Key Takeaway
Pressure gauge calibration is essential for maintaining measurement accuracy and ensuring safety in pressurized systems. Over time, gauges can drift due to mechanical wear, vibration, or environmental factors, resulting in incorrect readings. Calibration helps detect these deviations and restore accuracy. In regulated industries like pharmaceuticals, aerospace, and energy, calibration is mandatory to meet compliance standards. Accurate gauges reduce the risk of equipment damage, product defects, or safety incidents caused by overpressure. Regular calibration also improves process efficiency and extends the life of both gauges and connected systems. It’s a key component of any quality assurance or maintenance program.
Ensures Accuracy and Reliability in Measurements
A properly calibrated and maintained pressure gauge ensures your system runs within safe and efficient limits. Faulty readings lead to wrong decisions — wrong pressure means poor product quality, increased energy consumption, or even safety failures.
Accuracy is defined by a percentage of full-scale reading (e.g., ±1.0% FS). Reliability means the gauge gives consistent readings over time.
To ensure both:
Choose the correct pressure range (not too close to the limit)
Avoid mechanical shock and overpressure
Follow periodic recalibration intervals
Instrument reliability is not luck — it’s built through discipline.
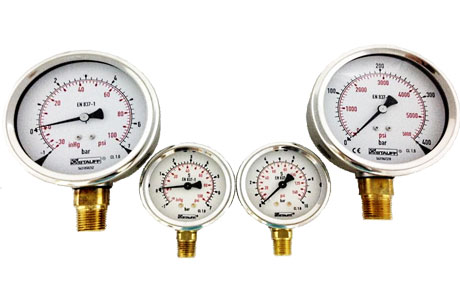
Maintains Compliance with Industry Standards
Pressure instrumentation must comply with standards — especially in regulated industries like oil & gas, pharmaceuticals, and aerospace. Common standards include:
ASME B40.100 for pressure gauges
ISO/IEC 17025 for calibration labs
EN 837 for European gauge specifications
ATEX/IECEx for explosion-proof gauges
Compliance ensures:
Safe operation under specified conditions
Reliable process control
Acceptance during audits or certifications
Non-compliance not only risks equipment failure — it can lead to legal and financial penalties. Always use pressure gauges that meet or exceed the applicable industry standard for your environment.
Detects and Prevents Hidden Instrument Errors
Pressure gauges help expose:
Stuck valves (abnormal pressure rise)
Leaks (slow pressure drop)
Pump cavitation (inconsistent suction pressure)
Blocked filters (rising differential pressure)
By strategically placing gauges across your system, you can detect issues before alarms trigger or damage occurs.
They’re silent sentinels — low cost but high impact. Train teams to watch for subtle anomalies in pressure behavior. It’s your best defense against invisible equipment errors.
Protects Equipment and Personnel from Failures
Accurate pressure readings prevent:
Overloaded pumps and compressors
Ruptured pipes or tanks
Unsafe boiler or reactor conditions
Equipment cavitation or dry running
Pressure switches can trigger alarms or emergency shutdowns. Gauges allow visual inspection and preventive maintenance decisions.
A small investment in proper pressure monitoring protects millions in equipment — and most importantly, safeguards personnel from explosions, toxic leaks, or fire hazards.
Enhances Process Control and Efficiency
Pressure gauges play a key role in enhancing process control and system efficiency.In any fluid or gas system, pressure reflects the health and performance of the process. If pressure drops, it might mean a leak, clog, or pump failure. If it spikes, it could indicate a blockage or malfunction.
With accurate pressure monitoring:
Pumps run more efficiently
Valves open/close at the right time
Compressors cycle properly
Filters are replaced at the right moment
This helps save energy, reduce wear and tear, and avoid downtime.
In automated plants, pressure readings are fed into PLCs or SCADA systems to fine-tune processes. Even in manual systems, a technician armed with real-time pressure data can make better decisions.
Ultimately, better pressure monitoring = smoother operations, less waste, and higher profitability.
Conclusion
Pressure gauges are only as reliable as their calibration. Without routine checks, readings can drift—leading to incorrect decisions, process inefficiencies, or safety risks. Calibration helps maintain the integrity of measurement over time and builds trust across departments. Technicians, quality teams, and operators must be confident that the gauge is showing the truth. Regular calibration also supports audit compliance and ISO certifications. Even slight variations in high-sensitivity environments (like pharma or aerospace) can result in batch rejection or system failure. Trusted calibration procedures include using master gauges or dead weight testers under controlled conditions. In short, calibration isn’t a one-time task—it’s a continuous process that maintains the reputation of your instruments and your operation.