Key Takeaway
Pressure gauges work by converting fluid pressure into mechanical movement. The most common mechanism is the Bourdon tube, which is a curved, hollow tube that straightens when internal pressure increases. This deformation moves gears connected to a pointer on the dial. Other types like diaphragm or bellows gauges use a flexible element that deflects under pressure. Digital pressure gauges operate on the same basic principle but convert the movement into electrical signals using sensors like strain gauges or piezoelectrics. The deflection or signal is calibrated to represent pressure values. This principle ensures accurate pressure monitoring in systems requiring reliable control and safety.
Conversion of Pressure into Mechanical Motion
In mechanical gauges, pressure is converted into motion through elastic deformation. Think of a Bourdon tube: pressure enters the curved tube, causing it to straighten slightly. This minute movement is multiplied by gears and levers to rotate a dial pointer.
Diaphragm and capsule gauges work similarly, but instead of a tube, a flexible membrane expands under pressure. This deflection is again translated into pointer movement.
The beauty of these systems is their simplicity. No electricity, no software. Just pressure and motion. That’s why they’re still preferred in harsh environments — where digital electronics may fail.
But remember: mechanical linkages introduce friction, hysteresis, and wear. This affects long-term accuracy. Choose mechanical gauges for robustness, and digital ones where precision and data logging are key.
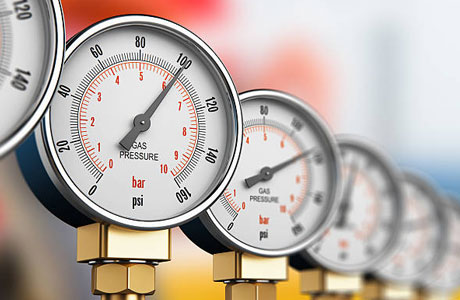
Role of Elastic Elements in Measurement
Elastic elements are the heart of mechanical pressure instruments. These elements deform in proportion to pressure — following Hooke’s Law — and include:
Bourdon tubes
Diaphragms
Bellows
Capsules
Each has its ideal use case. Bourdon tubes suit high-pressure, dry media. Diaphragms are better for low-pressure or corrosive fluids. Bellows and capsules work well in differential and low-vacuum scenarios.
Their performance depends on elasticity, material selection, and geometry. If overstressed, these elements deform permanently — leading to calibration drift or complete failure.
Understanding the elastic behavior helps engineers select the right pressure element for accuracy, longevity, and process compatibility.
Bourdon Tube Deflection Mechanism
The Bourdon tube is a curved, hollow metal tube that straightens when internal pressure rises. This deflection is converted into pointer rotation via a linkage mechanism.
The amount of deflection depends on:
Tube shape (C or spiral)
Material elasticity (brass, stainless, Monel)
Pressure intensity
Higher pressure = more deflection = more pointer movement.
But over time, the tube may lose elasticity (creep), especially after overpressure events. This leads to zero shift and inaccurate readings.
Regular calibration and using proper over-range protection preserves the tube’s integrity and reading reliability.
Diaphragm and Bellows Principles
Both diaphragms and bellows are elastic elements that deform under pressure — but work differently.
Diaphragms: Thin metal sheets that bulge with pressure. Ideal for low-pressure and corrosive fluids.
Bellows: Folded, accordion-like tubes that compress/expand. Suitable for low-pressure ranges or small differential measurements.
They’re used in:
HVAC systems
Filters
Cleanrooms
Differential pressure monitoring
Unlike Bourdon tubes, these elements handle delicate or chemically aggressive media better. They offer compact design, higher sensitivity, and are compatible with seals and flush connections.
How Digital Gauges Use Sensors
Unlike mechanical gauges that rely on elastic deformation, digital pressure gauges use sensors to convert pressure into electrical signals.The most common sensor is a strain gauge mounted on a diaphragm. As pressure deforms the diaphragm, the strain gauge’s resistance changes. This variation is converted to a voltage signal, then digitized and displayed.
Other sensor types include:
Piezoresistive sensors: Sensitive to small pressure changes.
Capacitive sensors: Change capacitance as diaphragm spacing shifts.
MEMS sensors: Used in compact applications like smartphones or wearables.
Digital gauges offer numerous benefits:
High precision
Easy-to-read displays
Data logging
Alarm thresholds
Output signals (4–20 mA, RS485, etc.)
These gauges are excellent for remote monitoring, hazardous environments, and integration into automated systems. While more expensive than analog, they eliminate human error in reading and can adapt to multiple units (psi, bar, kPa).
They also include built-in compensation for temperature, altitude, and vibration — making them ideal for critical operations where mechanical gauges fall short.
Conclusion
Whether it’s a Bourdon tube deforming under pressure, a diaphragm flexing, or a sensor converting pressure to voltage, all gauge types aim to give accurate, real-time pressure readings. While their internal principles differ, the end goal is the same: system safety, reliability, and performance tracking. Bourdon tubes work best for mechanical ruggedness, diaphragms for sensitive and corrosive environments, and digital sensors for automation and analytics. Understanding how each principle works helps users detect faults and pick the right tool. When you align the principle of operation with your measurement goal, accuracy improves. Different principles don’t mean better or worse—just fit-for-purpose design tailored to application needs.