Key Takeaway
A pressure switch is usually not analog. It works more like a digital ON/OFF device. When pressure crosses a set level, it opens or closes an electrical circuit — just like flipping a switch. It does not send a pressure signal like a pressure transmitter does. However, there are some advanced types called electronic pressure switches that may have digital displays and programmable settings. Even then, their output is still digital — either ON or OFF — not a range of values. Analog pressure measurement is typically done with pressure transmitters, which send continuous signals (like 4–20 mA) to show the exact pressure. So, while a pressure switch may use electronic parts, its main function is still digital in nature. It acts only when the pressure is too high or too low, making it ideal for control tasks. If you need live pressure values, use a transmitter, not a switch.
Definition of Analog vs. Digital in Control Systems
Analog pressure switches provide continuous or stepped electrical signals, such as 4–20 mA or 0–10 V outputs. They’re used in systems that need variable monitoring, like pressure graphs or real-time feedback. Digital pressure switches, by contrast, provide precise ON/OFF signals or communicate via protocols like IO-Link. They also include features like programmable setpoints, displays, and diagnostics. While analog systems offer smooth control, digital systems provide smarter integration and easier calibration. In automation, digital pressure switches are becoming more popular due to their ability to link with PLCs and cloud-based monitoring. The choice depends on the need for signal type, complexity, and level of control required.
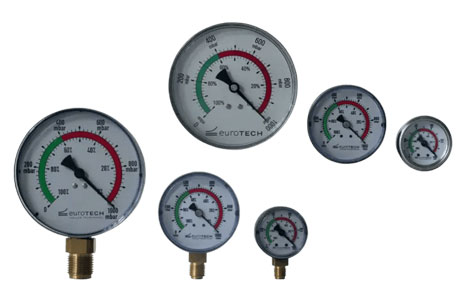
Legacy Analog Switches with Simple ON/OFF
Let’s walk back in time for a second. Imagine the early pressure control setups on pumps or compressors. What did they use? Mechanical pressure switches.
These devices were robust and built to last. Inside, there’s usually a diaphragm or a piston. When the pressure rises, it physically moves a contact and closes (or opens) a circuit. That’s it. It’s purely mechanical, no fancy electronics.
Even though we often refer to them as “analog” in casual talk, these are actually binary in action. They give a simple ON or OFF signal based on a setpoint. But because they operate in a continuous pressure range, some people still loosely group them under analog.
The beauty of these legacy switches is their simplicity. No power supply needed. No configuration hassles. You set your cut-in and cut-out pressures using a dial or screw and walk away. Ideal for rural pump systems, air compressors, and basic automation where ruggedness matters more than fancy features.
However, these types are not programmable. And they don’t provide feedback or diagnostics. You won’t know if the switch is healthy unless you physically test it or if the system fails.
Still, they’ve served the industry for decades – and you’ll still find them working in dusty corners of factories and farms. They’re affordable, easy to install, and for many basic tasks – more than enough.
Modern Digital Switches with Displays and IO-Link
Now, welcome to the future.
Modern digital pressure switches have changed the game. These aren’t just ON/OFF devices. They come with bright displays, programmable logic, and sometimes even IO-Link communication. That’s like turning your pressure switch into a smart sensor.
Let’s say you’re setting up a machine that runs on compressed air. With a digital switch, you don’t just know whether the pressure is high enough – you know exactly how high. You get real-time feedback. That’s invaluable when you’re troubleshooting or fine-tuning.
The onboard display allows for easy setup. You can adjust switching points, hysteresis, and even delay times without opening the control panel. Some models allow password protection to avoid unauthorized changes.
And if you connect via IO-Link? Now we’re talking remote configuration, real-time diagnostics, and error monitoring – all from your PLC or HMI. That saves time and adds a layer of predictive maintenance.
Also, these digital switches are compact and rugged. They’re built for industrial environments with IP65 or IP67 ratings.
Output Signal Format Comparison
Let’s compare the signals – because that’s where the real difference between analog and digital pressure switches becomes obvious.
Analog pressure switches (or transmitters) give out a continuous signal. For example, a 4-20mA signal that represents 0 to 100 PSI. If you’re getting 12mA, that means pressure is at 50 PSI. This signal can be monitored by PLCs, controllers, or indicators in real-time.
Digital switches, however, give a discrete output. It’s either ON or OFF. Like a relay closing at 80 PSI and opening back at 60 PSI. Some digital switches now offer PNP or NPN outputs, which are compatible with most industrial controllers.
If the switch supports IO-Link, it can deliver digital data over a standard 3-wire connection. That includes not just the switching status, but actual pressure values, error codes, and health status.
When selecting your switch, the signal type should match your control system. If your PLC expects a 4-20mA input, a digital switch won’t help. Likewise, if you just want to trip an alarm when pressure drops, a simple digital switch will do.
So, think of it like this: analog is smooth and descriptive, digital is sharp and decisive.
When to Use Analog and When to Go Digital
Here’s the golden question, right? When do you use analog, and when do you go with digital?
Let’s keep it simple:
Use analog pressure transmitters when you need to monitor exact pressure levels continuously. Ideal for processes that require precision – like dosing systems, HVAC control, or pump monitoring. They integrate beautifully with PID controllers and SCADA systems.
Go digital when your system needs threshold detection – like triggering a pump when pressure drops, or shutting off a system when it exceeds a limit. Especially when you want compact form, programmable switching, and status visibility.
Here’s a practical tip: if your panel has limited I/O and you just want ON/OFF switching, digital is easier. If your PLC or controller supports analog signals and you need more detailed data, go analog.
Another factor? Budget. Analog transmitters are generally costlier than basic switches, but they give much richer information. On the flip side, modern digital switches with IO-Link are also catching up in cost – but they bring smart diagnostics.
Remember, in many systems, both coexist. A transmitter for feedback and a switch for alarms.
Conclusion
A common debate is whether to choose analog or digital pressure switches. The truth is—it depends on your application. Analog switches are straightforward and cost-effective, offering basic ON/OFF signals. They’re great for standalone equipment like water pumps or compressors. Digital pressure switches, on the other hand, provide advanced functionality like precise setpoint tuning, real-time displays, and communication protocols like IO-Link. These are ideal for smart factories and industrial automation setups where integration and diagnostics matter. Both types are valuable depending on the need. If you’re controlling a simple motor, analog may suffice. If you’re collecting data or managing a smart process line, digital is the way to go. The goal is not to pick one over the other but to match the technology with your system goals. Evaluate what matters most—simplicity, accuracy, flexibility—and choose accordingly. Use what works best, not what’s trending.