Key Takeaway
The pressure element in a gauge is the core component that directly responds to the applied pressure. Its function is to convert pressure energy into mechanical motion or an electrical signal. In mechanical gauges, elements like Bourdon tubes, diaphragms, bellows, or capsules deform under pressure, and this deformation moves a pointer to display the pressure value. In digital gauges, the pressure element may be a strain gauge or piezoelectric sensor that produces an electrical output proportional to the pressure. The material and design of the pressure element are selected based on the type of fluid, pressure range, temperature, and required accuracy for the application.
Definition and Types of Pressure Elements
Pressure elements are the parts inside a gauge or sensor that react to applied pressure. Main types include:
Bourdon Tube: C-shaped metal tube for medium-high pressure
Diaphragm: Thin metal disk for low pressure or corrosive fluids
Capsule: Two diaphragms welded together, used in low pressure gas
Bellows: Accordion-shaped metal for moderate ranges and compact designs
Each has its application. Choose based on pressure range, medium compatibility, and response speed. Understanding these elements helps you choose the right gauge — not just any gauge.
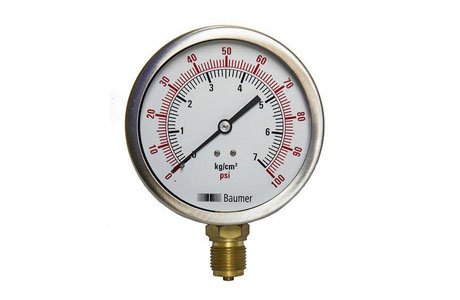
How Pressure Is Converted into Mechanical Displacement
In pressure gauges, pressure acts as a force over area — deforming an element (like a tube or diaphragm). This deformation is mechanical displacement.
In Bourdon tubes, the curved tube straightens
In diaphragms, the disc flexes
In bellows, the concertina compresses
This small movement is transferred to gears, amplified, and shown as pointer movement. The design must be sensitive enough to detect minute pressure changes but rigid enough to return to zero without drift.
This mechanical conversion is at the heart of analog pressure instrumentation. If it fails — due to fatigue, corrosion, or shock — readings become unreliable.
Bourdon Tube, Diaphragm, and Bellows Elements
These are the core mechanical pressure sensing elements:
Bourdon Tube: Curved tube that straightens under pressure. Best for high-pressure applications. Simple and durable.
Diaphragm: Thin flexible disc deflects with pressure. Ideal for low pressure or corrosive/viscous media.
Bellows: Accordion-style chamber expands/contracts. Used for small pressure changes or differential readings.
Each has trade-offs:
Bourdon = wide range, rugged
Diaphragm = chemical and sanitary-friendly
Bellows = sensitive, low-pressure accuracy
Choosing the right element ensures the gauge performs as expected across its life span.
Importance of Material and Shape Selection
The material and shape of sensing elements (Bourdon tube, diaphragm, etc.) determine:
Pressure rating
Corrosion resistance
Fatigue life
Accuracy and repeatability
Materials:
Brass: Low cost, water & air systems
316L SS: Corrosive or sanitary systems
Monel, Hastelloy: High chemical resistance
Shapes:
C-shaped Bourdon tubes: Most common, good for moderate pressures
Spiral tubes: Used in high-pressure gauges
Flat diaphragms: Best for low pressure and sanitary service
Matching material and shape to the process environment improves durability and measurement consistency.
Calibration Dependence on Pressure Element Integrity
The core of any mechanical pressure gauge is its pressure-sensing element — usually a Bourdon tube or diaphragm. Calibration is only effective if this element remains intact and responsive.
If the tube becomes:
Fatigued (from cycling)
Deformed (from overpressure)
Corroded (from chemical exposure)
…then no amount of recalibration will restore accuracy. The response curve becomes nonlinear or unrepeatable.
Signs of integrity loss:
Needle doesn’t return to zero
Inconsistent readings across range
Lag in needle movement
In such cases, replace the gauge instead of recalibrating. Calibration is only as good as the component it’s correcting. Regular inspection ensures calibration isn’t wasted on compromised internals.
Conclusion
Whether it’s a Bourdon tube, diaphragm, or bellows, the pressure-sensing element is what translates force into motion or electrical signal. If this element fails, the entire gauge becomes unreliable. That’s why selecting the right material (stainless steel, bronze, Inconel) for the pressure element is essential for media compatibility and environmental durability. Each element type responds differently—diaphragms for low pressure and corrosion resistance, Bourdon tubes for general industrial use. Regular calibration and proper installation protect this critical part from fatigue, overpressure, or vibration damage. When well-chosen and maintained, the pressure element provides the foundation for trustworthy, long-term readings in any system.