Key Takeaway
TIA stands for Totally Integrated Automation.
It’s Siemens’ strategic concept integrating all automation components — PLCs, HMIs, SCADA, drives, safety systems, and remote I/O — into a unified engineering environment.
In practice, TIA Portal is the software platform realizing this vision.
TIA ensures seamless data flow, hardware/software compatibility, faster project execution, reduced engineering time, and minimized errors.
Through TIA, users can configure devices, program logic, set up communication, design operator interfaces, perform diagnostics, and simulate system behavior — all from one project.
It supports Industry 4.0 integration, including cloud connectivity and secure networking.
TIA = Totally Integrated Automation
In the world of industrial automation, TIA (Totally Integrated Automation) stands out as a comprehensive and unified framework that is transforming how industries approach automation. At its core, TIA aims to integrate all the key automation components—such as programmable logic controllers (PLCs), human-machine interfaces (HMIs), drives, and SCADA systems—into a single, cohesive system. This integration allows for smoother communication and data flow, enabling engineers and plant operators to manage entire systems seamlessly.
When we talk about TIA, we are referring to a game-changing concept in industrial automation that enhances operational efficiency, reduces complexity, and supports digital transformation across the entire manufacturing process. For engineers who are new to this concept, think of TIA as the backbone that ties together all automation components, making it easier to monitor, control, and optimize industrial systems from a single platform.
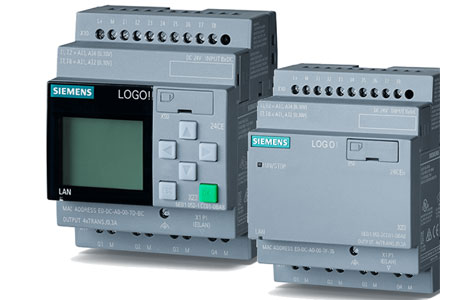
TIA as a Unified Engineering Framework
Imagine working on a large-scale automation project that involves multiple systems and processes. Without an integrated framework, engineers often face challenges like communication breakdowns between systems, inefficient troubleshooting, and complex setups that can lead to costly delays.
This is where TIA excels. By providing a unified engineering framework, TIA simplifies the design, development, and maintenance of industrial automation systems. Instead of dealing with separate software tools for different components, engineers can use a single interface to program and configure PLCs, HMIs, drives, and other essential equipment. This not only reduces the risk of human error but also accelerates the time-to-market for automation projects.
What’s more, TIA’s integration allows for easier scaling of automation systems. As your industrial processes grow, you can seamlessly add new components and integrate them into the existing framework without worrying about compatibility issues. The end result is a more flexible, efficient, and cost-effective automation solution.
Components Included: PLC, HMI, Drives, SCADA
One of the key features of TIA is its ability to integrate multiple components, all of which play crucial roles in automation systems:
PLC (Programmable Logic Controllers): These are the “brains” of the automation system, controlling processes based on programmed logic.
HMI (Human-Machine Interfaces): HMIs provide the interface through which operators can monitor and interact with the system.
Drives: These control the movement of machinery, motors, and other mechanical equipment.
SCADA (Supervisory Control and Data Acquisition): SCADA systems enable remote monitoring and control, providing real-time data to operators.
In the traditional setup, these components often functioned in silos, each requiring separate programming, configuration, and maintenance. With TIA, all these components are integrated into a single system, allowing for better communication, streamlined processes, and easier maintenance.
For example, engineers can program the PLC to communicate directly with the drive and HMI, ensuring that the system operates as a cohesive unit. This eliminates the need for manual intervention and reduces the likelihood of system failures due to communication issues.
Integration Benefits for Plant-Wide Automation
The integration of TIA brings several significant benefits to plant-wide automation. By connecting various automation components, TIA enables:
Enhanced Efficiency: With all systems integrated, engineers can monitor and optimize the entire plant from a central platform. This leads to faster decision-making and reduced downtime.
Improved Data Flow: The seamless integration of devices allows for more accurate and real-time data sharing between systems. This makes it easier to track performance metrics, diagnose issues, and make improvements.
Cost Savings: With TIA, industries can streamline their operations, leading to reduced overhead costs. Maintenance is simplified, and the need for multiple software systems is eliminated.
Faster Troubleshooting: When an issue arises, engineers can quickly pinpoint the root cause by accessing data from various components in real-time. This reduces the time needed for repairs and minimizes production interruptions.
For new engineers, this level of integration may seem like a significant leap. However, TIA’s user-friendly design and powerful capabilities make it easier to adopt and integrate into your projects.
TIA’s Role in Digital Transformation and Industry 4.0
In today’s fast-evolving industrial landscape, digital transformation is the key to staying competitive. TIA plays a pivotal role in this transformation by enabling industries to adopt Industry 4.0 principles—where machines, systems, and devices communicate with each other in real-time.
Industry 4.0 is all about automation, data exchange, and intelligent systems that enhance operational efficiency. TIA’s integration capabilities support these goals by providing a comprehensive platform for automating processes, collecting data, and analyzing performance. This data can then be used for predictive maintenance, process optimization, and even decision-making using artificial intelligence (AI) and machine learning (ML).
By using TIA, manufacturers can take their operations to the next level, embracing new technologies that support smart factories and future-proof their automation systems.
Conclusion
TIA streamlines the entire automation process, enabling engineers to develop, manage, and diagnose entire systems from a single platform. By integrating critical components like PLCs, HMIs, drives, and SCADA, TIA makes automation easier to implement, maintain, and scale. The benefits of this integration are felt across the entire manufacturing process, from increased efficiency and reduced downtime to cost savings and improved data flow.
As an engineer new to industrial automation, adopting TIA will not only make your projects more manageable but also prepare you for the future of digital transformation in the industry. TIA is more than just a set of tools—it’s the foundation of modern automation, empowering engineers to create smarter, more connected systems that drive innovation and efficiency in industrial operations.