Key Takeaway
Common problems with pressure gauges include:
Zero error: Gauge doesn’t return to zero
Pointer sticking: Often caused by vibration, dust, or mechanical damage
Overpressure damage: Permanent deformation of the pressure element
Corrosion or clogging: Caused by aggressive media or dirty systems
Leaks: From loose fittings or damaged seals
Fatigue: Wear and tear of internal components over time
Wrong pressure range: Using a gauge not suited for the pressure it measures
Regular inspection and proper gauge selection for the fluid, temperature, and environment can prevent most issues and extend gauge life.
Sticking or Jumping Pointer Needle
A pointer needle that sticks, jumps, or hesitates while moving is a classic symptom of internal damage or friction inside a pressure gauge. This can result from mechanical wear, dried-out lubricants, or dirt inside the movement.
Vibration is another major cause — especially in compressors and pumps. The solution? Use glycerin- or silicon-filled gauges, which dampen vibration and prevent needle flutter.
A jumping needle is more than a visual annoyance — it leads to misreadings and poor decision-making. Always replace or service gauges that don’t move smoothly, even if they still “look fine.”
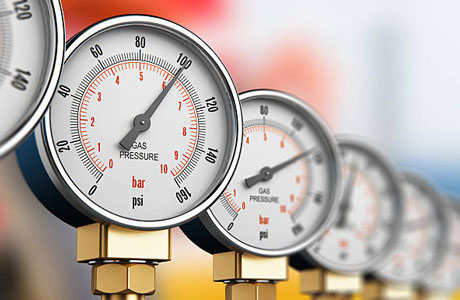
Cracked or Fogged Dial Lens
A cracked or fogged dial lens may seem cosmetic, but it affects readability and can signal deeper issues.
Fogging usually indicates moisture inside the case — caused by poor sealing, temperature swings, or outdoor exposure. This can corrode internal parts.
Cracking might result from UV exposure, physical impact, or chemical attack. It compromises the gauge’s IP rating and allows dirt or moisture to enter.
In clean rooms or food plants, even minor damage is unacceptable. Replace damaged lenses promptly and use liquid-filled or IP-rated gauges in harsh environments.
Zero Drift and Calibration Loss
Zero drift occurs when a gauge’s pointer no longer returns to zero after venting the system. It often results from:
Mechanical fatigue (Bourdon tube distortion)
Temperature effects
Vibration or overpressure exposure
Calibration loss means the gauge no longer maintains its original accuracy across the full scale. Over time, internal wear, corrosion, or stress changes the gauge’s linearity.
Symptoms include:
Readings slowly becoming inaccurate
Zero offset that worsens over time
Inconsistent response under repeat pressure cycles
Recalibrate regularly based on industry standards or install gauges with better stability and over-range protection.
Fluid Leakage or Blockage
Leaks or blockages can severely affect gauge performance:
Leaks cause pressure drop and unsafe readings
Blockages (e.g., from slurry, rust) cause false high pressure or delayed response
Prevention:
Use isolation valves and snubbers
Install chemical seals for sticky or corrosive media
Inspect connections and fittings regularly
If a gauge shows erratic or frozen readings, check for line blockage or leaks before assuming internal failure. Timely intervention prevents process disruption and equipment damage.
Loose Mounting or Vibration Damage
One of the most overlooked causes of pressure gauge failure is loose mounting and vibration.
If a gauge is:
Not tightly secured
Installed without proper brackets
Directly exposed to engine or pump vibration
…it can develop needle flutter, cracked lenses, or damaged internals.
Prevention tips:
Use vibration-dampening mounts
Choose liquid-filled models
Add snubbers or pulsation dampers
Remote-mount with a capillary tube if needed
During installation, always use the wrench on the gauge hex — never twist the case. Tighten to spec, and use thread sealant properly. A securely mounted gauge lives longer, reads truer, and resists the rigors of industrial use.
Conclusion
Common problems like pointer jitter, cracked lenses, leaking seals, and zero shift often appear before a gauge fully fails. Identifying these signs early can prevent unplanned shutdowns, process deviations, or accidents. Technicians should include visual gauge checks in daily routines—looking for fogged dials, incorrect range, or fluctuating readings. If detected early, many issues can be resolved through cleaning, reseating, or recalibration—without needing a full replacement. In critical systems, failure to detect a faulty gauge may result in pressure overload, product loss, or safety violations. Like any frontline device, pressure gauges speak through symptoms. Listen to them early, and you save far more than just the gauge.