Key Takeaway
The full form of TIA is Totally Integrated Automation.
Introduced by Siemens, TIA represents a seamless integration approach where all automation components — PLCs, HMIs, SCADA, Drives, Networking — operate under a common engineering platform (TIA Portal).
TIA optimizes productivity, reduces project complexity, minimizes engineering overhead, improves system diagnostics, and facilitates scaling future plant expansions.
It’s a key strategy supporting digitalization, cloud connectivity, and Industry 4.0 initiatives.
With TIA, Siemens offers a unified, harmonized environment, enabling faster development cycles, better asset management, and efficient maintenance of complex industrial automation systems.
Totally Integrated Automation – Siemens Definition
When we hear the term TIA, it stands for Totally Integrated Automation. This is Siemens’ revolutionary approach to streamline and simplify industrial automation systems by integrating all automation processes into one cohesive platform. Imagine a world where all automation components – from PLCs (Programmable Logic Controllers), HMI (Human Machine Interface) systems, SCADA (Supervisory Control and Data Acquisition), and drives – are interconnected seamlessly. This is exactly what TIA does.
In a traditional industrial automation setup, multiple platforms and systems would often operate in silos, making integration, troubleshooting, and maintenance a daunting task. TIA eliminates these barriers by providing a unified solution where everything from planning, design, and commissioning, to maintenance can be managed from a single platform. It’s a major leap forward in simplifying the complexities of automation processes.
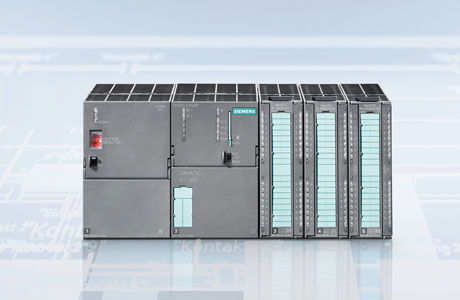
Goals Behind TIA Framework
So, what exactly is Siemens trying to achieve with TIA? The goal is simple: to simplify and optimize industrial automation by removing the need for separate systems and enabling seamless communication between different components. The vision behind TIA is to reduce complexity while improving the efficiency and flexibility of automation systems.
TIA is designed to integrate all the stages of the automation process. Whether it’s the initial engineering phase or the ongoing operational phase, the TIA framework ensures everything works together smoothly. By incorporating a central platform, Siemens aims to enhance data transparency, improve system performance, and drastically reduce the time it takes to implement automation systems. All this ultimately leads to reduced operational costs, faster time-to-market, and easier maintenance.
Advantages in Programming, Visualization, and Maintenance
The power of TIA lies in its ability to simplify several critical aspects of automation, including programming, visualization, and maintenance.
When it comes to programming, TIA provides a centralized environment where engineers can work on multiple devices and systems at once. With a unified programming environment, developers no longer need to use different software tools for different hardware. TIA’s modular approach makes it easier to scale systems and adapt them to changing business needs. This drastically reduces the time spent on programming tasks, allowing engineers to focus more on innovation and optimization rather than integration issues.
In terms of visualization, TIA allows for real-time data monitoring and visualization. With the ability to visualize operations on a single platform, operators gain complete insight into the system’s performance, enhancing decision-making and system optimization. This helps to predict potential problems before they occur, reducing downtime and increasing the system’s overall reliability.
As for maintenance, TIA provides a streamlined approach to troubleshooting and system upgrades. Thanks to its integrated nature, it is easier to monitor system performance and detect faults early. Maintenance teams have all the diagnostic tools they need in one place, ensuring a faster response time when issues arise. Additionally, Siemens’ remote maintenance options allow engineers to troubleshoot systems without being physically present, saving time and resources.
TIA Portal as the Core Engineering Tool
At the heart of Siemens’ Totally Integrated Automation strategy lies the TIA Portal. This is the software tool that enables engineers to design, configure, and program all automation systems using a single interface. It serves as the backbone of TIA, offering a seamless user experience for engineers to configure and optimize everything from PLCs to HMI systems.
The TIA Portal allows for the integration of a wide range of devices and systems from Siemens, including automation, drive, motion control, and safety devices. This makes it an all-encompassing engineering platform, enabling engineers to manage every aspect of their system from one single tool. Whether you’re designing control systems or configuring complex machine operations, the TIA Portal simplifies the task by ensuring all components work in harmony.
One of the standout features of the TIA Portal is its user-friendly interface. Engineers, even those new to the system, can easily navigate through different functionalities, reducing the learning curve. The system also offers real-time simulation and diagnostics, which help engineers identify potential issues early in the development process, further enhancing system reliability.
Comparison with Traditional Automation Architectures
Now, let’s take a step back and compare TIA with traditional automation architectures. In traditional setups, components such as controllers, drives, and HMIs were often integrated in a fragmented manner. This required engineers to use different tools for programming, visualization, and maintenance, leading to a more time-consuming and error-prone process. Additionally, communication between different components wasn’t always seamless, and integrating different systems from various manufacturers was often a challenge.
With TIA, Siemens brings everything together in a single platform. There’s no need for multiple tools or systems – everything is connected and integrated within the TIA Portal. This centralized approach eliminates compatibility issues, reduces system integration time, and improves communication across devices. The result? An optimized, highly efficient system with fewer risks, lower costs, and easier scalability.
Moreover, the TIA framework facilitates modular system design. Engineers can easily add or remove components without disturbing the entire system. This is a huge advantage compared to traditional systems, where scaling up or modifying systems often meant a complete overhaul of existing infrastructure. TIA’s flexibility and modularity allow businesses to quickly adapt to changing needs and remain competitive in an ever-evolving market.
Conclusion
In conclusion, Totally Integrated Automation (TIA) is a game-changing framework developed by Siemens to streamline industrial automation processes. By offering a unified platform for programming, visualization, and maintenance, TIA simplifies the complexities of industrial systems while enhancing system performance and reliability. Through tools like the TIA Portal, engineers can efficiently design, configure, and monitor automation systems, reducing development time and operational costs.
When comparing TIA to traditional automation architectures, the advantages become clear: a single integrated platform, better system flexibility, and easier scalability. For engineers, TIA provides an all-in-one solution that not only reduces the time spent on system design and maintenance but also helps businesses remain competitive in a rapidly changing industrial landscape. If you’re a newly joined engineer, embracing TIA will make your journey in the industrial automation world much smoother, more efficient, and certainly more exciting!