Key Takeaway
Cut-in pressure is the point where the pressure switch turns ON the connected equipment, like a pump or compressor. Cut-out pressure is the point where it turns OFF the equipment. These two settings help maintain the right pressure in a system. For example, in a water pump setup with a 30/50 psi switch, the pump turns ON at 30 psi (cut-in) and OFF at 50 psi (cut-out). The difference between the two is called the pressure differential. This gap prevents the system from turning ON and OFF too frequently. You can usually adjust both values by turning screws inside the pressure switch. The wider the gap, the less often your system runs. Setting it too narrow may cause short cycling, which can wear out your system faster. Always stay within the manufacturer’s safe range. Proper cut-in and cut-out settings keep your system balanced, energy-efficient, and working smoothly.
What is Cut-In Pressure?
Cut-in pressure is the lower threshold at which a pressure switch activates to start a system—commonly a pump or compressor. When pressure in the system drops below this point, the switch closes the circuit, powering up the connected device. For example, in a water pump system with a 30–50 PSI switch, the pump starts when pressure drops to 30 PSI. Correctly setting the cut-in point ensures that your system doesn’t run dry or lag in response. Too low, and you may cause pump strain; too high, and pressure may fluctuate excessively. Always balance cut-in with cut-out pressure to avoid short cycling and ensure stable, efficient operation.
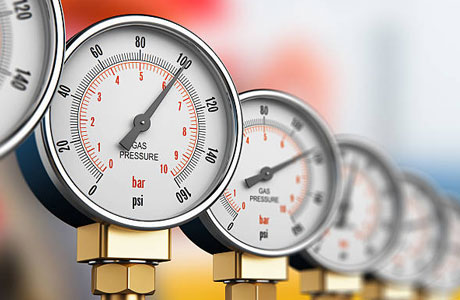
What is Cut-Out Pressure?
If cut-in pressure is the start signal, cut-out pressure is the stop.
Cut-out pressure is the maximum pressure at which the pressure switch deactivates the pump or compressor. It signals, “We’ve hit the upper limit. Shut down.”
Let’s go back to the same water pump example. Once the pump is running and pressure climbs, you don’t want it to keep running forever. That would waste energy, over-pressurize your pipelines, and damage components.
So, the cut-out pressure kicks in. Typically, this might be set at 4.0 bar for a residential system. Once the pressure touches this limit, the switch opens the circuit, and the pump stops.
This setting protects the system. It ensures the pump only works as long as needed. No more, no less.
Also, too high of a cut-out pressure can stress components. Too low, and you might see poor performance. So finding the sweet spot is important.
How to Set the Difference (Pressure Band)
The pressure band or differential is the gap between the cut-in and cut-out pressure settings. This difference defines how long your pump runs before switching off, and how long it stays off before switching back on.
Here’s how it works:
If your cut-in is 2.0 bar and your cut-out is 4.0 bar, the pressure band is 2.0 bar.
This means the pump will kick in at 2.0 bar and stop at 4.0 bar.
Now, how do you set it?
Most mechanical pressure switches have one main nut or spring to set the cut-in pressure. A second adjustment (usually smaller) sets the differential. Digital pressure switches allow exact inputs via menus.
Why does the band matter?
Because it controls how often the pump starts and stops. If the band is too narrow (e.g., cut-in 3.8 bar, cut-out 4.0 bar), your system will cycle rapidly. That’s not good.
But if the band is too wide (e.g., cut-in 1.0 bar, cut-out 5.0 bar), then pressure will fluctuate more than desirable. You’ll get strong bursts, then weak flow. Not good either.
Ideal range: For water pumps, a differential of 1.5 to 2.0 bar is common. For air compressors, 1.0 to 1.5 bar works well. Golden Rule: Always balance responsiveness and system longevity.
Why This Gap Prevents Short Cycling
Short cycling is one of the silent killers in any pressure-based system. It happens when the pump or compressor starts and stops too often in a short period. The culprit? An improperly set pressure band.
Here’s why:
When your cut-in and cut-out points are too close, the switch activates and deactivates repeatedly. The system never gets time to breathe.
Short cycling leads to:
Higher wear and tear on pumps
Motor overheating
Reduced efficiency
Higher power bills
Let me give you an example from the field.
In a packaging plant I worked at, we had a booster pump cycling every 30 seconds. Why? The technician had mistakenly set the cut-in at 3.9 bar and the cut-out at 4.0 bar. The pressure band was too narrow. Within weeks, the motor capacitor failed, and the pump was worn out.
We fixed it by setting a 2-bar differential. The result? Smooth operation and zero issues for months.
Rule of Thumb: A wider pressure gap = fewer cycles = longer life.
So, always double-check your settings. It’s not just a number. It’s the health of your system.
Typical Values for Pumps and Compressors
Now that you know what cut-in and cut-out pressures do, let’s talk about real-world numbers.
These values change based on what system you’re dealing with:
For Water Pumps (Domestic or Booster):
Cut-in Pressure: 1.5 to 2.0 bar
Cut-out Pressure: 3.5 to 4.0 bar
Differential: 1.5 to 2.0 bar
This range ensures consistent water flow and avoids dry taps. It also helps save electricity and prevent water hammering.
For Air Compressors (Workshop or Industrial):
Cut-in Pressure: 6.0 to 7.0 bar
Cut-out Pressure: 8.0 to 9.0 bar
Differential: 1.5 to 2.0 bar
Why higher values? Pneumatic tools need higher and more consistent pressures. A wider band prevents frequent restarts and helps regulate airflow better.
For Pressure Tanks:
Always match cut-in and cut-out with tank pressure limits
Tank pre-charge should be 1.0 to 1.5 bar below cut-in
Conclusion
Cut-in and cut-out pressures define when your pressure switch activates or deactivates. Set the cut-in too low, and your system starts too early. Set the cut-out too high, and you risk overpressure. The space between the two is the differential or pressure band, which prevents short cycling and protects motors. A well-balanced setting ensures smoother operation, longer equipment life, and fewer energy spikes. For example, a 30–50 PSI setting means the pump starts at 30 and stops at 50. Always test settings under real load conditions, and use a gauge to verify them. Small tweaks to this balance make a big difference in performance, safety, and operational cost. Don’t overlook it.