Key Takeaway
A Bourdon tube pressure gauge is the most widely used type of mechanical pressure gauge. It consists of a curved, hollow metal tube (typically C-shaped) that straightens when internal pressure increases. This motion is linked to a gear and pointer mechanism that displays the pressure on a dial. Bourdon tubes are highly durable, simple in design, and capable of measuring pressures from vacuum to several thousand psi. They are suitable for liquids, gases, and steam and are used in applications like hydraulic systems, compressors, and industrial machinery. Their robust construction makes them reliable for both high and low-pressure measurements.
The History and Design of Bourdon Tubes
The Bourdon tube was invented in 1849 by Eugène Bourdon, a French engineer. Over 170 years later, it’s still the most used mechanical pressure sensor in the world. Why? Because it’s brilliantly simple.
It uses a curved, hollow tube that straightens under pressure. That motion drives a gear which moves the needle. No electricity. No software. Just pure mechanics.
Modern Bourdon tubes are made of stainless steel, phosphor bronze, or Inconel. Some have C-shapes, others are helical for higher pressures. The design has evolved, but the principle remains the same.
Bourdon tubes are proof that the best engineering solutions don’t always need complexity — just clarity of thought and precision in design.
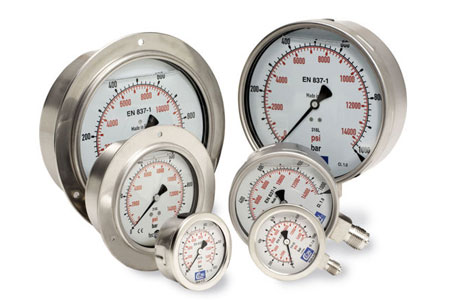
How the Curved Tube Responds to Pressure
The Bourdon tube is curved like a “C” or spiral. When pressure is introduced inside the hollow tube, the inner side experiences more force than the outer. This causes the tube to attempt straightening.
This movement is tiny — often less than a few millimeters — but it’s enough to turn a gear and rotate the pointer on the dial. The tube’s material, thickness, and curvature all affect how much it bends and how accurate the gauge is.
Excessive pressure may overstretch the tube, resulting in permanent deformation. That’s why pressure gauges must be selected carefully to match system pressure with sufficient safety margin.
Industries Where Bourdon Gauges Are Widely Used
Bourdon tube gauges are popular across many industries due to their simplicity and robustness:
Oil & Gas: For wellhead, pipeline, and pump monitoring
Manufacturing: Compressors, stamping machines, hydraulic presses
Water Treatment: Booster pumps and filtration units
Automotive: Brake, fuel, and tire pressure systems
Marine and Offshore: For tank and engine room pressure
They are favored where power isn’t available, and instant pressure feedback is essential. Their durability and no-power operation make them a go-to for rugged, on-site conditions.
Advantages: Rugged, Cost-Effective, Reliable
Mechanical pressure gauges offer key advantages:
Rugged: Withstand dirt, shock, and temperature swings
Cost-effective: Inexpensive to purchase and maintain
Reliable: No power needed, minimal failure points
Simple: Easy to read and install
For these reasons, they’re widely used in:
Workshops
Construction
Utility plants
Agriculture
Backup to digital systems
Their simplicity is their strength. With proper care, they deliver years of dependable performance at a fraction of the cost of complex sensors.
Limitations and Accuracy Considerations
Mechanical pressure gauges have clear limitations despite their widespread use.
1. Accuracy Limits: Most analog gauges have ±1% to ±3% full-scale accuracy. This might be too imprecise for laboratory or critical process applications.
2. No Data Logging: Analog gauges cannot record trends, alarms, or fluctuations unless monitored continuously by an operator.
3. Environmental Sensitivity: Vibration, high temperature, and humidity can affect mechanical components, causing wear or drift.
4. Limited Readability: In low light or dusty environments, dial visibility becomes a challenge.
5. Lack of Remote Monitoring: Gauges provide only local display, limiting their use in modern SCADA/IoT-based systems.
However, for many systems where readings are infrequent, cost is a concern, and power isn’t available, they are still the go-to choice.
To overcome these limitations:
Use digital or smart gauges where accuracy and data logging are needed.
Calibrate frequently.
Protect gauges from environmental damage using dampers, enclosures, or liquid-filling.
Knowing their limits allows better integration of gauges into broader system design.
Conclusion
Bourdon tube pressure gauges are the most widely used mechanical pressure gauge due to their simplicity, durability, and reliability. They function by converting pressure into a mechanical deflection, where a curved tube straightens as pressure increases. This movement is then transmitted to a pointer that shows the pressure reading on a dial. These gauges are cost-effective and perform well in medium to high-pressure ranges. They are suitable for liquids and gases, making them a favorite in industries like manufacturing, HVAC, oil and gas, and water treatment. They don’t require power and can withstand rough handling. Their robustness, long service life, and accurate readings make them a trusted choice worldwide.