Key Takeaway
To prevent pressure gauge damage, use gauges within 25–75% of their full-scale range. Install pulsation dampeners or snubbers to protect against sudden pressure spikes. Use chemical seals or isolators when working with corrosive fluids. Choose materials compatible with the process medium. Protect the gauge from excessive vibration by using remote mounting kits or liquid-filled designs. Avoid mechanical shock during installation. Calibrate the gauge regularly to ensure accurate readings. Ensure that the temperature range is suitable for both ambient and process conditions. Lastly, always mount the gauge vertically unless it’s designed for another orientation, and keep it clean to prevent clogging.
Avoiding Overpressure with Snubbers and Dampers
To protect gauges from rapid pressure surges, use accessories like:
Snubbers: Porous orifice fittings that slow down pressure impulses
Pulsation dampers: Use bellows or diaphragms to absorb shock
Restrictor valves: Narrow passages that limit flow rate
Install these between the pressure source and the gauge, especially in systems with pumps, hydraulic actuators, or compressors.
Choosing the right snubber depends on the fluid type — liquid or gas — and viscosity. Always size these components properly, or they’ll either clog or not protect the gauge effectively.
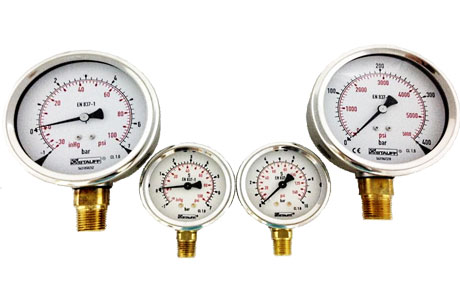
Installing Gauges Away from High Vibration Zones
Vibration damages gauges over time. It causes:
Pointer oscillation (making readings hard to interpret)
Internal wear in gears and linkages
Loosened fittings or cracked solder joints
Solutions:
Install the gauge on a remote mounting bracket
Use flexible capillary tubes or impulse lines
Choose glycerin-filled or silicone-filled gauges
For high-vibration equipment like compressors or pumps, these small design choices greatly increase gauge lifespan and reliability.
Using the Right Gauge for Corrosive or Hazardous Media
In harsh chemical or explosive environments, standard gauges won’t last — or worse, may leak or explode.
For corrosive media:
Use Monel, Hastelloy, or PTFE-lined gauges
Install chemical seals with compatible diaphragms
For hazardous (explosive) zones:
Use ATEX or IECEx certified gauges
Choose flameproof or intrinsically safe designs
Avoid exposed electrical contacts unless sealed
Choosing based on media compatibility and location classification prevents accidents and ensures long-term reliability.
Protecting Against Temperature and Humidity Fluctuations
Temperature swings cause:
Fluid expansion in liquid-filled gauges
Elastic element fatigue
Condensation inside non-sealed gauges
Humidity can:
Fog the dial
Corrode internals
Cause electrical failure in digital sensors
Solutions:
Use vent plugs for pressure equalization
Choose IP-rated or hermetically sealed gauges
Install sunshields for outdoor gauges
Store spares in dry, cool areas
Designing for environmental protection improves performance consistency and extends instrument life.
Scheduling Regular Inspections and Calibrations
To avoid unplanned failures, set a preventive maintenance schedule for all pressure gauges.
Suggested schedule:
Daily/Weekly: Operator visual checks for cracks, leaks, odd readings
Monthly: Manual zero check during system rest
Quarterly: Review logs, identify abnormal trends
Annually: Full calibration by trained personnel or lab
Critical gauges (e.g., in boilers, medical, or pharma setups) may require quarterly calibration. Use asset tracking software or spreadsheets to track each gauge’s status and schedule.
Label every gauge with:
Date of last calibration
Next due date
Technician ID
A systematic approach ensures gauges don’t fail silently and protects your operation from costly errors.
Conclusion
Preventing damage to your pressure gauges is more cost-effective than dealing with failure. Use snubbers to reduce pulsation, install gauges away from vibration-prone zones, and choose corrosion-resistant materials for harsh media. Ensure correct mounting—vertical or horizontal depending on design—and avoid over-tightening. Use shutoff valves or siphons in high-temperature systems to minimize stress. Environmental conditions like humidity, dust, or temperature swings can impact longevity, especially for digital models. Proactive maintenance—like cleaning ports, inspecting connections, and checking zero—can double the life of your gauges. A little prevention protects accuracy, extends usability, and keeps your system safe and operational. Don’t wait for failure—shield your gauge from it.