Key Takeaway
The useful life of a pressure switch depends on its quality, usage, and environment. Most well-made switches can last 5 to 10 years in normal conditions. In clean environments with stable pressure, they last longer. But in harsh conditions like high vibration, extreme temperatures, moisture, or dirty air/water, the switch may fail sooner. Frequent ON/OFF cycles (called short-cycling) can also wear out internal parts like springs and contacts faster. Electrical contacts may burn or corrode over time, especially if not rated properly for the connected load. Regular inspection and cleaning can help extend the switch’s life. If you notice delayed response, failure to switch, or inaccurate performance, it might be time to replace it. While some switches are repairable, most are replaced once worn. In summary, a pressure switch lasts long with proper setup and care, but it should be checked regularly to ensure safe and reliable operation.
Life Expectancy in Switching Cycles
A pressure switch’s life expectancy is measured in the number of successful ON/OFF operations it can perform. Light-duty switches may last around 100,000 cycles, while industrial-grade versions can exceed 1 million cycles. Factors that reduce lifespan include frequent cycling, overpressure, electrical arcing, and poor installation. Signs of a worn switch include inconsistent activation, arcing sounds, or sluggish response. To maximize lifespan, select a switch that matches your system’s duty cycle, use proper voltage loads, and avoid pressure spikes. Preventive maintenance and occasional testing also help. When designing high-cycle systems, invest in a higher-rated or electronic switch to avoid unexpected downtime and maintenance costs.
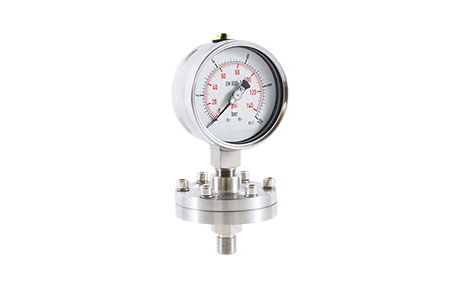
Effect of Fluid Type and Pressure Fluctuations
Not all pressure switches have the same tolerance. The type of fluid passing through or touching the diaphragm has a direct impact on the switch’s life.
If your application involves clean air or water, the switch will generally last longer. But if you’re dealing with corrosive chemicals, viscous oils, or sludgy water, expect a shorter lifespan. Why? Because these fluids cause build-up, wear, and sometimes even chemical degradation of the internal components.
Also, pressure fluctuations play a massive role. Let’s say your system pressure jumps wildly between low and high. That’s stress. Repeated, rapid ON/OFF cycles cause mechanical fatigue. Over time, the diaphragm and contact points wear out.
I’ve seen pressure switches in hydraulic presses get damaged in 6 months because the system had extreme pressure spikes—while the same model lasted over 4 years in a chilled water system.
One more thing: temperature + pressure + dirty fluid = the perfect storm for switch failure.
So what can you do? Use protective filters, select switches rated for aggressive media, and if possible, install dampers or snubbers to smooth out pressure spikes.
Mechanical vs. Electronic Life Span Differences
Let’s clear a common confusion: mechanical and electronic pressure switches are not the same when it comes to durability.
Mechanical pressure switches use springs, levers, and physical contacts. These parts physically move every time the pressure hits a setpoint. Over time, this wear and tear adds up.
Electronic switches, on the other hand, use sensors like piezoresistive or strain gauges. They have no moving parts in many designs. So the mechanical fatigue is close to zero.
Because of this, electronic switches generally outlast mechanical ones—especially in high-cycle or harsh environments.
However, don’t write off mechanical switches too quickly. They’re cost-effective, robust, and field-proven. In non-critical applications or stable environments, a mechanical switch can work trouble-free for years.
But if you’re dealing with critical systems, rapid cycling, or need precision and digital output, go for electronic. They offer longer life, better repeatability, and often come with diagnostic features.
Quick Comparison:
Mechanical: Simple, cheaper, good for basic needs.
Electronic: Smart, durable, ideal for demanding systems.
Your job is to match the switch to the environment. The wrong type in the wrong place can die fast.
How Preventive Maintenance Affects Longevity
You may have the best pressure switch in the world, but if you ignore it, it’ll fail faster.
Preventive maintenance is a game-changer. Just like we service our cars regularly—even if they don’t show problems—you should check your switches at fixed intervals.
Here’s what I recommend as a monthly checklist:
Check for dust, oil, or moisture around the switch.
Listen for any unusual clicking or delay in switching.
Check wire terminals for corrosion or looseness.
Validate if the switch triggers at the right setpoint.
Sometimes, a small debris particle can block the diaphragm movement. Or oil vapour can corrode the spring. These are preventable issues. A simple cleaning with a cloth, tightening a screw, or blowing some air can add years to your switch’s life.
In fact, in my previous plant, we extended our pressure switch replacement cycle from 12 months to 36 months just by sticking to preventive maintenance.
Another tip—log your switch behavior over time. If you see drift in actuation points, it’s a red flag.
A well-maintained switch isn’t just about saving money—it’s about avoiding surprises in mission-critical systems.
Signs It’s Time to Retire a Pressure Switch
Pressure switches don’t usually shout when they’re failing. But they do whisper in signs.
Here are 5 clear signs it’s time to say goodbye to your current switch:
Inconsistent triggering: Sometimes it activates, sometimes it doesn’t.
Visible rust or pitting on terminals or housing.
Switch delay: It triggers too late or too early.
Manual override becomes a frequent need.
System alarms or shutdowns without clear reasons.
If you see any of these, don’t ignore them. One small fault can cause costly downtime or safety issues.
Also, remember that components age—even if they still “look fine.” Springs lose tension. Diaphragms wear out. Electrical contacts corrode.
It’s like using an old tire that still has grip but is 7 years old. At some point, you don’t wait for failure—you proactively replace.
So here’s my advice: if your pressure switch has been running more than 5 years in a tough environment, start planning for its replacement, even if it’s working okay.
Retiring it at the right time is not wasteful—it’s wise engineering.
Conclusion
A pressure switch may seem like a set-it-and-forget-it device, but regular care significantly extends its lifespan. Dust, moisture, and vibration are the silent killers of many switches. Make it a routine to inspect the switch housing, wires, and terminals every few months—especially in high-use or harsh environments. Clean off dust, check for signs of corrosion, and make sure connections are tight. Use dielectric grease on terminals if exposed to moisture. Test switch response with a multimeter or by observing activation at known pressures. If your system runs 24/7, consider switching to a higher cycle-rated switch or using a backup. Also, ensure the switch isn’t cycling too frequently—this wears down internal springs and contacts. A little maintenance—tightening, cleaning, checking—can help a pressure switch last for years beyond expectations. It’s a small effort for a big return in uptime and safety.