Key Takeaway
The pressure gauge range refers to the minimum and maximum pressure the gauge can accurately measure. Ranges vary widely depending on the application—from vacuum pressures (-1 bar) to high-pressure systems (up to 1000 bar or more). For best performance, it’s recommended to select a gauge where the working pressure falls within 25% to 75% of its full-scale range. Using a gauge beyond its specified range can result in inaccurate readings or permanent damage. Common ranges include 0–100 psi, 0–10 bar, or 0–250 kPa. Selecting the correct range is crucial for accurate monitoring and ensuring the longevity of the gauge.
Common Ranges in PSI, Bar, and Pascal
Pressure can be measured in different units: PSI (pounds per square inch), Bar, and Pascal (Pa). Each industry prefers one depending on regional standards or application types.
1 Bar = 14.5038 PSI = 100,000 Pa
1 PSI = 6.89476 kPa
1 atm = 1.01325 Bar
In the U.S., PSI is the most commonly used unit, especially in pneumatic and hydraulic systems. In Europe and Asia, Bar is preferred. Pascal is the SI unit and is used in scientific or micro-pressure applications (e.g., cleanrooms).
Most industrial gauges come with dual markings — typically PSI and Bar — to make life easier for global engineers. When selecting a gauge, ensure the range fits your system: if your pressure is expected to reach 4 bar, choose a 6 or 10 bar gauge for safety margin.
Understanding unit conversions is not just academic — it prevents wrong installations, incorrect readings, and costly mistakes in multi-national projects.
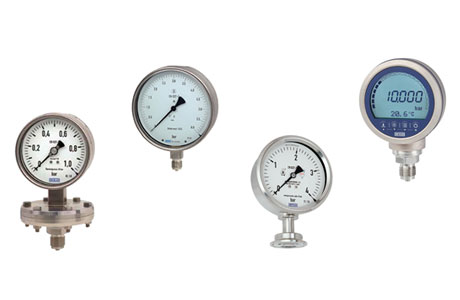
How to Select the Right Range for Your System
Always choose a gauge with a range 1.5 to 2 times your system’s maximum working pressure. Why? Because gauges must never operate near their maximum scale — this shortens lifespan and reduces accuracy.
If your system operates at 6 bar, choose a 10 bar gauge — not an 8 bar one. The working range should fall in the middle third of the scale for best accuracy.
Also consider pressure spikes. If your system sees occasional surges (like in pumps or press machines), add a buffer. Select a filled gauge or add a snubber to avoid pointer damage or permanent tube deformation.
Remember, correct range = longer life, fewer errors, and safer operation.
Over-Range Protection Mechanisms
Over-range protection prevents damage to pressure gauges when system pressure exceeds the maximum rating.
Protection methods include:
Snubbers: Reduce sudden pressure spikes
Overpressure stops: Mechanical limits that restrict pointer movement
Gauge dampeners: Fluid-filled cases absorb shock
Blowout back plates: Safely release internal pressure if the gauge fails
In critical applications, choose gauges rated at 130–150% of normal pressure. Repeated over-range events lead to elastic deformation, calibration drift, or even internal rupture.
Designing your system with built-in protection extends gauge life and ensures accurate readings under real-world conditions.
Factors Affecting Gauge Range Selection
Choosing the wrong pressure range is a common — and costly — mistake. Your gauge should operate within 30–70% of its full scale for optimal accuracy and durability.
Key factors to consider:
Normal operating pressure
Max pressure including surges
Type of fluid (compressible/incompressible)
Process dynamics (steady vs pulsating)
For example, if your system runs at 6 bar with possible surges to 9 bar, a 0–10 bar gauge is better than 0–6. Gauges running at the edge of their range wear faster, show drift, and may fail unexpectedly.
Why Too Much Range Is a Problem Too
Selecting a gauge with too wide a pressure range might seem safer — but it’s actually a mistake. Over-ranging a pressure gauge reduces accuracy in the operating zone. Most mechanical gauges are accurate to ±1–2% of full scale. If you choose a 0–1000 psi gauge for a system that runs at 50 psi, that 1% error becomes significant.
Low operating pressures will barely deflect the Bourdon tube, resulting in readings that are hard to distinguish and interpret. The pointer may not move enough to provide reliable resolution, making fine pressure adjustments difficult.
Additionally, wide-range gauges tend to have larger, more compressed scale intervals, increasing the chances of misreading — especially in low-light or high-vibration environments.
To solve this, select a gauge with a full-scale range that places your normal operating pressure in the middle third of the scale. For example, a 0–100 psi gauge is ideal for a 50 psi system. This maximizes accuracy, resolution, and readability.
Over-ranging can also wear out the sensing element prematurely if the gauge is constantly operating at the very low end of its scale. Precision, not just protection, should drive gauge selection.
Conclusion
Choosing the right pressure range for your gauge is crucial. A gauge rated too high may show barely any needle movement, leading to misreading. One rated too low can easily get damaged by minor overpressure. Ideally, select a gauge where your operating pressure falls within 25–75% of its full-scale range. This ensures accuracy and protects the sensing element. Over-range protection mechanisms like blow-out discs help, but they aren’t substitutes for proper selection. Also, be aware that lower-pressure ranges may require more sensitive materials, which can be affected by vibration or temperature. Don’t guess your range—calculate it based on system specs and operating fluctuations. The right range means safer, clearer, and more dependable readings.