Key Takeaway
Pressure switches are made from materials that ensure durability, accuracy, and safety. The outer body is usually made from metal like stainless steel, brass, or aluminum — materials that resist corrosion and wear. For lightweight or low-cost models, plastic housings may be used. Inside, the pressure-sensing parts like the diaphragm or piston are made from rubber, silicone, stainless steel, or Teflon, depending on the fluid type and temperature. Electrical contacts are often made from copper, silver alloy, or gold-plated metals for good conductivity and long life. Explosion-proof models use thicker metals for safety. Materials are chosen based on the environment — for example, chemical-resistant materials for acid handling, or food-safe materials for the food industry. Good material selection prevents leaks, false readings, and damage. When buying a pressure switch, always check if the materials are compatible with your system’s fluid, pressure range, and temperature.
Stainless Steel vs. Brass Housings
The housing material of a pressure switch determines where and how it should be used. Stainless steel offers excellent corrosion resistance, making it ideal for aggressive environments, chemical plants, and outdoor installations. Brass is more affordable and commonly used in residential water systems or clean air applications. Internally, materials like NBR, FKM, or silicone are chosen based on media compatibility (e.g., water, oil, gas, or steam). Choosing the wrong material can lead to corrosion, swelling, or premature failure. Always match the housing and diaphragm materials with your fluid type and temperature range. Material choice impacts reliability, cost, and service life.
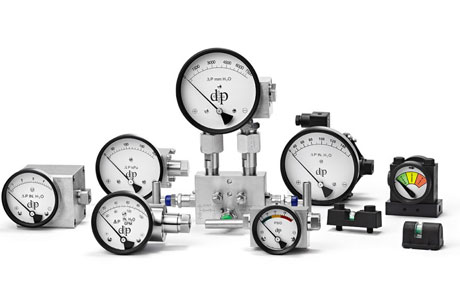
Diaphragm Materials: NBR, FKM, Silicone
Now let’s dive into the real heart of a pressure switch: the diaphragm.
This thin membrane is what senses pressure and makes the magic happen. And trust me, the material here makes a massive difference.
NBR (Nitrile Rubber) is the go-to for oil, fuel, and water-based systems. It’s affordable and has good resistance to wear. But it can crack under extreme heat or cold.
FKM (like Viton) is the premium pick. It handles high temperatures and resists aggressive chemicals. Think of applications in automotive, chemical, or process industries. It’s expensive, yes, but worth every rupee where performance matters.
Silicone is flexible and stable across a wide range of temperatures. It’s great for low-pressure applications and sensitive environments like food processing or clean rooms.
The diaphragm decides how accurately your switch responds. Choosing the wrong one? That’s a recipe for failure.
Sealing and Insulation Materials
Here’s the thing no one tells you early in your engineering journey—seals matter more than you think.
What keeps the internals safe from moisture, dust, or oil leaks? The sealing and insulation materials.
EPDM is used in water and steam applications. It holds well against weather and heat. But it’s not your guy for oil-based systems.
PTFE (Teflon) is the chemical-resistance king. It’s slippery, durable, and used in extreme industrial conditions. It’s often found in food-grade and pharma-grade switches too.
Silicone sealants are flexible and great for temperature swings. You’ll often find these in HVAC and clean environments.
Good insulation doesn’t just protect the electronics—it protects your entire system from unexpected shutdowns.
So next time you’re reviewing a pressure switch datasheet, don’t skip the sealing materials. That little detail could save a lot of maintenance headaches.
Corrosion and Chemical Resistance Factors
Let’s talk real-world. You install a pressure switch. It works fine for a few months—then rust shows up, signals go crazy, and boom—failure.
This is where corrosion and chemical resistance come in.
If you’re dealing with saltwater, acids, ammonia, or even simple cleaning agents, you need switches made from chemically resistant materials.
304 or 316 stainless steel offers great corrosion resistance. But 316 is the better choice when chloride (salt) or aggressive chemicals are in play.
Plastic-bodied switches might work for mild environments but avoid them in anything aggressive.
Elastomers like FKM or PTFE can handle exposure to chemicals, oils, and even fuels.
Ask yourself: What media will touch the switch? Water is easy. Acids and alkalis? You better double-check every material.
Failure due to corrosion isn’t just inconvenient. It’s expensive and dangerous. So always match resistance to your working conditions.
Material Selection Based on Application Type
Here’s a golden rule: the right switch in the wrong application is still the wrong switch. Different applications demand different materials—and ignoring that can cost you downtime, repairs, or worse, safety issues.
Food and beverage? Stainless steel housing, PTFE or silicone seals, and FKM diaphragms for hygiene and chemical washdowns. HVAC or general machinery? Brass housing, NBR diaphragm, and EPDM seals often do the job well at a lower cost.
Chemical industries? You need the full suit—316 stainless steel, PTFE seals, FKM diaphragm. Safety first. Water treatment? Depends on the chemical load. Clean water allows brass; chlorinated or treated water demands better materials.
Match the switch to the job, not just the specs. Talk to suppliers, understand the media, the pressure range, and the working environment. Every successful installation starts with smart material choices.
Conclusion
Material selection in pressure switches is critical to performance and durability. Stainless steel is corrosion-resistant and ideal for aggressive chemicals or outdoor use. Brass is commonly used for air and water applications due to its affordability. Internally, diaphragm materials like NBR, FKM, or silicone are chosen based on fluid type and temperature. Improper material use can lead to swelling, cracking, or inaccurate response. For food or pharma industries, hygienic-grade materials are mandatory. In corrosive or explosive zones, certified materials with special coatings are preferred. Always check compatibility charts before choosing a switch. The wrong material choice could lead to leaks, failure, or safety hazards. The right choice ensures reliable, long-term operation.