Key Takeaway
A pressure switch works by monitoring system pressure through a sensing element like a diaphragm or bellows. When the system pressure reaches a pre-set threshold (cut-in or cut-out), the element deforms and triggers a mechanical or electronic contact. This switch action can energize or de-energize pumps, compressors, alarms, or other control devices. The switch resets when the pressure returns to normal operating limits. Mechanical pressure switches operate purely through spring tension and contact mechanisms, while electronic versions use sensors and digital logic. Pressure switches are crucial in automating processes, protecting equipment, and maintaining safety in pressurized systems.
Internal Mechanism and Trigger Response
Inside a pressure switch, the trigger mechanism consists of:
A sensing element (diaphragm, bellows, or piston)
An adjustable spring to set the activation point
A snap-action switch to open or close electrical contacts
When pressure exceeds the spring force, the element deflects and trips the switch. The snap action ensures clean, fast switching to prevent arcing or contact bounce.
Some switches have fixed differential (hysteresis), while others are adjustable. Understanding this response time and hysteresis helps you select the right switch for your process needs.
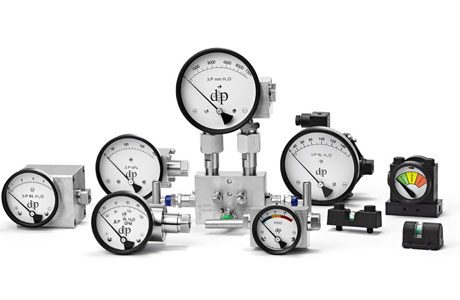
Set Point and Differential Adjustment Explained
Pressure switches have two important settings:
Set Point: The pressure at which the switch activates (trips)
Differential: The pressure range the system must fall back before the switch resets
Example: If a switch trips at 6 bar and has a 1-bar differential, it resets at 5 bar.
This prevents chattering — rapid ON/OFF switching — especially in fluctuating systems. Differential can be fixed or adjustable. Understanding how to fine-tune both helps improve control logic and protect equipment from unnecessary cycling.
Signal Transmission to Control Systems
Modern pressure sensors transmit signals in various formats:
Analog: 4–20 mA (most common), 0–10 V
Digital: Modbus, HART, CAN bus
These signals feed directly into:
PLCs
DCS systems
Remote monitoring panels
Safety interlocks
Choosing the right signal type ensures reliable data flow, interference resistance, and easy integration with existing control infrastructure. Use shielded cables and proper grounding for long-distance or noisy environments.
Fail-Safe and Redundancy Features in Switches
Fail-safe designs ensure that pressure switches default to a safe state during:
Power failure
Sensor malfunction
Signal loss
Techniques include:
Normally closed contacts that open under pressure loss
Redundant pressure switches (dual-sensor setups)
Mechanical backup switches in case digital sensors fail
Redundancy is essential in:
Boilers
Hydraulic presses
Critical chemical processes
Aerospace or medical devices
Fail-safe configurations protect not just equipment but also personnel — reducing the risk of overpressure, leaks, or explosions when a primary control fails.
Mechanical vs Digital Pressure Switch Operation
Mechanical pressure switches use springs and diaphragms to actuate contacts when pressure reaches a threshold. They’re:
Inexpensive
No power needed
Rugged and simple
Digital pressure switches use electronic sensors and relays:
Programmable setpoints
High accuracy and repeatability
Remote configuration and diagnostics
Suitable for IoT/PLC integration
Use mechanical when:
Budget is limited
Power is unavailable
Simplicity is valued
Use digital when:
Precision is key
Integration is required
Remote access is beneficial
Both have their place. Understand your system’s needs, and choose the switch that offers reliability and control without overengineering.
Conclusion
Whether you’re running an air compressor or automating a production line, the right pressure switch can make or break system performance. It determines when actions are triggered—ensuring safety, saving energy, and optimizing response times. Adjustable pressure switches allow fine control over start/stop conditions, improving equipment life and reducing downtime. Digital switches bring added intelligence—offering diagnostics, alarms, and network integration. Choosing the right switching logic (NO or NC), response delay, and control voltage ensures compatibility with your setup. In short, the pressure switch is a small component that makes smart systems possible. Every reliable process starts with knowing when—and how—to switch.