Key Takeaway
Pressure gauge failures are often caused by:
Overpressure: Applying pressure beyond the gauge’s limit can deform the sensing element.
Vibration: Causes mechanical wear, pointer flutter, and gear misalignment.
Pulsation: Rapid pressure fluctuations fatigue the movement mechanism.
Corrosion: Aggressive fluids degrade materials over time.
Temperature extremes: Thermal expansion or contraction affects accuracy.
Improper installation: Misalignment, overtightening, or incorrect orientation.
Lack of maintenance: Dust, rust, or clogging may cause sticking or zero error.
Using liquid-filled gauges, proper range selection, material compatibility, and regular calibration help reduce failure risks and improve longevity.
Overpressure or Shock Loading
Pressure gauges are designed for a maximum limit. If the system pressure exceeds that limit — even briefly — it causes overpressure. This can lead to:
Permanent deformation of the sensing element
Loss of calibration
Needle stuck above the full-scale range
Shock loading happens when pressure spikes suddenly (like water hammer or valve slamming). To prevent damage, use gauges with a 130% overpressure safety margin or add snubbers and pulsation dampeners.
A gauge that’s been overpressured once may never read accurately again — even if the needle “seems” to return to normal.
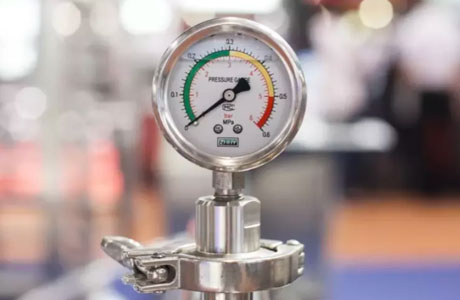
Exposure to Corrosive Media or Moisture
Exposure to corrosive fluids or humidity can severely damage a pressure gauge’s internal components. The Bourdon tube, gear mechanism, and even the case can rust, clog, or crack.
Use the right materials:
316 Stainless Steel for general corrosion resistance
Monel or Hastelloy for acids and chlorides
Teflon coating or chemical seals for aggressive media
Moisture from cleaning, condensation, or outdoor use also causes fogging and internal rust. Use gauges with IP65+ protection, filled cases, and drain plugs where needed. Preventing exposure is cheaper than frequent replacement.
Mechanical Vibration or Pulsation Effects
Constant vibration causes:
Pointer oscillation
Wear in gear linkages
Internal component fatigue
Pulsation (e.g., from reciprocating pumps) causes:
Rapid needle fluctuations
Fatigue-induced failure
Gauge case rupture
Solutions:
Liquid-filled gauges (glycerin or silicone dampens movement)
Snubbers or restrictors to smooth pressure spikes
Remote mountings using capillary tubing to remove the gauge from vibration sources
Preventative installation protects gauges from false readings and early breakdown.
Poor Installation Practices
Common mistakes include:
Mounting directly on vibrating equipment
Using the wrong thread sealant (e.g., tape entering the gauge)
Installing gauges upside-down or without support
Skipping snubbers in pulsating systems
Poor installation leads to:
Leaks
Premature wear
Calibration drift
Unsafe conditions
Best practices:
Use dampers or remote mounts
Support heavy gauges
Position for easy viewing
Label ranges and units clearly
Proper installation protects the gauge and improves operational safety.
Lack of Maintenance or Calibration
A gauge is only as good as the attention it receives. Lack of maintenance is one of the top reasons for failure and inaccurate readings.
Common consequences:
Zero drift
Inconsistent needle movement
Blocked ports from debris
Leaks or fluid loss in filled models
Many facilities install gauges and forget them. But regular inspection, zero checks, and calibration are essential to long-term performance.
Best practices:
Monthly visual inspections
Bi-annual zero checks
Annual calibration (or more for critical systems)
Document everything for traceability
A “set it and forget it” mindset with gauges is dangerous — pressure is too critical to be left unverified.
Conclusion
Most pressure gauge failures can be traced back to a few common causes—overpressure, vibration, temperature extremes, or corrosion. Once a gauge fails, don’t just replace it—investigate why. Was the media too aggressive for the material? Did pulsation from a pump stress the element? Was the mounting prone to vibration or movement? Addressing root causes—such as adding a snubber, using isolators, or selecting more compatible materials—prevents repeated failure. Gauge damage not only affects readings but can also compromise safety and compliance. Learning from failures is part of smarter maintenance. Fix the environment, not just the gauge, and your instruments will last longer and perform better.