Key Takeaway
A pressure switch and a limit switch both control systems, but they sense different things. A pressure switch works based on fluid or air pressure. When pressure rises or drops past a certain point, it opens or closes a circuit. It’s used in pumps, compressors, and HVAC systems. A limit switch, however, works based on physical movement. It detects the position of an object — like a machine part reaching a certain point. For example, in a conveyor, a limit switch stops the belt when an object reaches the end. So, pressure switches detect invisible pressure, and limit switches detect mechanical contact or movement. Both are safety or control devices, but for different types of monitoring. Pressure switches are common in plumbing and air systems, while limit switches are used in manufacturing, elevators, and mechanical setups. Choosing the right one depends on whether you want to monitor pressure or position.
Input Source – Pressure vs. Mechanical Motion
Pressure switches and limit switches serve different purposes based on the input type they respond to. A pressure switch activates based on fluid or gas pressure, while a limit switch reacts to physical movement—like a door closing or an object reaching the end of a track. Internally, pressure switches use diaphragms or pistons, while limit switches use levers or plungers. Confusing the two may result in incorrect system behavior or unsafe operation. In hydraulic systems, pressure switches ensure safe pressure levels. In conveyor systems, limit switches detect part position. When choosing a switch, always ask: “What triggers it—pressure or movement?” Knowing this difference is essential for proper integration and reliable automation.
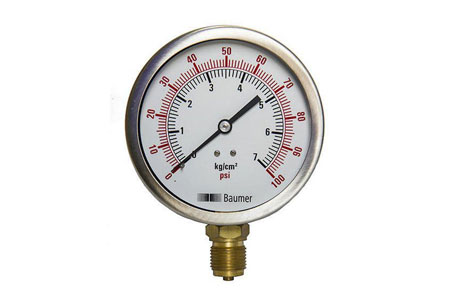
Internal Mechanism and Sensor Design
A pressure switch contains a diaphragm or a piston that reacts to pressure changes. When the pressure reaches a threshold, it moves, triggering an internal contact to either open or close. Some are analog, while modern ones offer digital outputs with more precision.
A limit switch, in contrast, is more straightforward. It’s almost like a button. Inside, it has mechanical components like levers, rollers, or plungers. Once something physically touches or displaces them, it makes or breaks the electrical connection.
Think of it this way: pressure switches feel; limit switches get poked.
Hook: “Imagine giving your machine eyes to see vs. skin to feel – that’s how different these switches are.”
This also affects durability. Pressure switches often need sealing against oil or air leaks. Limit switches need to withstand mechanical wear from repeated hits.
Wiring and Control System Integration
A pressure switch usually integrates with analog or digital control systems. It may offer SPDT (Single Pole Double Throw) or DPDT (Double Pole Double Throw) contact types, and some models provide 4-20mA outputs for PLC input.
Limit switches, on the other hand, are often part of safety or position control loops. They send simple ON/OFF signals when a machine part reaches a specific position. They’re common in conveyor systems, packaging machines, and robotics.
Wiring-wise, limit switches tend to be dry-contact (voltage-free) and can be easily interfaced with relays or PLC digital inputs.
Applications in Hydraulic vs. Motion Systems
Now, where do these switches shine?
Pressure switches are built for fluid environments. You’ll find them in:
Hydraulic presses
Air compressors
Pump control systems
HVAC chillers
Water booster pumps
Whenever you need to cut off a pump or activate an alarm based on fluid pressure, this is your guy.
Limit switches dominate in mechanical motion applications:
CNC machines
Robotic arms
Elevators and hoists
Door position detection
Conveyor belt control
Any system that needs to know if something reached a limit (hence the name), relies on limit switches.
Troubleshooting Tips for Both Switches
When things go wrong, knowing your switch helps fix problems faster.
For pressure switches, start by checking:
Is the pressure range correct?
Are there leaks in the system?
Is the diaphragm worn out?
Is it wired properly to the control unit?
Use a pressure gauge to compare actual system pressure with the switch setpoint.
For limit switches, inspect:
Has the actuator arm or plunger worn out?
Is the moving part properly aligned?
Are the mechanical contacts stuck?
Are wires loose or corroded?
Conclusion
Pressure switches and limit switches might sound similar, but they respond to completely different physical inputs. A pressure switch reacts to fluid or gas pressure, while a limit switch detects mechanical movement—like a door opening or an actuator reaching its end. Confusing the two can lead to incorrect installations and system failures. Pressure switches belong in pipelines, tanks, compressors, and HVAC systems. Limit switches are used in machine tools, conveyor systems, and safety doors. Internally, their mechanisms are different—pressure switches rely on diaphragms and springs, while limit switches use levers or plungers. Even their wiring terminals and mounting styles differ. When selecting a switch, always ask: “What input is being sensed?” That simple question ensures you’re using the correct device for the job. Matching the right switch to the right stimulus guarantees better performance, safety, and integration into your control system.