are no loose or damaged wires.
Verify Communication Parameters: If the connection still isn’t working, double-check the communication settings in STEP 7. Ensure that the right interface (MPI, PROFIBUS, or Ethernet) is selected, and verify that the address settings for all connected devices are correct.
Inspect the PLC’s Status LEDs: Siemens PLCs are equipped with status LEDs that indicate whether the device is connected and operating properly. If the LEDs show an error, refer to the Siemens documentation to identify the issue.
Use Diagnostics Tools: STEP 7 offers diagnostic tools to help identify and troubleshoot connection problems. You can use the software to monitor network traffic and pinpoint the source of communication failures.
Troubleshooting can be time-consuming, but taking a systematic approach will help identify and resolve issues efficiently. Always test the system step by step to pinpoint where the breakdown occurs.
Conclusion
Connecting your Siemens S7-300 PLC is a straightforward process when you follow the correct steps. Begin by choosing the right communication interface (MPI, PROFIBUS, or Ethernet), ensure the physical wiring is set up properly, and configure the communication settings in STEP 7. With the correct IP address and network discovery, your S7-300 will be fully integrated into your automation network. Always troubleshoot systematically to resolve any connection issues. By following these steps, you’ll ensure that your Siemens S7-300 PLC is set up correctly and ready to support your industrial automation tasks.