Key Takeaway
Hooke’s Law states that the force needed to extend or compress a spring is directly proportional to the distance it is stretched or compressed, i.e., F = kx. In pressure gauges, this principle is applied through elastic elements like Bourdon tubes, diaphragms, or bellows. As pressure increases, it exerts force on these components, causing deformation. The degree of deformation is proportional to the applied pressure. This displacement is then translated into a dial reading. Hooke’s Law ensures linearity in many mechanical pressure gauges. However, for accurate measurements, the material must operate within its elastic limit, as permanent deformation will cause gauge errors.
Definition of Hooke’s Law in Elastic Elements
Hooke’s Law is a principle every instrumentation engineer must understand — especially when working with Bourdon tubes, diaphragms, and bellows. It states that the force (or pressure) applied to an elastic material is directly proportional to the amount it deforms, as long as the elastic limit is not exceeded.
Mathematically: F = k × x
Where F is the force, x is the displacement, and k is the stiffness constant.
In pressure gauges, this law governs how much the elastic element (like a C-tube or diaphragm) moves when pressure is applied. The mechanical deflection causes movement in the pointer mechanism — translating pressure into a readable dial output.
Exceeding the elastic limit — through overpressure or fatigue — causes permanent deformation, and that’s when gauges start giving faulty readings. Always select a gauge with a range that includes a safety margin to stay within Hooke’s Law boundaries.
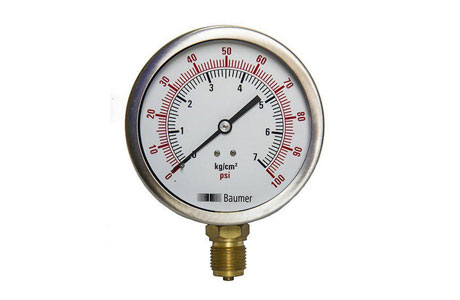
Role in Bourdon Tube and Diaphragm Gauges
Both Bourdon tube and diaphragm gauges rely on elastic deformation — but in different ways.
Bourdon Tube: A curved hollow tube that straightens as pressure increases.
Diaphragm Gauge: A thin, flexible disk that bulges outward when pressure is applied.
Bourdon tubes are suitable for medium-to-high pressures. They’re used in compressors, boilers, and hydraulic systems. Diaphragms, on the other hand, excel in low-pressure applications and are better for corrosive or viscous fluids because the sensing element is isolated.
Knowing which one to use depends on pressure range, fluid type, mounting constraints, and cost. In both cases, the movement must stay within elastic limits to ensure repeatability and accuracy.
Mathematical Expression: F = -kx
This formula — Hooke’s Law — explains how elastic elements behave under pressure:
F = -kx,
where:
F = Force applied (from pressure)
k = Spring constant of the material
x = Displacement or deformation
This is the principle behind Bourdon tubes and diaphragms. When pressure increases, force increases proportionally, causing more deflection. The system must stay within the elastic limit to return to zero and remain accurate.
If the pressure exceeds the elastic range, permanent deformation occurs. This leads to zero error and non-linearity in readings. That’s why overrange protection is critical for pressure gauges.
Limitations in Real-Life Pressure Measurement
In real-world conditions, perfect pressure measurement is nearly impossible due to:
Mechanical wear
Thermal expansion
Parallax or zero error
Signal interference (for digital sensors)
Fluctuating process conditions
No gauge remains 100% accurate forever. That’s why industry standards specify acceptable tolerances, such as ±1% or ±1.6% FS.
Understanding these limitations helps set realistic expectations. Always choose instruments that exceed the precision needed for your process — not just the cheapest or easiest to install.
Engineering Importance of Elasticity in Gauges
The heart of most mechanical pressure gauges lies in their ability to deform — specifically, their elasticity. This is most evident in the Bourdon tube, a curved, hollow metallic component that flexes under pressure. The amount it bends is proportional to the internal pressure, and this movement is translated into the dial reading.
The gauge’s accuracy depends heavily on the material’s elastic properties. Common materials include brass, phosphor bronze, or stainless steel — chosen for their consistent and recoverable deformation under load. If the material loses elasticity due to fatigue, corrosion, or overheating, the readings become unreliable.
Elasticity also determines how well a gauge handles pressure cycles. In applications with frequent fluctuations, poor elasticity can lead to permanent deformation (plasticity), causing zero drift or sticking needles.
Engineers must consider temperature, chemical exposure, and expected pressure range when selecting a gauge. High elasticity and fatigue resistance are key in ensuring the pressure element can return to its original shape repeatedly without distortion.
Conclusion
Most mechanical pressure gauges operate using Hooke’s Law, which states that the force needed to compress or extend a spring is proportional to the distance stretched. In a Bourdon tube or diaphragm gauge, pressure causes elastic deformation, which is then translated into dial movement. This principle allows gauges to provide repeatable and reliable readings. However, elasticity has limits—overpressure or long-term use can lead to permanent deformation, throwing off measurements. Understanding Hooke’s Law helps technicians diagnose whether a gauge is functioning correctly or has suffered fatigue. It also explains why materials and design matter in gauge construction. At its core, Hooke’s Law makes pressure measurement both possible and practical in the physical world.